Table of Contents
Warehouse management encompasses the coordination, supervision, and upkeep of all warehouse activities to ensure optimal efficiency.
Despite automating specific processes, errors, and obstacles can still arise in warehouse operations. This blog will address prevalent problems in warehouse management and provide strategies to avoid them. Let’s get started!
Warehouse Management
Warehouse management involves overseeing the daily operations within a warehouse, which includes receiving goods, organizing storage space, scheduling labour, managing inventory, and fulfilling orders. Effective warehouse management requires optimizing and integrating these processes to ensure that all aspects of the operation work cohesively, thereby enhancing productivity and minimizing costs.
Challenges in Warehouse Management
1. Optimising storage layout: A poorly configured warehouse proves that the warehouses are not utilised efficiently, indicating a waste of resources. This can impact profitability as more time is spent finding the product, leading to lower order fulfilment.
2. Handling seasonal fluctuations: Seasonal changes and economic patterns can all influence client demand. Changing customer demand is one of the challenges in warehouse management.
3. Inaccurate inventory information: The manual process of updating inventory information can lead to improper stock information, the buildup of obsolete inventory, causing errors and confusion.
What are the Common Problems in Warehouse Management?
1. Poor damage control: Damage is one of the common problems in warehouse management, as it deals with large amounts of inventory and high-duty equipment. It is essential to employ regular inspections, install rack protectors, guard rails, and anti-lock systems, inspect and monitor for water damage or pests, and take respective precautions.
2. Addressing high operational costs: Labor, rent, utilities, and equipment are all significant operating expenses for warehouses, which is one of the common problems in warehouse management.
3. Inaccurate inventory tracking: Maintaining accurate inventory records is one of the common challenges and problems in warehouse management faced by warehouse managers. It may cause delayed shipping of the products, which causes miscalculations due to inventory processes performed manually by several companies. It is essential to have state-of-the-art software with real-time inventory management features.
Read More: Optimus Warehouse Management System – optimising inventory
How Do Manual Processes Affect Warehouse Operations?
1. The impact of human error
As the manual process involves being super-dependent, it may invite a high probability of mistakes resulting in customer dissatisfaction, order discrepancies, and calculations. Following are the various warehouse manual challenges faced by warehouse managers:
- Picking errors: A warehouse operator may misinterpret a handwritten order or SKU, resulting in the incorrect product being selected from the shelf.
- Packing errors: A warehouse operator may misinterpret a handwritten order or SKU, resulting in the incorrect product being selected from the shelf.
- Shipping errors: If the shipping address is manually transcribed, there is a chance that the incorrect address will be entered, leading to the product being delivered to the wrong destination.
- Labeling errors: Manual application of shipping labels may cause misinterpretation and a high chance of labeling errors, leading to more discrepancies in order processing and shipment.
- Processing delays: Manually handling the inventory records and hand-sorting on paper makes it challenging to ship and fulfill orders promptly.
According to a report, 92% of employees admit to wasting up to 8 hours per week looking for the proper information and data to service clients. Meanwhile, 24% lose up to a full day of productivity each week trying to get this information across all industries.
2. Increased labour costs
Many factors have increased employment expenses. Industries that rely significantly on the EU workforce need help finding both skilled and unskilled workers, causing warehouse managers to face several manual challenges.
Automation in warehouses becomes a critical investment, allowing businesses to shift employees from manual and redundant tasks to more valuable tasks requiring human judgment and problem-solving abilities such as strategic planning, data analysis, and process improvement.
How Can Inventory Management Be Optimised with Addverb Technologies?
