Table of Contents
Consumer Trends Driving Change
The retail landscape is gaining a significant transformation with evolving consumer demands and preferences. The rise of the e-commerce sector demands faster delivery times, with the increase in the instant fulfilment of online orders, leading them to evolve rapidly.
Micro fulfilment centers are compact, automated warehouses focusing on order fulfilment and delivery that are situated near the final customer. As speed, convenience, and efficiency continue to be prioritised by consumer trends, Micro Fulfilment Center are becoming an increasingly important part of the retail infrastructure of the future.
In this blog, we will examine several factors influencing the e-grocery sector’s momentum and explain how Addverb’s automated warehouse solutions and picking robots are pivotal in enhancing this flow of operations. Let’s get started!
Challenges in E-Grocery and Solutions
Picking Time and Last-Mile Delivery Issues
Last-mile delivery and picking time are promises that the micro fulfilment center would take care of.
Since selecting an eGrocery order usually takes sixty minutes, many retailers find the market unprofitable. The micro fulfilment center cut the picking time down to about six minutes.
Installing these micro fulfilment centers in supermarkets’ layouts enables a hyper-local option that reduces last-mile delivery costs.
Fluctuating Consumer Demand
Variable consumer demand is a familiar actor rather than merely a COVID phenomenon.
For instance, consumers may avoid platforms that don’t allow instant resource allocation when client order fulfilment delays exceed industry norms and produce a perception of scarcity.
Consequently, businesses likely find that their Internet sales arena could have been more successful than anticipated.
Micro fulfilment center tactics in back rooms and dark stores might need help to handle unexpected client demand on a large scale. Retailers cannot afford to risk product scarcity and declining consumer confidence.
Infrastructural Investment Risks
Rapidly changing technology and the upfront costs of installing it can cause severe trajectory diverges when the equipment becomes obsolete sooner than planned.
This could cause huge operational problems, impacting the operational workflow and making it more inefficient than anticipated.
Replenishment Challenges
Grocery items have severe, unpredictable demand patterns. Factors such as seasonality and changing consumer preferences can cause sudden spikes or drops in demand, affecting the efforts.
- Stock levels: Maintaining stock levels is a challenging task, as overstocking can lead to the waste of perishable goods, and understocking can lead to stockouts.
- Supply chain inefficiency: Maintaining coherent coordination among suppliers can be challenging due to variations in supplier reliability or order processing times.
Automation: Enhancing Efficiency
Cost Reduction and Staff Optimization
Integrating with self-driving delivery trucks, the fulfilment process may be fully automated, from selection to delivery. They help enhance productivity, reduce manual errors in handling operations, and improve customer satisfaction.
Human error is the primary cause of about 80% of shipping variations in well-defined sectors. Order fulfilment is optimised when automated procedures, including those on micro-fulfillment centres, are integrated. This effectively reduces errors of this kind. |
Improving In-Store Experience
Implementing automation and top-notch technology helps reduce operational costs. In a nutshell, it reduces the need for a larger task force, enabling it to work on high-value-oriented tasks, thus making it a cost-effective option.
Innovations in Future Supermarkets
Future supermarkets will integrate several top-notch technologies, such as AI, IoT, and advanced robotics, which will help optimise tasks.
They will enhance operational efficiency, offer personalised shopping experiences, offer real-time insights on inventory management, and encourage sustainable practices.
The micro fulfilment centre will focus on enhancing personalised product recommendations and tailored experiences, improving customer satisfaction.
It will help you track key metrics like order processing times, design an efficient center layout, and use space-saving configurations.
Discover more insightful content by exploring our other blogs!
Embracing Retail Evolution with Addverb’s Retail Solutions
Experience Retail Innovation: ITC’s Journey with Addverb’s Automated Warehouse Solutions
Robotics and Automation Implementation
Our Autonomous Mobile Robots (AMRs) can completely transform warehouse operations. They can streamline material-moving processes, increase efficiency, and guarantee safety.
A. Autonomous mobile robots: Dynamo’s pick-assistant technology, Dynamo, revolutionises warehouse picking procedures by improving order fulfilment speed, accuracy, and efficiency.
- With its tugging capabilities, Dynamo can quickly move large items around a warehouse. Pallets, carts, and other heavy machinery may need to be moved, which can be difficult for employees to accomplish by hand.
B. Storage optimisation: Quadron can help optimise storage space by arranging items practically and effectively. In high-density storage systems, it can stack and store cartons.
Fulfillment Process Optimization
Addverb’s retail solutions improve fulfilment through the integration of cutting-edge technology that expedites each stage of the process, from order receipt to delivery.
Our automated systems, like AMRs, offer real-time insights as orders are picked, sorted, and shipped with exceptional speed and accuracy. They help to reduce manual errors and optimise the inventory management workflow.
Flexibility in Fulfilment
Our automated solutions offer unparalleled flexibility in the order fulfilment process, accommodating various order volumes and managing fluctuating demands.
