Table of Contents
In the fast-paced world of e-commerce, effective reverse logistics and return management are now essential elements of a successful supply chain strategy.
Robust reverse logistics procedures help businesses manage returns more efficiently, lowering expenses, increasing customer happiness, and advancing sustainability.
In the cutthroat world of e-commerce, this holistic approach guarantees that returned goods are handled quickly, optimising value recovery and bolstering a satisfying customer experience.
What is Reverse Logistics?
It is a form of supply chain management that involves the movement of goods from customers back to the sellers or manufacturers. After a customer receives a product, activities like returns or recycling necessitate the implementation of reverse logistics.
The process begins with the end consumer and moves in the opposite direction through the supply chain, either from the distributor to the manufacturer or from the manufacturer to the distributor.
To simplify Ajio’s returns handling and warehouse operations, Addverb provided an advanced sortation solution using a fleet of Zippy Sorting Robots, managed by the Movect Fleet Management System.
Main components of Reverse Logistics
- Returns management involves managing returned items in a business, which includes receiving, inspecting, restocking, or disposing of them efficiently. The main goals are to reduce costs, increase value recovery, and enhance customer satisfaction. Return management activities are usually very fast and controllable by the store operators. This involves re-returning the product in case the customer finds it faulty or broken. This scenario occurs with custom-made items.
- Refurbishing and Remanufacturing: The processes involved in repairing, reconstructing, and refurbishing products are essential for companies. They salvage interchangeable, reusable components or materials from other products, a practice commonly referred to as part cannibalization. Refurbishment includes disassembling, cleaning, and reassembling products.
- Recycling and Waste Management: When products reach end-of-life and are no longer useful, customers usually send them for recycling. Manufacturers dispose of these products or recycle them.
In 2023, the reverse logistics market in the world was valued at US$ 646.7 billion. Looking ahead, studies reveal that the market would increase at a rate of five percent (CAGR) from 2024 to 2032, reaching US$ 1,008.4 billion.
Revolutionising Reverse Logistics with Addverb Technologies
1. Sortation: Our sortation automation system can overcome several challenges by automating the sorting process, ensuring that returned items are handled efficiently, precisely, and quickly.
- Employees can use Zippy to be guided in real-time to the exact location of an item, minimising the need for manual sorting and reducing errors.
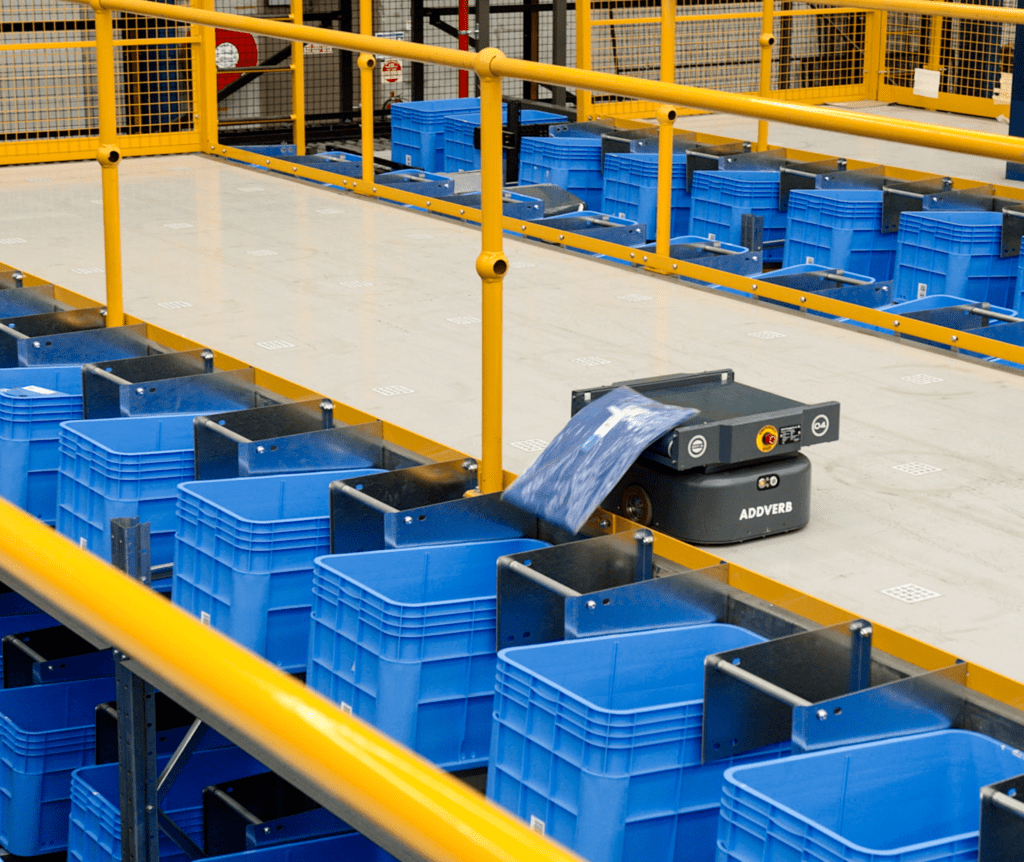
2. Picking: We apply pick automation systems to improve warehouse productivity, accuracy, scalability, and cost-effectiveness in reverse logistics operations, eliminating the need for additional labor or resources.
