Table of Contents
Implementing appropriate strategies can streamline inventory management. Whether your enterprise is a small business or a sizable warehouse, the importance of maintaining an orderly inventory report must be maintained.
In this blog, we will examine five efficient strategies for creating inventory reports, accompanied by illustrative examples to assist you in selecting the most suitable approach for your specific requirements.
This encompasses both traditional manual methods and sophisticated inventory management software solutions.
What is an Inventory Report?
An inventory report is a detailed list of every product your company has on hand, including raw materials, work-in-process items, and finished goods. An inventory report should include the product name, SKU number, description, price, and quantity.
It assists organisations in tracking and managing inventory levels, providing important data to inform decisions related to purchasing, sales, and production. Inventory reports can be generated manually or automatically through inventory management software and are crucial for ensuring efficient stock management and preventing issues such as stockouts or overstocking.
What are inventory reports used for?
Stock level monitoring: Inventory lists are pivotal as they help track the stocks and ensure they meet customer demand.
Reorder point identification: This helps identify which stocks have replenished and require replacements. It also ensures that stockout issues in the warehouse are solved.
Cost Control: It aids in budget and cost management by identifying inventory carrying costs.
Demand forecasting: Inventory reports help plan for seasonal fluctuations or demand spikes.
Operational efficiency: Optimizing storage and retrieval processes helps streamline warehouse management operations.
Regulatory compliance: Ensures compliance with regulatory and industry standards for inventory tracking and reporting.
ALSO READ: Vendor Onboarding Process – Prerequisites of Warehouse Management System
5 Ways To Create Inventory Report
Manual Inventory Lists
This is a traditional method used by various business models. It involves manually counting each item of the business, such as raw materials or stocks, as there is usually a limited inventory.
Example: A small local bookstore might use a physical book to list all the books written by various authors by hand.
Spreadsheet Software
This is usually used by business models that require sophisticated details. They use top-notch software like Google Sheets and Excel to create digital inventory lists. It helps in appropriate sorting and filtering, enabling easy calculations.
Example: A boutique clothing company may use an Excel spreadsheet to maintain inventory, listing goods with columns for product names, sizes, colors, and numbers and utilising algorithms to compute the total stock value.
Inventory Management Software
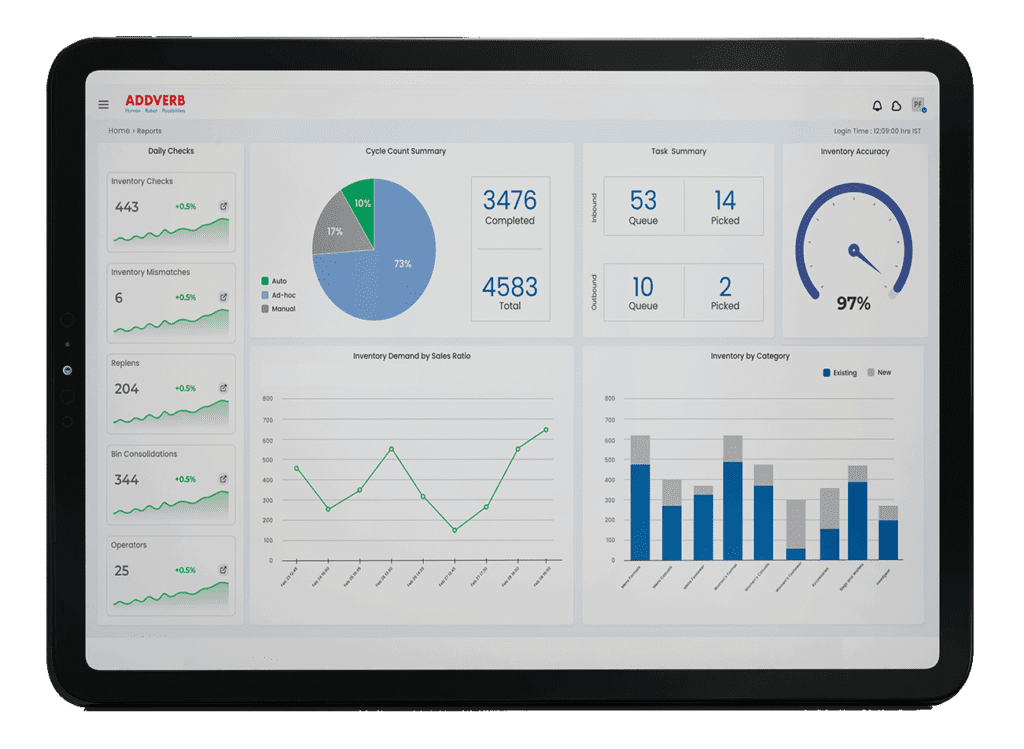
Inventory management software streamlines inventory tracking by including advanced capabilities such as real-time updates, barcode scanning, and connectivity with other corporate systems. This strategy is appropriate for warehouses with more excellent stocks and more complex needs, as it improves efficiency and accuracy.
Example: A large distribution warehouse may utilise software to manage its inventory, automatically updating inventory levels as shipments arrive and orders are fulfilled. The software can also create thorough statistics and analytics about inventory performance.
Advanced systems like Addverb’s software streamline inventory with real-time updates and automation.