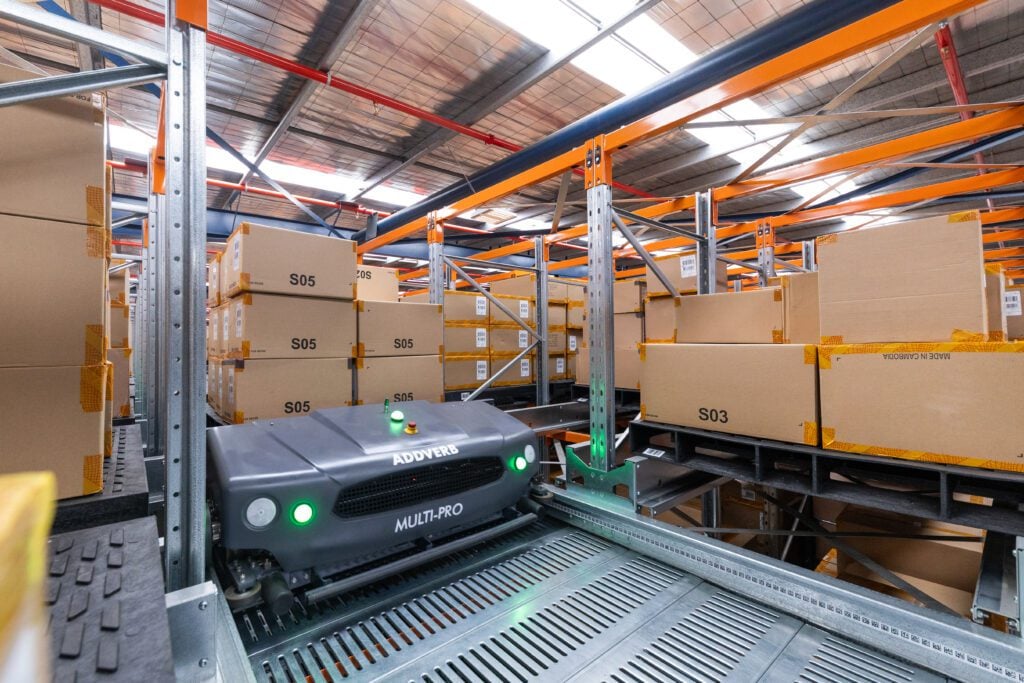
1. Efficient labor scheduling
Addverb Technologies’ carton shuttle improves labor efficiency in warehouse management by automating retrieval and storage, decreasing the need for manual handling. It also optimises area utilisation and expedites picking, reducing worker travel time.
They are designed to move goods swiftly and efficiently from one location to another, resulting in increased production and streamlined operations. Carton shuttles can help organise products in the warehouse, making it easier for employees to find and collect items as needed.
2. Adopting warehouse management systems (WMS)
Addverb’s Optimus is a highly adaptable WMS that uses cutting-edge practices to improve warehouse operational efficiency.
Benefits of using Optimus Warehouse management (WMS)
- Enhanced warehouse management: It offers real-time visibility of the inventory, enabling accurate record keeping. This helps to reduce stockout situations, thus avoiding discrepancies in shipment delays.
- Data-driven insights: Optimus offers real-time insights that ensure efficient decision-making in warehouse operations.
- Error reduction: Several integrated automation features, such as barcode scanning, help minimize manual errors, ensuring accurate order fulfilment.
- Enhanced efficiency: By leveraging resources, balancing workloads, and optimising operational flow, Optimus ensures enhanced efficiency and productivity in warehouse management.
3. Integrating automation and robotics
Addverb’s Dynamo is an automation robot that transports material and goods within a factory or warehouse.
- It is equipped with advanced sensors and mapping technology, which ensures efficient transport of goods in the warehouse without manual intervention and helps reduce warehouse manual challenges.
- Our robust autonomous mobile robots are highly designed industrial robots with Light Detection and Ranging Technology (LiDAR) and cutting-edge software. They enable efficient transportation of goods in the warehouse, ensure high safety, and have advanced navigating capabilities.
Benefits
- Material movement: Automated Mobile Robots (AMRs) can transform warehouse operations by speeding material movement, enhancing efficiency, and ensuring safety. These robots can roam the warehouse autonomously, picking up and transferring products to their designated areas, reducing the requirement for manual labor and lowering the danger of occupational injury.
- Picking: Rapido’s pick-assistant technology can improve warehouse picking processes by enhancing speed, accuracy, and efficiency in order fulfilment. The pick-assistant technology assists workers in identifying the correct products and their places, minimising the possibility of errors and enhancing efficiency.
- Tugging: A Dynamo designed for tugging activities can quickly transfer huge goods within a warehouse. These duties may include transporting pallets, carts, or other heavy equipment that might need help to handle manually.
4. Utilizing data analytics for better decision-making
Addverb’s data analytics may help organisations gain useful insights into crucial indicators such as inventory performance and replenishment speed. This ensures they have just enough product to meet demand and a little buffer supply to smooth out unexpected spikes in demand or problems refilling.