- Rapido: Our automatic picking system directs staff in real-time to the exact location of an item, avoiding human sorting and errors.
3. Storage: Quadron, our Automated Storage and Retrieval System (AS/RS), is utilised in storage optimisation, transferring things quickly and effectively, allowing higher output and streamlined procedures.
4. Warehouse Execution System: Our system helps to monitor the flow of the return process, ensuring that each activity is completed in the correct order and that the right persons are notified when necessary measures must be taken.
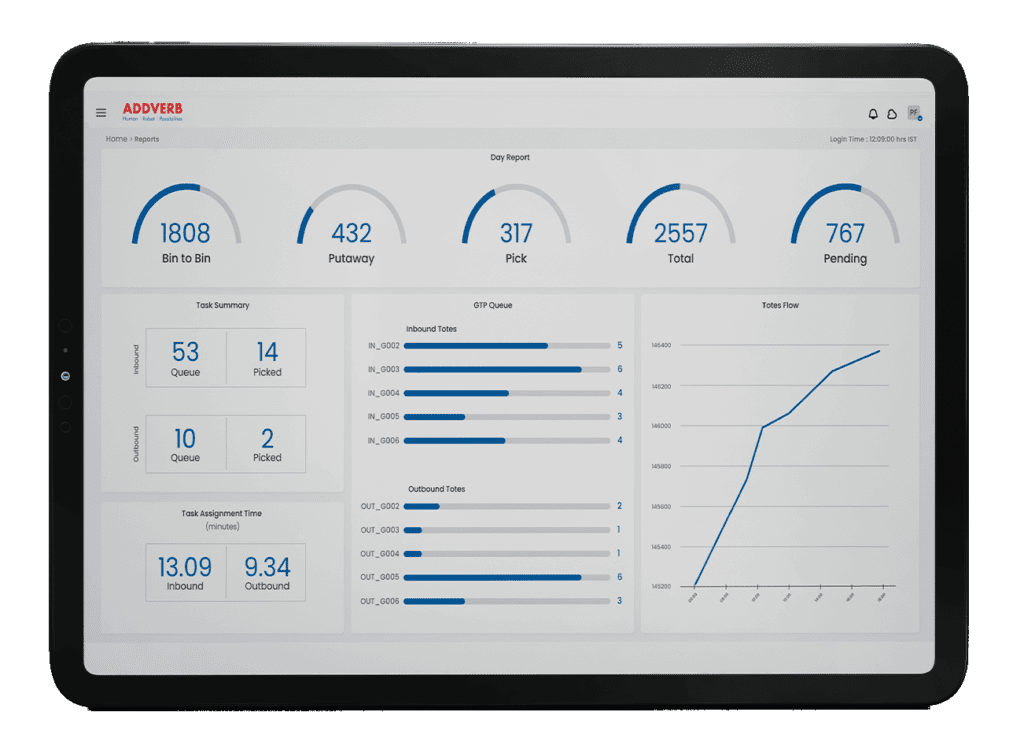
Benefits of Implementing Reverse Logistics
1. Cost Savings: Our proficiently managed reverse logistics solutions contributes to cost savings for your business. For instance, you can reduce administration, repairs, tech support, quality assurance, marketing, and disposal expenses. Additionally, providing economy shipping enables potential savings on transportation.
2. Operational Flexibility and Agility: Reverse logistics enhances the business’s operational flexibility and agility by enabling it to quickly adapt to repairs, returns, and recycling processes. It ensures a smooth operational workflow and enhances productivity.
3. Supply Chain Resilience: Reverse logistics makes the chain more resilient to market changes and disruptions by offering other paths for product recovery and reuse, guaranteeing continuity and lowering reliance on new raw materials.
4. Enhanced Customer Satisfaction: Concentrating on customer retention is a key strategy for achieving your business objectives. Acquiring new customers is more challenging than retaining existing ones.
Did you know? 96% of consumers are likely to make repeat purchases from the same merchant after a favorable experience, attracting new customers can be more difficult than retaining existing ones.
Few services that can enhance Reverse logistics for customers
- Offering free return shipping
- Providing customers with a full refund
- Not mandating that customers return the original packaging.
