Table of Contents
The evolving world of logistics and warehousing has made automation a critical factor in driving efficiency, productivity, and cost-effectiveness. As we step into 2025, the challenges and opportunities in warehouse management are significant to sustain a competitive edge.
Challenges of Warehouse Automation in 2025
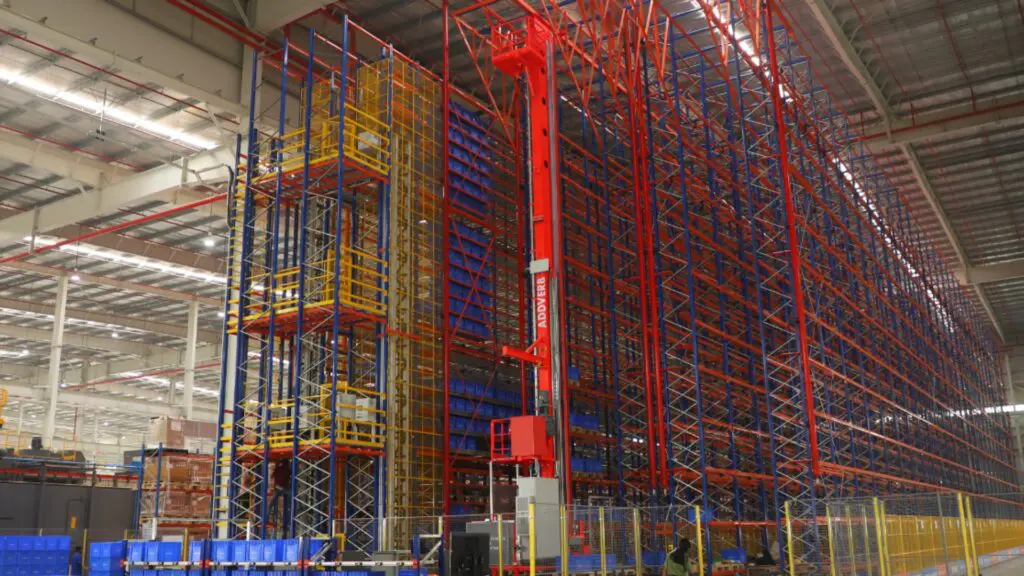
Warehouse automation in 2025 faces numerous challenges, including increasing customer expectations, labor shortages, and the need for faster order fulfilment. According to recent studies, the global warehouse automation market is expected to reach $30 billion by 2026. This growth is driven by the rising demand for automated storage and retrieval systems (ASRS), robotic picking and sorting solutions, and advanced intralogistics automation technologies.
Workforce Adaptation
- Challenge: There is a growing need for employees to adapt to new roles that require different skill sets, leading to potential resistance and a need for retraining programs.
- Reference: The integration of robotics in warehouses involves collaboration between machines and humans, necessitating retraining workers for new roles.
Space Constraints
- Challenge: Implementing automation often requires reconfiguring existing warehouse layouts, which can be challenging in facilities with limited space.
- Reference: Space scarcity continues to shape warehouse automation and intralogistics, driving the need for innovative solutions.
Choosing the right automation solution:
- Fixed automation is ideal for high-volume, repetitive tasks but lacks adaptability if demand patterns shift.
- Flexible automation (like AMRs) can scale up or down based on business needs but may require higher initial investment in software integration.
Addverb Technologies: A History of Innovation
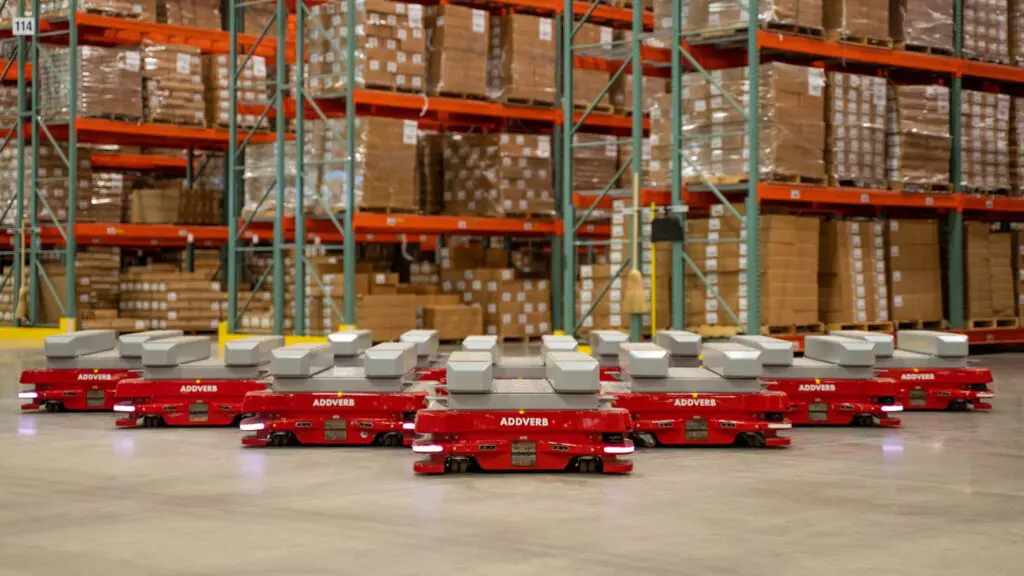
Addverb Technologies, founded in 2016, has quickly established itself as a global leader in warehouse automation. With a strong focus on research and development, Addverb has consistently delivered cutting-edge solutions that address the unique challenges faced by modern warehouses. From its state-of-the-art ASRS to its advanced sorting and intralogistics automation systems, Addverb has revolutionized the way warehouse automation in 2025.
