Table of Contents
Worldwide sales of the cold chain market will amount to $628 billion by the year 2028, according to a study by Grand View Research. It is forecasted to have a compound annual growth rate (CAGR) of 14.8% up to that year.
As stated in the modern world of logistics, cold-chain logistics are no longer a requirement but a strategic asset. The need for cold storage warehousing increases markedly, as does the increased challenge of operating such a highly controlled environment.
The daunting task before the industry is how to manage energy costs while maintaining temperature integrity and delivering orders quickly while ensuring the safety of its workforce.
Key Challenges in Cold Storage Warehousing
- Temperature Variations: Even slight temperature changes in cold storage can spoil perishable goods. It means continuous system monitoring and highly insulated constructions are required.
- Inventory Management: An efficient inventory is an important factor in controlling wastage and stockouts. Real-time visibility and automated stock rotate to keep optimal levels with freshness to ensure a continuous supply.
- Space Optimization: Cold storage is costly and limited in space. Office space designs, vertical shelving, or automated systems help packing more into storage without much loss in efficiency.
- Employee Safety: Cold storage causes health problems in terms of frostbite or strain. Training with the use of special protective clothing and equipment provided should ensure the safety of the employees.
- Fluctuations in Seasonal Demand: Storage at low temperatures goes through season peaks of demand at certain times of the year. Flexible processes and ampliative solutions would have to be set up to answer this demand.
Why is Cold Storage Automation Needed?
Increased efficiency, accuracy and scalability can also be attained through cold storage warehousing because demand for perishable goods usually rises beyond what manual processes can accomplish.
Automated systems include robotic picking and smart racking which can pick with less error, optimize the floor space, and reduce labor costs.
The market for cold storage warehousing has had a significant increase in value over the last several years, rising from about $115 billion in 2021 to an estimated $428 billion by 2028.
There is much more that would be included in managing consistency in handling spoilage and speedier responses to demand changes; such readily makes cold storage warehousing highly competitive and relevant in today’s modern supply chains.
Innovative Solutions for Cold Storage Warehousing
Automated Storage and Retrieval Systems (ASRS)
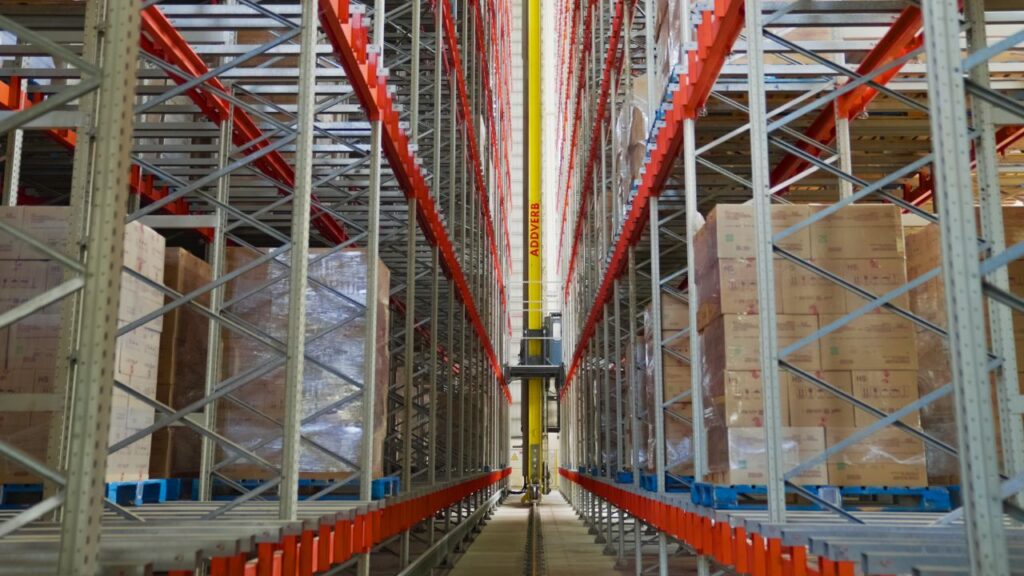
Effectiveness of ASRS
- Space Optimization in Limited Space: For example, maximize space storage in tight areas.
- Reduced Manual Labor: Through reduced human involvement, also minimized costs and errors.
- Increased Picking Efficiency: Accelerates and improves order processing efficiency.
Accelerating Productivity with ASRS Systems
ASRS solutions are essentially cold storage warehousing that boost efficiency and space usage and manage temperature-sensitive goods. The Mother-Child Shuttle automates the movement between the zones, reducing manual work.
The Carton Shuttle speeds storage and retrieval up and maximizes space. Skyron’s 4-Way Pallet Shuttle handles goods with serious weight precision; Medius optimizes vertical storage for even lower energy costs.