Process
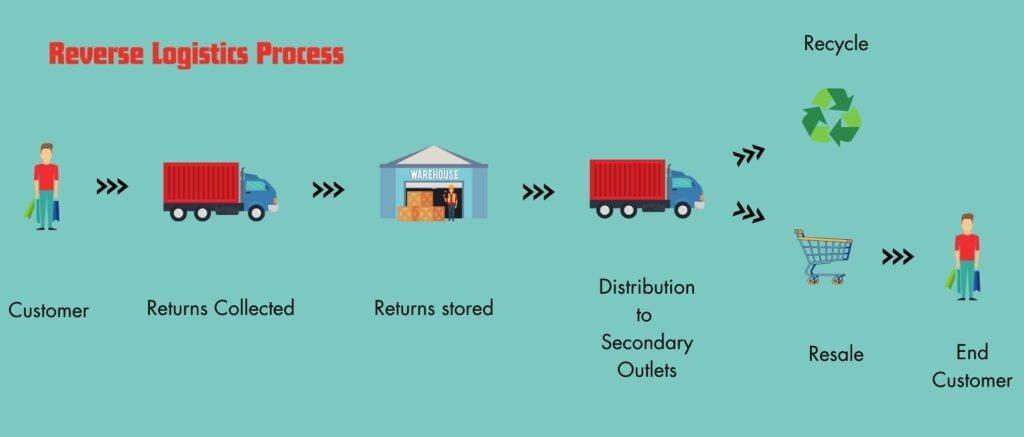
How Is Reverse Logistics Integrated into Supply Chain Management?
1. Strategic Planning and Implementation: Reverse logistics in supply chain management is integrated through strategic planning and implementation, which includes an efficient return process, recycling products, and leveraging technology for inspecting the returned items for sorting, storing, and processing them. We at Addverb ensure that your inventory management is improved with our advanced reverse logistics solutions.
2. Cross-Functional Collaboration: Logistics solutions integrate cross-functional collaboration across several departments, such as IT and sales, to configure and perform cohesive and effective return and repair management, provide real-time visibility on inventory, and make insightful decisions.
3. Technology Integration: Supply chain management and reverse logistics are integrated with advanced technologies like IoT, AI, and blockchain technology, which help to manage returns, optimise route tracking, and enhance visibility, enabling higher inventory control.
4. Customer Relationship Management: Reverse logistics in supply management contributes to overall customer satisfaction through effective and efficient return options, thus retaining them as happy customers.
Don’t forget to check out our blogs for more on these fascinating topics!
Wrapping Up
We hope the above-listed pointers gave you valuable insights as to what reverse logistics is in supply chain management, the return management intricacies, and how it benefits organisations with enhanced operational efficiency and inventory control, leading to overall customer satisfaction.
Get in touch with Addverb Technologies, and give us a chance to streamline your operations with our advanced reverse logistics and automated solutions, which enhance your customer satisfaction and help you gain a competitive edge with cost-effective strategies.
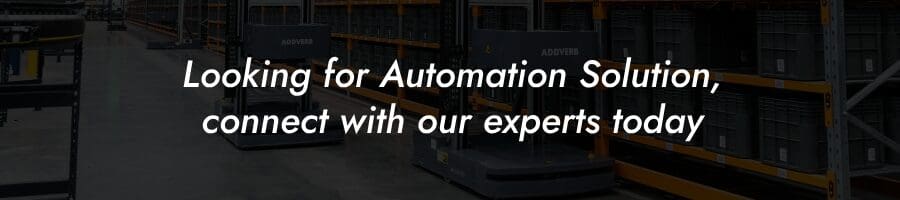
FAQ
what is reverse logistics in supply chain?
In warehouse automation, reverse logistics refers to the automated method of managing returned products, surplus stock, or damaged items from the customer to the warehouse for restocking, refurbishment, recycling, or disposal. Reverse logistics includes automated systems, such as robotics, conveyor belts, and AI applications, to create an efficient and accurate return process.
By using reverse logistics in warehouse automation systems, companies can reduce labor costs, lower mistakes and increase operational efficiency, a benefit of utilizing reverse logistics is enhanced sustainability, using products again, and recycling. This is important for e-commerce and retail.
What is reverse logistics?
It involves moving goods from their destination back to the manufacturer or a facility for returns, repairs, recycling, or disposal, ensuring efficient and sustainable management of returned products.
Why is reverse logistics important?
It is essential for enhancing customer satisfaction through efficient returns, reducing costs related to waste and inventory management, minimizing environmental impact through recycling, and ensuring compliance with regulatory requirements.
What are the key components of reverse logistics?
Key components include returns management (handling product returns), remanufacturing and refurbishment (repairing and refurbishing products), recycling and disposal (processing products to reduce environmental impact), and asset recovery (retrieving valuable components).
How does reverse differ from traditional logistics?
Traditional logistics focuses on moving goods from the manufacturer to the customer, while reverse logistics handles the return flow from the customer back to the manufacturer or facility, often involving additional processes like refurbishment and recycling.
What are the challenges?
Challenges include managing the logistics of returns, controlling operational costs, tracking returned inventory, and ensuring environmentally friendly disposal and recycling practices.
Founded in 2016, Addverb offers complete robotics solutions for warehouse and industrial automation, with a strong global presence through its subsidiaries worldwide. The company provides a range of in-house automation products, including Autonomous Mobile Robots, ASRS, and sorting technologies. It serves over 350+ clients, including well-known companies such as Coca-Cola, Amazon, and DHL.