Table of Contents
The adoption of global warehouse order picking tools is seeing an upward trend. Valued at USD 7.46 billion in 2022, it’s projected to nearly double to USD 15.60 billion by 2030. That’s a robust CAGR of 9.84% from 2023 to 2030!
In warehouse operations, efficient order picking is crucial for meeting customer demands and maintaining productivity. Among batch picking vs wave picking, these are two of the most common techniques. Understanding the nuances between these methods can help in selecting the most appropriate one for your warehouse setup. Let’s delve deeper into these methods, their differences, and the best scenarios for their application.
Batch Picking
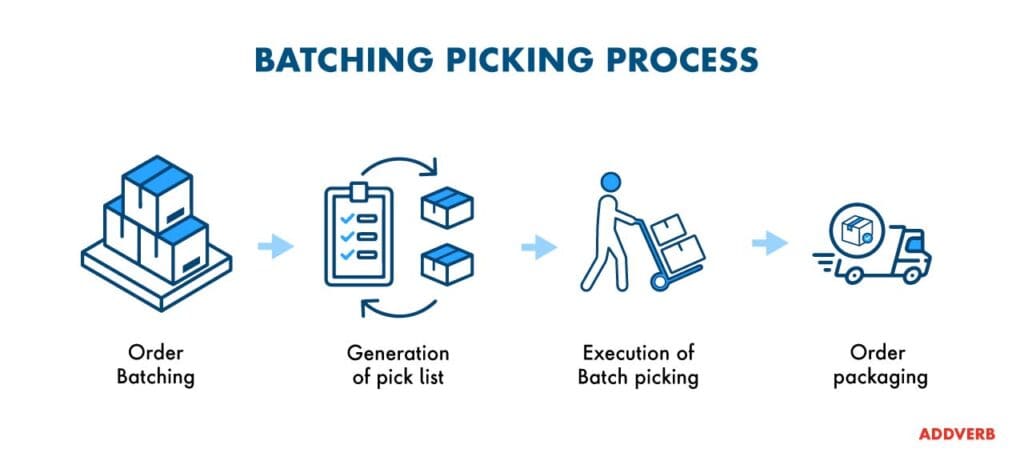
Batch picking is an order picking protocol where a picker compiles a batch of orders by picking multiple orders simultaneously, often from the same SKU. This method significantly speeds up the fulfilment process by reducing repeated trips to the same location. Each location is visited only once per batch, optimizing travel time, and reducing congestion in the warehouse.
Example of Batch Picking:
- Order 1: 3 soaps, 5 shampoos, 3 gels
- Order 2: 8 shampoos, 5 soaps
In batch picking, the picker combines these orders. When visiting the soaps section, they pick all 8 soaps; in the shampoo section, they pick all 13 shampoos, and then they collect the 3 gels. At the packing station, these items are sorted into individual orders. This method is ideal for orders with minimal SKUs, typically 4-5 SKUs per order, where each item is small enough to fit in a picking cart. It reduces travel time and warehouse traffic, making it suitable for smaller warehouses or areas with high SKU concentration.
Batch picking often involves the use of picking carts to deliver items to packing stations, unlike wave picking which may utilize conveyors or tilt-tray sorters. Warehouses can create uniform batches (e.g., 50 orders per batch with an average of 3 SKUs per order) or variable-sized batches based on order volume and SKU characteristics. Optimized paths for SKU picking can be suggested by Warehouse Management Systems (WMS) or Warehouse Control Systems (WCS), enhancing efficiency and reducing labour requirements.
Wave Picking
Wave picking involves grouping orders into waves, which can vary in size from a few orders to hundreds. In this method, a picker selects one order and one SKU at a time. Orders are grouped based on inventory characteristics, shipping routes, delivery schedules, shipping carriers, or packaging types. After picking, items are brought to a staging area for sortation into individual orders.
ALOS READ: A Comprehensive Guide to Understand Wave Picking Strategies and Techniques
Example of Wave Picking:
Consider a warehouse with 50 orders to be fulfilled within a shift:
- 20 orders require items from the cold storage area.
- 10 orders are destined for a specific location.
- 20 orders need to be packed in glass packaging.
These orders are divided into three waves, scheduled at different times for different zones. Once items in a wave are picked, they are taken to the sorting area and packed. Depending on the strategy, orders can be sent for packing immediately (fixed wave picking) or wait until all items for the orders are picked (dynamic wave picking).
Batch Picking vs. Wave Picking
The primary distinction between batch picking vs wave picking lies in their operation:
- Batch Picking: Involves one picking session per shift, with pickers visiting each location once per batch, greatly reducing travel time and congestion. It’s suitable for small warehouses or scenarios with minimal SKUs.
- Wave Picking: Can include multiple waves per shift, offering flexibility in planning and coordinating other warehouse activities such as replenishment and dispatch. It’s more effective in large warehouses with diverse SKUs, where logical order flows are necessary to maintain efficiency.
Choosing the Right Method
Both methods have their advantages:
- Batch Picking: Best for small warehouses, fewer SKUs, and small items. It enhances picking rate by minimizing travel time and congestion.
- Wave Picking: Ideal for larger warehouses with diverse SKUs, requiring automation tools like sorters, conveyors, and WMS to achieve optimal results. It allows for more controlled and flexible order fulfilment.
Ultimately, the choice between batch picking vs wave picking depends on the nature of your inventory, order profiles, and key performance indicators (KPIs). Both (batch picking vs wave picking) methods can significantly boost picking productivity and efficiency when applied correctly.
By understanding these methods’ distinct characteristics and advantages, warehouse managers can make informed decisions to optimize their order-picking processes, ensuring smoother operations and improved customer satisfaction.
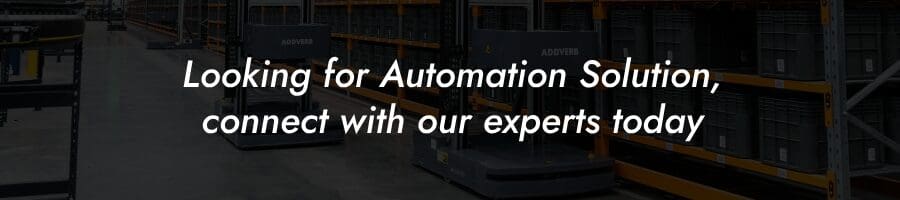
FAQ
What is batch picking?
Batch picking involves collecting items for multiple orders in one trip, reducing travel time and warehouse congestion.
What is wave picking?
Wave picking groups orders into waves, focusing on specific items, allowing for coordinated and flexible order fulfillment.
Batch Picking vs Wave picking
Batch picking reduces travel by handling multiple orders simultaneously, while wave picking organizes picking in waves for better coordination.
Can they be combined?
Yes, combining both can optimize efficiency based on warehouse needs.
How does WMS help?
A WMS improves efficiency in both methods by optimizing picking paths and managing inventory.