Table of Contents
In today’s evolving landscape, effective material handling drives operational excellence. Traditional methods often create inefficiencies, worker constraints, and increased safety risks, creating specific challenges.
Mobile robots have the potential to revolutionise material transport in a rigorous, much-needed transformation era. Imagine having an intelligent fleet of machines that will precisely navigate your facility, optimise workflows, and free up your workforce to focus on strategic activities.
With technology advancing rapidly, adopting innovative material handling solutions is no longer optional—it’s essential to stay ahead in the game.
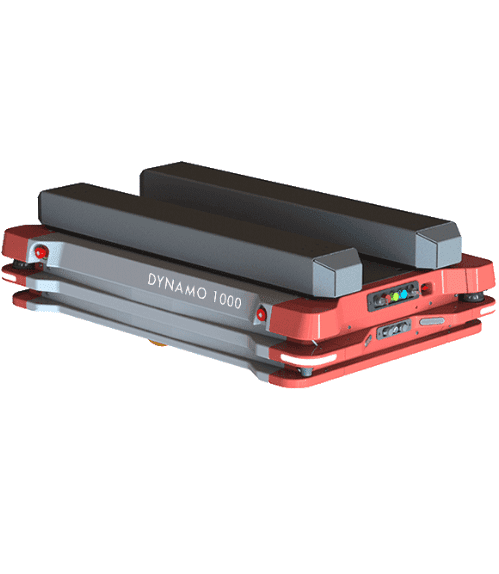
Importance of Efficiency and Safety in Warehousing
Efficiency and safety are two major factors to be considered in the busy warehouse environment. In the case of AMRs, the working operation efficiency is increased; the workplace is also made safe as concerns many aspects mentioned below:
- Minimised human error: Automation of repetitive jobs by AMRs minimises the human error that occurs, which in turn results in accurate order fulfillment and safer material handling.
- Improved ergonomics: AMRs take over the heavy task of lifting and transporting, mainly reducing the physical burden on the employees and the chances of injuries related to manual handling.
- Enhanced traffic management: It comes through intelligent navigation systems, which optimise routes and avoid collisions, hence promoting a safer working space for all employees while reducing the chances of accidents.
What is a Robotic Pallet Mover?
Addverb’s Dynamo is a powerful robotic pallet mover that helps in material movement. Equipped with natural navigation technology, you can easily transfer materials weighing up to 2500 kg throughout your operation.
Key Features of Dynamo
- Payload: Dynamo can carry loads up to 2500 kg.
- Charging Time: Just 8 minutes for quick charging for smooth operations and reduced downtime.
- Max Speed: The speed of the Dynamo is 2 m/s. It accelerates the material handling process, hence producing a much more efficient overall result.
- Run Time: The work time of the Dynamo is up to 4 hours on a single charge.
Benefits of Pick-Assistant Technology
Robotic pallet mover’s pick-assistant technology significantly increases operational efficiency in such a way that-
- Reduces Labour Costs: Almost all labour for redundant work is minimised.
- Enhanced Material Transportation: Dynamo redefines how materials can be moved about a warehouse. Automated pick, tugs, and transport eliminate bottlenecks and streamline workflows.
- Increased accuracy: Reducing mistakes in picking and delivery.
- Increasing Flexibility: Ability to adapt to every aspect of material handling needs of different industries.
How Dynamo Works
Using advanced natural navigation, the Robotic pallet mover maps its environment, avoids obstacles, and selects optimal routes to transport materials safely and efficiently. It can be smart about mapping its way out around sensors and complex algorithms, hence avoiding obstacles and taking optimal routes toward material handling. This way, it successfully operates safely and effectively within dynamic environments.
Robotic Pallet Mover for material movement, picking, or tugging is multi-versatile for use in any industry with varied needs. With its flexibility in AMRs, it forms an asset that any warehouse needs to possess to upgrade its productivity and ensure safe operations. With Dynamo by your side, you’ll be able to change your processes to beat the market.
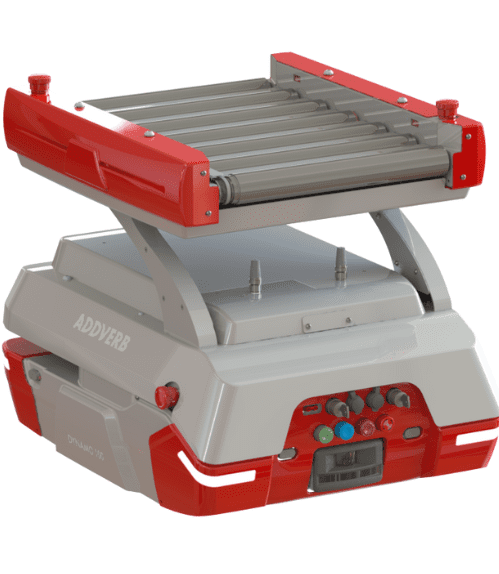
What is a Multi-Carton Picking Robot?
Veloce is a state-of-the-art fleet of autonomous vehicles, designed to revolutionise the movement and handling of goods within a warehouse. Navigation with grid-based paths, Veloce will allow for hassle-free operations for your business while perfectly working in sync to meet your needs.