Pick-assistant robots from Dynamo storage optimisation tools from Quadron enable smooth scaling and quick responses to shifting market conditions.
This flexibility guarantees that organisations can satisfy consumer expectations regardless of order size or complexity by maintaining high service levels and operational agility.
Benefits of Micro Fulfilment Centers
Faster order picking: Micro fulfilment center reduce the time it takes to pick up orders and enable quicker delivery by being near the customer. The efficiency of picking robots can improve operational efficiency, reduce upfront costs, and improve the safety of the workers by delegating them critical tasks such as carrying heavy crates and working closely with equipment such as forklifts.
Easy Deployment and Utilization of Existing Spaces: More products can be kept in a given space since an MFC uses space more efficiently than a traditional warehouse. This presents an opportunity for retailers, who may begin selling more goods online without requiring additional premises.
Enhanced Client Services: By using micro fulfilment center, businesses may enhance the customer experience through expedited deliveries. Additionally, faster refunds, returns, and exchanges are made possible by the thoughtful positioning of fulfilment facilities, which raises customer satisfaction.
Wrapping Up
By addressing several challenges such as order picking time, reducing operational costs, fluctuating demand, and infrastructural investment risks, Micro fulfilment centers offer robust solutions.
Automation solutions offered at Addverb Technologies, help to enhance storage optimisation, reduce manual errors, and improve operational efficiency, which significantly enhances customer satisfaction.
According to the most recent research conducted by Interact Analysis, it is forecasted that by the end of 2030, there will be nearly 7,300 automated micro fulfillment centers (MFCs) in operation, a significant increase from the mere 86 that were operational by the end of 2021. |
Adopting MFCs and state-of-the-art automation is essential for stores hoping to stay ahead of the competition in the industry. These technologies guarantee flexibility, scalability, and top-notch client service in addition to streamlining fulfilment procedures.
Get in touch with Addverb Technologies today to find out how their picking robots and automated warehouse solutions may transform your retail business and satisfy the expectations of e-commerce in the future.
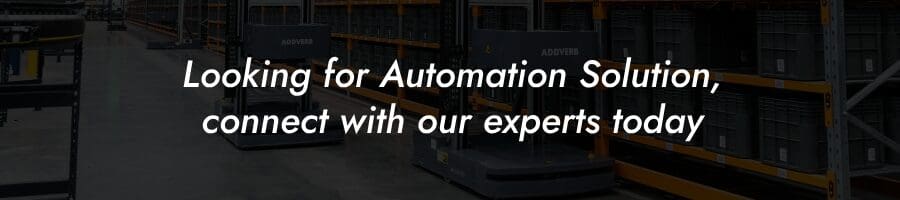
FAQ
- What is a Micro Fulfilment Center (MFC)?
A Micro fulfillment center is a small, highly automated warehouse located close to the end consumer, designed to speed up order fulfillment and delivery times.
2. How do Micro Fulfilment Center differ from traditional fulfillment centers?
Unlike traditional fulfillment centers, which are large and often located on the outskirts of urban areas, micro fulfilment centers are smaller and situated within cities or close to consumer hubs. This proximity reduces delivery times and costs.
3. What are the main benefits of Micro Fulfilment Center for retailers?
Micro Fulfilment Center offers several benefits, including faster delivery times, reduced shipping costs, improved inventory management, and the ability to meet increasing consumer demands for quick and efficient service.
4. How do Micro Fulfilment Center improve customer satisfaction?
By enabling quicker delivery times and ensuring a wider range of products are available for rapid dispatch, MFCs help meet customer expectations for fast and reliable service, enhancing overall satisfaction.
5. Are MFCs suitable for all types of retailers?
Micro Fulfilment Centers are particularly beneficial for retailers with high online order volumes and those offering same-day or next-day delivery. They are especially popular among grocery retailers and e-commerce companies.
6. How do Micro Fulfilment Center impact the future of retail?
MFCs are transforming retail by enabling faster, more efficient fulfillment processes, supporting the growth of e-commerce, and helping retailers meet the rising demand for quick delivery. They represent a shift towards more localized, technology-driven retail operations.
7. What are the challenges associated with implementing Micro Fulfilment Center?
Challenges include the initial investment in automation technology, integration with existing systems, and the need for skilled personnel to manage and maintain these advanced facilities.
8. Can small businesses benefit from MFCs?
Yes, small businesses can benefit by partnering with third-party MFC providers to access the advantages of faster fulfillment and delivery without the high upfront costs of setting up their centers.
Founded in 2016, Addverb offers complete robotics solutions for warehouse and industrial automation, with a strong global presence through its subsidiaries worldwide. The company provides a range of in-house automation products, including Autonomous Mobile Robots, ASRS, and sorting technologies. It serves over 350+ clients, including well-known companies such as Coca-Cola, Amazon, and DHL.