Addverb’s Growth as a Market Leader
Over the years, Addverb Technologies has experienced remarkable growth, expanding its presence across multiple continents. The company’s success can be attributed to its customer-centric approach, innovative product portfolio, and dedication to delivering exceptional results. Addverb’s solutions have been implemented by numerous industry giants, testifying to their reliability and effectiveness in streamlining warehouse operations.
Why Choose Addverb for Your Warehouse Automation in 2025?
When it comes to warehouse automation in 2025, Addverb Technologies stands out from the competition for several reasons:
Easy to Manage Solutions: Easy to manage solutions: The new AGV control AI assistant from Addverb combines the power of AGV maintenance with generative AI and speech-to-text. This translation capability allows the operator to speak in any one of 98 languages and translate those words into commands, hence being understood by the AGV.
Customization and Scalability: Our solutions are highly customizable and scalable, ranging from tabletop sortation to 9km conveyor systems, ensuring they adapt to your warehouse’s unique requirements and scale with your business.
Comprehensive Solutions: Addverb offers a wide range of automation solutions, including ASRS, picking and sorting systems, and intralogistics automation, catering to the diverse needs of warehouse automation in 2025 across industries.
Proven Expertise: With a team of experienced professionals and a track record of successful implementations, Addverb has the expertise to deliver optimal results for your warehouse automation in 2025.
Successful KPIs
Material Movement: Maersk now dispatches 100,000 pieces daily to 2,500 unique distribution nodes, ensuring faster and more efficient deliveries.
Sortation: Mondial Relay achieved 100% sorting accuracy, reaching 80% of the targeted throughput within the first week of implementation.
Storage: Reliance expanded its storage capacity to 15 million units, seamlessly accommodating growing inventory demands.
Picking: Volvo boosted its hourly pick rate to 414 lines per hour, leading to a 60% increase in auto parts delivery efficiency.
Product Portfolio
Fixed Automation
Fixed Automation products consist of systems that rely on a fixed infrastructure for operation. These solutions are ideal for industries that demand high-volume, repetitive production of standardised products, such as automotive, electronics, food and beverage, pharmaceuticals, and packaging.
AS/RS: Innovative warehouse automation technologies designed for high-density storage and retrieval of goods. They are equipped with rails, robotic arms, shuttles, lifts, and software for inventory management and quicker material handling processes.
▪ Carton Shuttle ▪ Pallet Shuttle ▪ Mother Child Shuttle ▪ Multi-Level Shuttle ▪ 4-Way Pallet Shuttle
Stacker Crane: Efficiently loads and unloads heavy items, ensuring precise storage. It’s highly designed for unit loads and pallet loads, with accurate real-time inventory tracking.
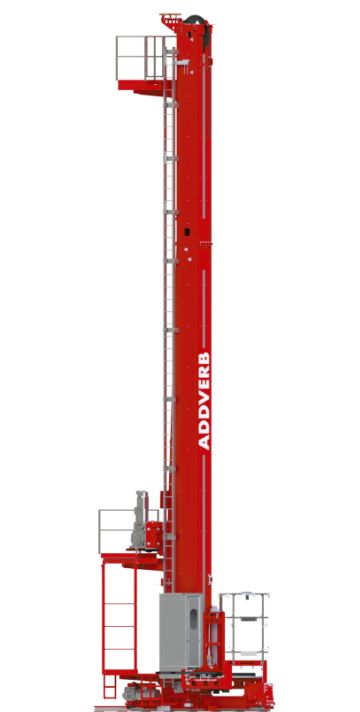
Vertical Sortation Robot: Delivers highly accurate sortation while sorting individual packets to their destination locations at varied heights on a dedicated track.