Key Features of Veloce
- Payload Capacity: Every Veloce unit can carry up to 240 kg of payload, hence suitable for conveying heavy cartons and totes.
- Maximum Speed: Veloce can attain a maximum speed of 1.5 m/s to ensure on-time deliveries along with safety.
- Rapid Charging: Veloce can be charged in as little time as 15 minutes, which reduces idle time to the fullest extent.
- Longer Running Time: Veloce boasts a long running time of up to 3 hours; that means this truck can do a lot of work in a relatively short period and then come back for recharging before the next runtime.
Streamlining Material movement with Veloce
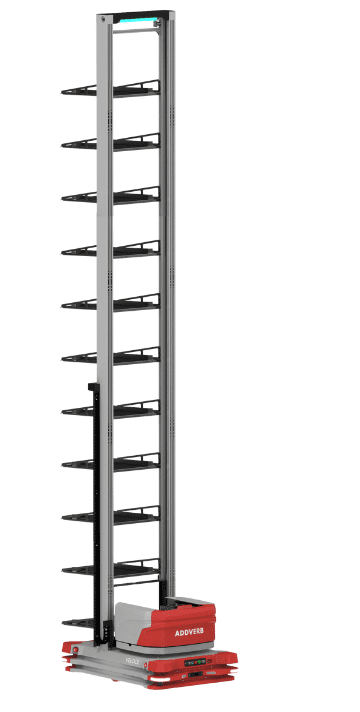
- Less Handling of Goods with Veloce: Multi Carton Picking robot increases material handling in your facility since it streamlines goods transportation within designated storage locations and picking areas. This will involve much less handling compared to how it would be in traditional transportation methods, ensuring that your operations become more efficient.
- Order Fills: You will be saving your orders so much time processing with Veloce incorporated into your operations. The automatic cars quickly move items to their picking stations so that the order process is completed in the shortest time possible and with maximum accuracy.
- Processing Cycle Savings Time in Picking Process: Veloce enables Goods-to-Person picking. This reduces instances of traveling long distances to fetch items. Though it reduces the time it takes to execute picking, this system ensures that employees are productive and happy while working.
- Controlled Storage and Returns Process: This way, Veloce works towards ensuring storage and return handling at one time. The automatic transportation of cargo to and from the storage location, means that one has a structured inventory, which is therefore easily accessed for maximum efficiency at the operations levels.
- Handling Returns: There will be no issues related to returns with Veloce. Returns can be transported to the precise areas very fast, hence keeping your inventory updated and managed very efficiently.
Case Study: Maersk Implements Flexible Warehousing
Due to the rapid scaling up of their brand and the rising demand, they urgently needed to incorporate a greenfield solution in a brownfield. To achieve all its objectives as an omnichannel fulfilment warehouse, Addverb designed an innovative solution that combines the power of both fixed and flexible warehousing.
The solution comprised autonomous mobile robots for material movement in the warehouse, Automated Storage and Retrieval Systems like Pallet Shuttles and Carton Shuttles to optimise space utilisation.
Final Thoughts
Automated mobile Robots like Dynamo and Veloce transform material transportation by streamlining operations, cutting labor costs, and minimizing errors. They create safer, more productive workplaces while ensuring seamless material handling.
Ready to modernise your warehouse operations? Let Addverb Technologies provide the solutions you need to optimize your logistics processes and drive your business forward.
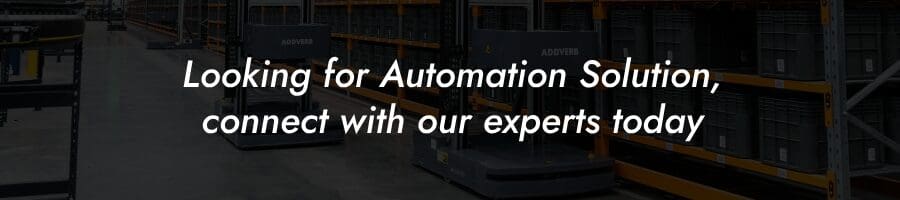
FAQ
What are autonomous mobile robots (AMRs) in material handling?
AMRs are intelligent machines designed to navigate facilities autonomously, optimising workflows and transporting materials efficiently within warehouses and industrial environments.
How do AMRs enhance efficiency and safety in warehousing?
AMRs improve efficiency by automating repetitive tasks, reducing human errors, and optimising traffic management. They enhance safety by minimising physical strain on workers and decreasing the risk of injuries related to manual material handling.
What is Addverb’s Robotic pallet mover(RPM), and what are its key features?
Dynamo, Addverb’s advanced robotic pallet mover, is designed to optimise material transport with key features such as a high payload capacity, cutting-edge navigation technology, and robust safety mechanisms.
How does Addverb’s Multi-carton picking robot(MCPRS) streamline material handling?
Veloce, a multi-carton picking robot, streamlines material handling by:
- Efficiently handling multiple cartons simultaneously.
- Navigating autonomously to optimise picking routes.
- Integrating seamlessly with existing warehouse management systems.