Barcode Scanning Systems
Barcode scanning technologies make inventory easier by allowing warehouse staff to scan merchandise using handheld devices swiftly. This reduces human error, speeds up data entry, and maintains accurate inventory records.
Example: A logistics warehouse may utilise a barcode scanning system to assign a barcode to each item. Staff use scanners to record arrivals, movements, and dispatches, ensuring that inventory data is updated in real time.
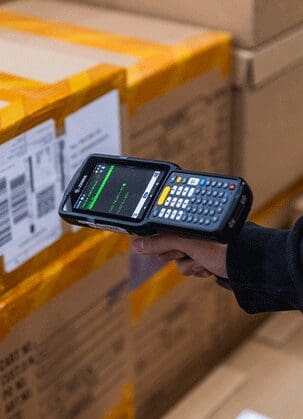
Mobile Apps
Mobile inventory management tools enable you to handle stock from any part of the warehouse through your mobile device, such as a smartphone or tablet. These applications typically offer functionalities such as barcode scanning, stock monitoring, and instant data synchronisation.
Example: A distribution centre might employ mobile applications to enable staff to carry out stock checks, monitor deliveries, and adjust inventory amounts while moving around. The portability of these applications enhances the effectiveness of operations.
ALSO READ: 12 Challenges of Inventory Management and their Solutions
Reasons to Automate Your Inventory Report
Enhanced Accuracy
Automations prevent errors such as miscounting or incorrect data entry, ensuring accurate and up-to-date inventory records.
Time Efficiency
Automation speeds up inventory tracking, reducing the burden on staff members primarily involved in data entry.
Real-Time Visibility
Automated systems provide real-time information, offering visibility into stock availability, orders, and replenishment, thereby improving decision-making.
Cost Savings
By eliminating manual work and effectively managing inventory, automation results in significant cost savings.
Enhanced Scalability
Automation systems can easily accommodate business growth without requiring extensive adjustments for large inventory.
Better Demand Forecasting
Automated data facilitates accurate forecasting and supply scheduling, enabling consumption forecasts to be seamlessly integrated into the supply chain.
Minimized Stockouts and Overstocking
Automation provides early alerts for low stock, ensuring optimal stock levels to meet customer demand. This helps avoid missed sales opportunities and excessive inventory costs.
Streamlined Compliance and Auditing
Automation simplifies record-keeping for regulatory compliance and facilitates the auditing process through improved accuracy.
Increased Operational Efficiency
Integration of inventory automation with systems such as WMS and ERP enhances overall operational efficiency.
Improved Customer Satisfaction
Effective inventory management enables the company to fulfil customer needs promptly, leading to increased customer satisfaction.
Addverb: Inventory Reporting made easy
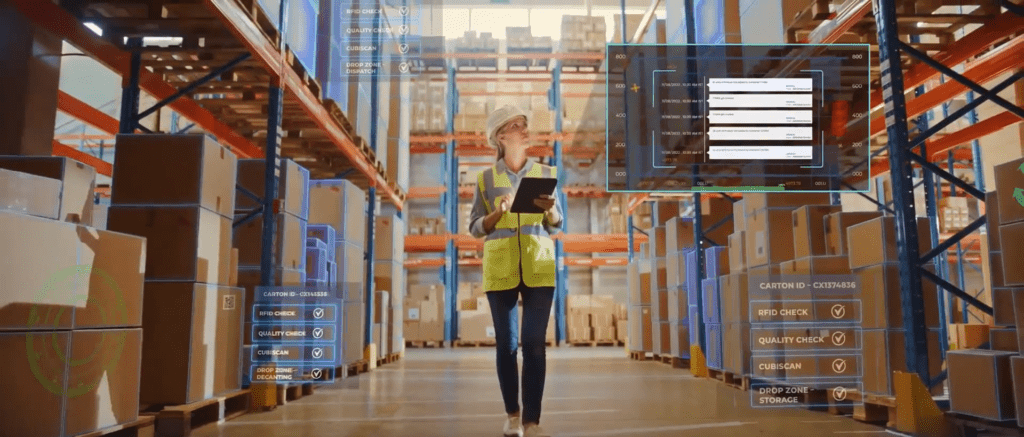
Our Warehouse Management System (Optimus) software simplifies inventory tracking by integrating advanced automation technologies and robotics. With real-time updates, easy integration, and advanced reporting capabilities, our technology provides efficient and accurate inventory management.
It enables flexible automation, optimises inventory control, and improves order accuracy, increasing overall operational efficiency.
Robots automate monotonous jobs, enhance precision, and free up human workers for more complicated tasks, making warehouse management smarter and more efficient.
End Note
Streamlining inventory management is crucial for operational efficiency and accuracy. The five strategies—manual lists, spreadsheet software, inventory management software, barcode scanning, and mobile apps—offer tailored solutions for different business needs. Embracing automation, like Addverb’s Optimus WMS, enhances accuracy, scalability, and real-time visibility, ultimately boosting operational efficiency and customer satisfaction.
Founded in 2016, Addverb offers complete robotics solutions for warehouse and industrial automation, with a strong global presence through its subsidiaries worldwide. The company provides a range of in-house automation products, including Autonomous Mobile Robots, ASRS system, and sorting technologies. It serves over 350+ clients, including well-known companies such as Coca-Cola, Amazon, and DHL.