Cruiser and Cruiser 360 improve storage density in narrow aisles, which means capacity increases along with less labor. Streamlining operations in this way captures the ideal ambient condition for perishable items.
Mobile Robots for Material Movement
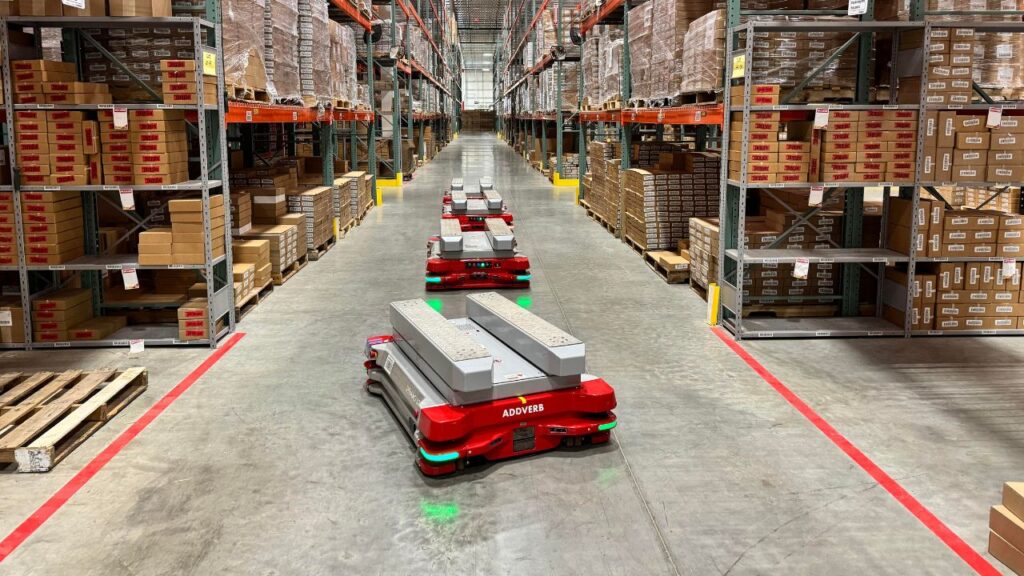
- Seamless Transport of Goods: Mobile robots make warehouse internal material transfer smooth and cost-effective, thus minimizing bottlenecks and improving throughput.
- Least Human Interference: Mobile robots would reduce human workforce dependency on material movement so that they can now devote their time to more valuable tasks.
- Increase Worker Safety: Automated systems help minimize a person’s exposure to hazardous areas and heavy lifting, which could otherwise risk injury and accident.
- Enhance Efficiency in Operations: Robots manage routing and handling to allow faster order fulfilment, better efficiencies in storage, and better space utilization.
Enhancing Material Movement with Mobile Robots: Dynamo, Veloce, and Travect
Mobile robots such as Dynamo, Veloce and Travect play a key role in improving material handling and cold storage warehousing efficiency without compromising the integrity of temperature-sensitive products.
Dynamo automates the conveyance of materials along freezing, narrow aisles, thereby reducing human exposure in hazardous conditions.
Veloce occupies space more effectively in cold storage warehousing using very optimal ways of handling load sizes, allowing for precise goods-to-person operations in even the tightest, cold storage warehousing.
Moreover, Travect accelerates pallets on its fixed rail system while maintaining the cold chain and is important in high-volume pallet handling.
Person-to-Goods Picking Systems
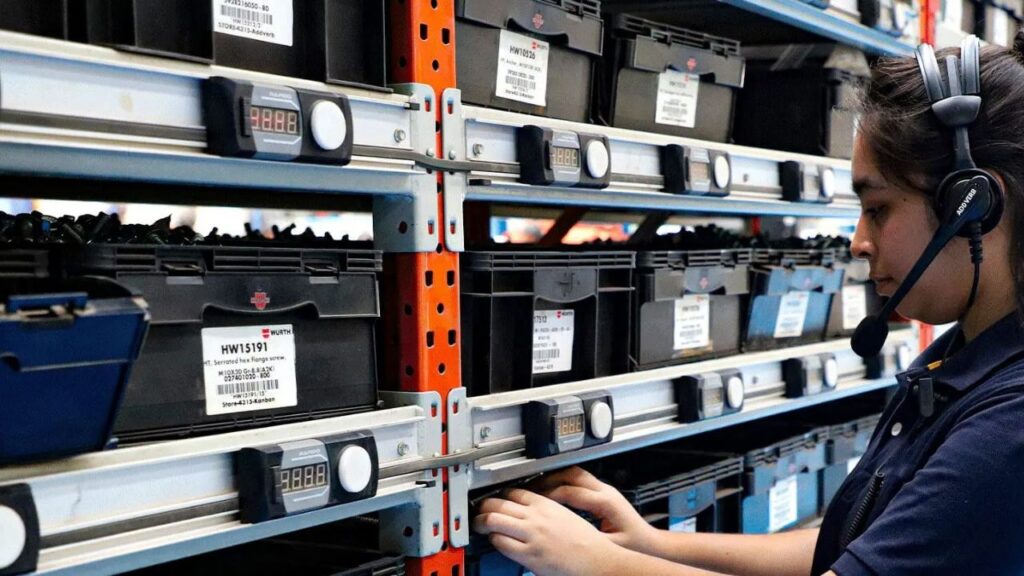
- Faster and More Accurate Picking: Person-To-Goods systems have simplified the order-picking process, thus ameliorating the amount of time spent during picking while ensuring greater accuracy which is important for any high-speed warehouse operation.