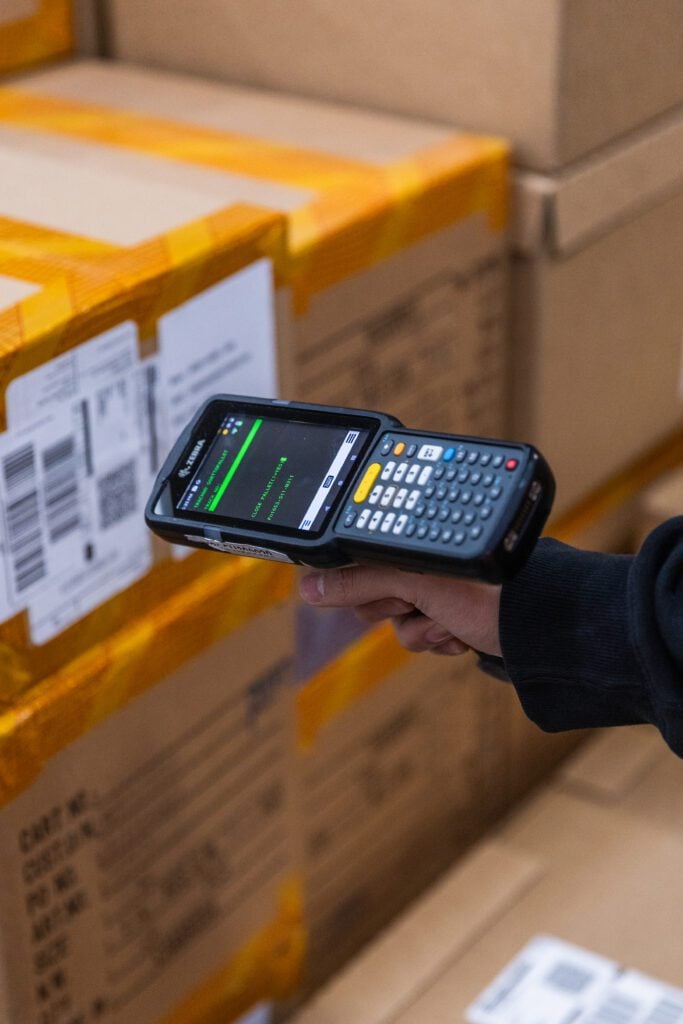
Wrapping Up
We hope the above-listed pointers gave you insights on how to combat problems in warehouse management, reduce warehouse manual challenges with the help of our automation robots, specifically designed to streamline operational efficiencies, improve labor operations by offering real-time insights and cutting-edge automation features, and help you gain a competitive edge over others.
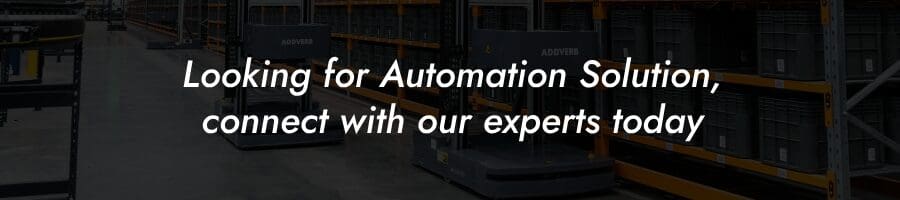
FAQ
What are the most common operational challenges in warehouse management?
Key challenges include inventory inaccuracy, poor space utilization, order fulfillment errors, labor shortages, operational inefficiency, technology integration issues, and safety hazards, all impacting productivity and costs.
How can inventory accuracy be improved?
Inventory accuracy can be enhanced through regular audits, using automated systems like RFID and barcodes, and establishing clear procedures for handling and recording inventory.
What strategies can enhance space utilization in a warehouse?
Optimizing space involves efficient layout design, utilising vertical storage, slotting analysis for item placement, and cross-docking to reduce storage time.
How can order fulfillment errors be minimized?
To minimize errors, adopt automated picking systems, implement order verification processes, provide staff training, and use a WMS for streamlined order fulfillment.
How can warehouses improve operational efficiency?
Enhance efficiency by mapping processes to identify inefficiencies, applying lean principles, using data analytics for decision-making, and fostering continuous improvement.
What are the best practices for integrating new technologies in warehouse management?
Integrate new technologies by conducting a needs assessment, phased implementation, training and support for employees, and collaborating with vendors for seamless integration.
Founded in 2016, Addverb offers complete robotics solutions for warehouse and industrial automation, with a strong global presence through its subsidiaries worldwide. The company provides a range of in-house automation products, including Autonomous Mobile Robots, ASRS, and sorting technologies. It serves over 350+ clients, including well-known companies such as Coca-Cola, Amazon, and DHL.