Rail Guided Vehicle: Provides a fast and flexible alternative to continuous conveyor systems used to transport pallets within warehouses and factories.
Flexible Automation
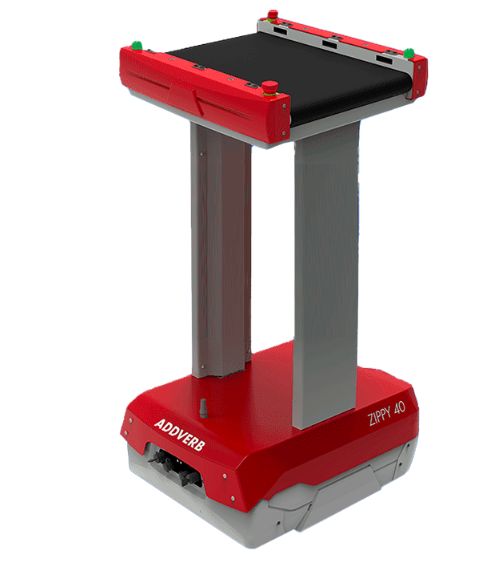
Fixed Automation products consist of systems that rely on a fixed infrastructure for operation. These solutions are ideal for industries that demand high-volume, repetitive production of standardized products, such as automotive, electronics, food and beverage, pharmaceuticals, and packaging.
Autonomous Mobile Robot: Powered by Lidar and operates on natural navigation. It can carry payloads of 100 kg, 200 kg, 500 kg, 1000 kg, 1500 kg, and 2500 kg.
Multi-Carton Picking Robot: Navigates through grid-based paths to pre-decided locations for storing and picking carton loads, working in perfect sync with one another.
Sorting Robots: Automated systems to identify and categorize order parcels or packages. They are equipped with sensors, cameras, and AI algorithms for accurate and quick sortation.
Autonomous Forklift: Autonomous forklifts are self-operating vehicles equipped a with sensors and software that allow them to navigate and transport materials without manual intervention.
Collaborative Robot: Designed to work alongside humans in shared spaces to perform industrial operations.
Pick-To-Light: Our trusted Pick-to-Light solution, empowers your workforce to pick the correct products and quantities swiftly and accurately for order fulfilment.
Pick-By-Voice: Our advanced Pick-by-Voice technology, revolutionizes the order-picking process. By eliminating the need for paper or RF devices, Zesty streamlines operations through voice commands
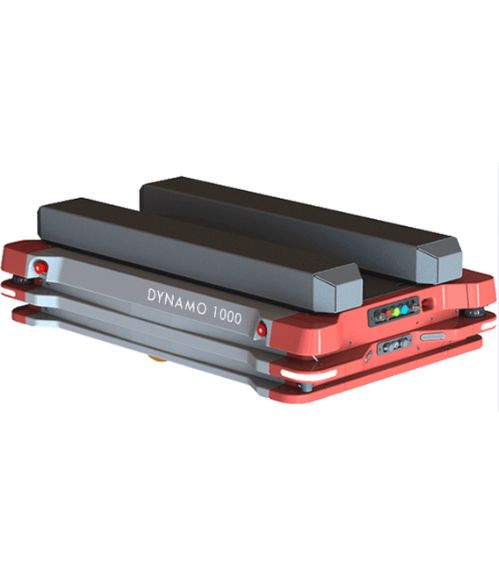
Conclusion
As warehousing automation in 2025 continues to evolve, automation has become a necessity for businesses looking to stay competitive. Addverb Technologies, with its innovative solutions, proven expertise, and commitment to customer success, is the ideal partner for your warehouse automation in 2025. By choosing Addverb, you can unlock the full potential of your warehouse, improve efficiency, and drive business growth. Don’t wait – take the first step towards a smarter, more automated warehouse today with Addverb Technologies.
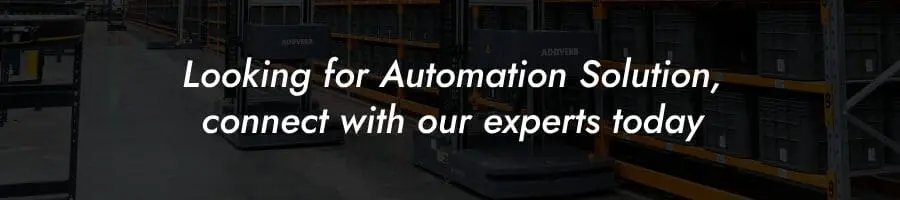