- Better Inventory Management: Real-time tracking and efficient picking allow enterprises to maintain accurate levels of stock for better inventory control and ensure fewer discrepancies in counting stocks.
- Increased Productivity among Workers: PtG has intuitive guidance for the workers through lights and voice commands to increase productivity while minimizing manual errors in picking.
- Decreased Human Errors: Minimized human error by automated handling guidance, which makes sure that the right items are picked within the right quantities.
Optimizing Order Fulfillment in Cold storage Warehousing with Person-to-Goods (PtG) Picking Systems
Rapido, for instance, is equipped with Pick-to-Light technology that directs workers to actual items for picking speedily and accurately under freezing conditions. Hence, it eliminates the use of paper or RF devices and increases inputs.
The beauty of Zesty’s Pick-by-Voice system lies in its ability to give workers voice prompts in real-time as and when necessary, thus enabling them to operate in the cold without the hassle of holding handhelds.
These types of systems enable workers to process very fast and also quite accurately, thus maximizing the whole process of collecting volumes of inventory inside a cold storage warehousing where speed, precision, and efficiency direct the handling of perishable products.
The Role of Automation in Addressing Cold Storage Challenges
- Temperature Control Improvement: Automation in temperature control will be without human intervention, with robots and automated systems to reduce the openings of doors, reduce cold air exposure through human presence, and move cold products into storage without long detention. Effective cold chain that takes care of this type of preservation.
- Safety for Workers: Automation is going to minimize human exposure due to harsh cold temperatures and, additionally, voyaging with manual handling of heavy or dangerous items. Thus, potential cold effects injuries, fatigue, and accidents will be lessened, making the working environments of those employees working in cold storage places safer.
- Cost Savings & Flexibility: Automation gives savings in labor costs by replacing human tasks and creating efficient operations. It also offers scalability because the systems can be easily expanded or refitted to cater to great variations in demand, which gives the flexibility to manage the spikes and changes in product volume that generally occur seasonally and require little capital investment.
- Better Visibility of Inventory: Automated systems offer inventory real-time tracking and monitoring, which allows accurate stock counts and enhances inventory turnover management. Visibility prevents stockouts or overstocking and avoids spoilage for perishables, making stock levels match demand and reduce waste.
Conclusion
Automation is needed keeping in regard the pace with changing world and within it, cold storage logistics are evident, various automation solutions like ASRS Systems, Sorting Robots, Mobile Robots, and Person-to-goods Picking Systems from Addverb bring benefits like space optimization, efficiency, and safety.
They reduce the physical load of human manpower considerably as well as minimize human error and streamline operations so that they are competitive and operational requirements of the warehouse-keeping-in-future-vision of the ever-increasing demands of temperature-sensitive commodities.
Prepared to transform your cold storage operations completely? Contact us today to find out how Addverb can automate your cold storage warehousing , thereby improving the efficiency and growth of your warehouse operations.
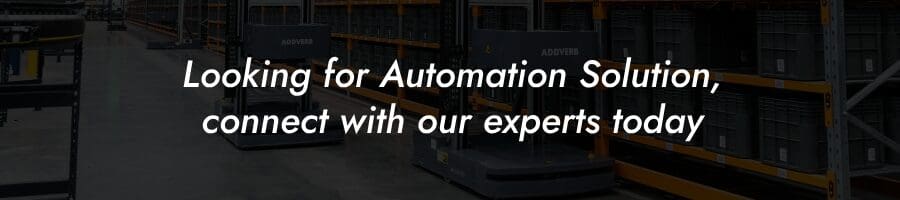
FAQ
What are the key challenges in cold storage warehousing?
Temperature control, inventory management, space optimization, employee safety, and fluctuations in seasonal demand are major challenges.
Why is automation essential in cold storage warehouses?
Automation enhances efficiency, accuracy, and scalability, helping to manage increased demand, reduce errors, and optimize space.
How do mobile robots improve cold storage operations?
Mobile robots streamline material handling, reduce human exposure to hazardous environments, and improve order fulfillment efficiency.