Table of Contents
In the race toward faster, smarter, and more cost-effective fulfillment, businesses often find themselves performing warehouse optimization in what they can see—the picking path, the AMR task time, resource allocation. While these local wins play an important role, the real transformation comes when warehouses zoom out to the bigger picture.
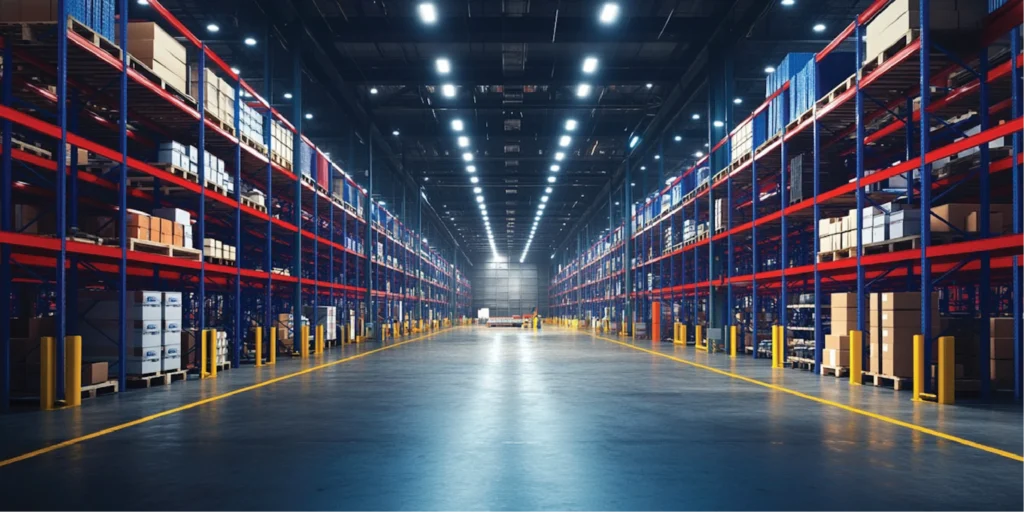
Think of it like…
Correctly tuning a single violin in an orchestra will make that violin sound beautiful. But the music won’t come together, without tuning the entire ensemble – That’s how local and global warehouse optimization are different. Let’s break down why warehousing needs a bird’s-eye view—and why aligning local improvements with global goals is the key to scalable efficiency.
Addverb’s whitepaper on “Metrics That matter” gives a great insight into this.
What is Local Optimization?
Warehouse optimization in local sense focuses on enhancing individual processes or zones, like faster picking routes, smarter AMR paths, or reduced tote dwell time.
Examples
- Redesigning packing stations to reduce labor fatigue.
- Implementing zone-based picking to reduce travel time.
- Adjusting storage layouts for fast-moving SKUs.
- Optimizing conveyor speed or robot routing in high-traffic areas.
These tweaks deliver quick and ‘local’ wins, in that particular process. But without integration into a broader system, they can sometimes create bottlenecks, silos – or even worse, a false impression of achieving overall efficiency.
The Illusion of Local Success
A warehouse might report:
- +98% picking accuracy
- Very high throughput from conveyors
- Perfectly scheduled maintenance windows
But still the delays persist in order fulfillment. Why? Because ‘local’ success does not always translate to ‘global’ effectiveness.
A fast conveyor could overwhelm a docking process that is relatively slower. High AMR utilization might come at the cost of neglecting urgent tasks in other zones. A perfectly optimized storage system may cause delays if picking routes are not optimized concurrently. This is the fallacy of local optimization in isolation – it solves for the piece, not the puzzle.
What is Global Optimization?
Warehouse optimization in global sense means aligning all the warehouse processes, be it picking, sorting, storage, automation, labor, and fleet – toward the common business-level goals like:
Examples
- Faster order fulfillment
- Automation system’s throughput
- Inventory turnover
- Controlling opex / Cost per order
- Customer satisfaction
It ensures every local optimization adds up to a cohesive, real-time warehouse strategy.
An Analogy – Local vs. Global Optimization
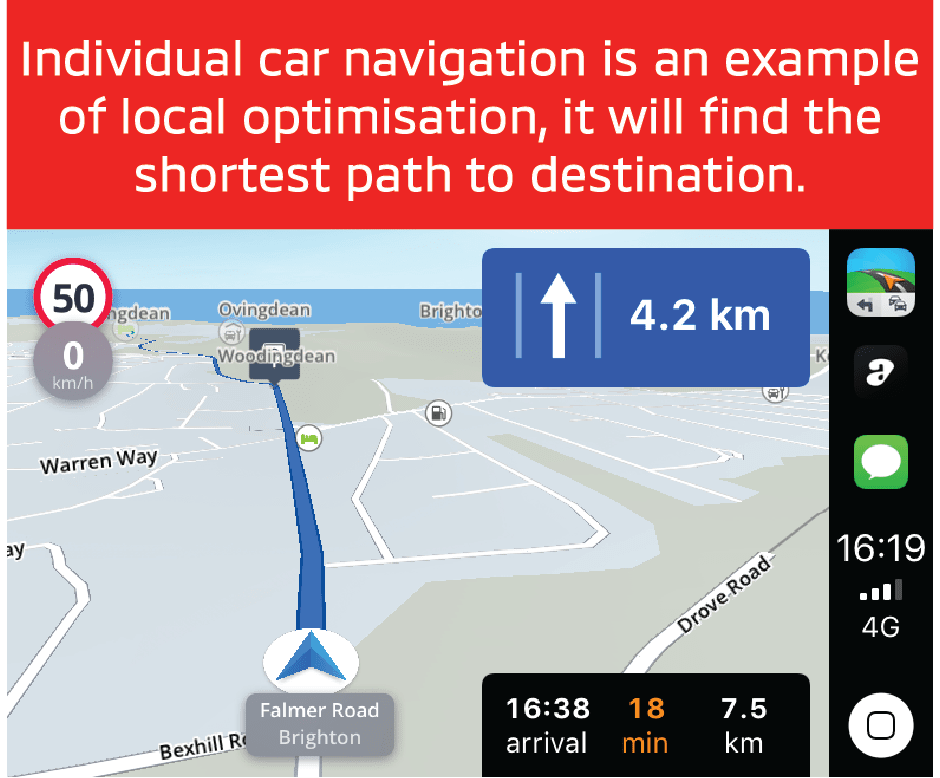
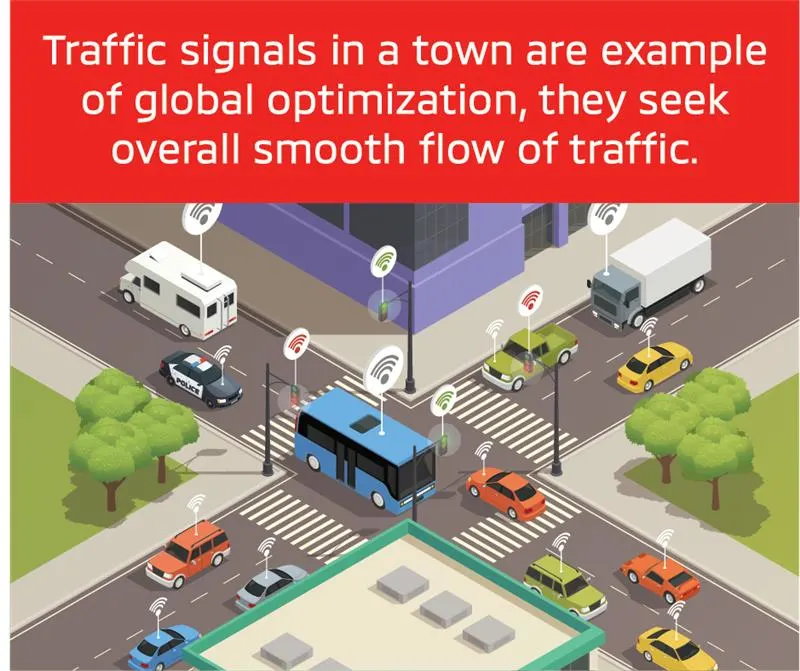
GPS guides you to take the best (fastest, least congested) route to your destination. This is local warehouse optimization.
A city planner adjusts the traffic lights across the city to ensure smoothness in everyone’s commute. This is global warehouse optimization. Warehouses need both. Without a city planner’s map, the GPS can lead you right into gridlock. Without the GPS, you’re moving like a ship without a rudder.
The Role of Warehouse Software in Bridging the Gap
Modern warehouses must deal with thousands of SKUs, multiple shipping formats, reverse logistics, and labor constraints. It’s impossible to keep every part of the system optimal manually.
That’s where intelligent warehouse software comes in.
A strong Warehouse Software Suite (like Addverb’s Optimus WMS, Concinity WES, or Movect FMS) enables:
- Seamless orchestration across AMRs, conveyors, picking stations, and storage
- Real-time data visibility for inventory, tasks, and system health
- AI-based task prioritization, ensuring robots and humans focus on what matters most
- Scalable architecture, ready for brownfield and greenfield sites alike
It’s like giving the conductor a smart baton – and letting every instrument follow the same rhythm.
Why a Bird’s-Eye View is Critical
According to McKinsey, end-to-end optimization in large fulfillment centers reduce order processing time by up to 40%.
Deloitte reports that 55% of warehouses struggle with disconnected local improvements that don’t support global outcomes.
Addverb’s holistic approach has helped clients like Volvo, PepsiCo and 350 others align micro-efficiencies with macro-performance goals:
- Improvements in throughout
- Faster order fulfillment
- Efficiency and productivity gains
- Optimized space utilization
Success Story from the Harmony of Global and Local Optimization
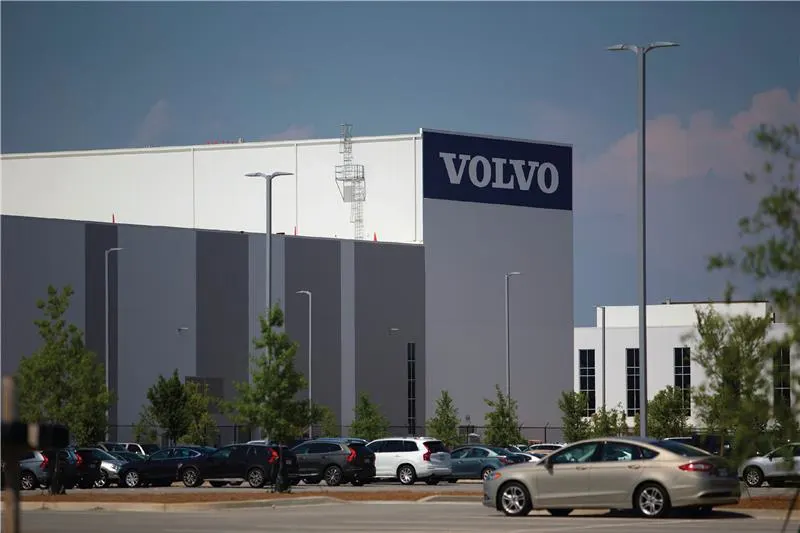
Addverb partnered with Volvo, who sought to improve the overall productivity and efficiency levels as they expand the VE Parts Distribution Center (VEPDC) for better traceability, accuracy, and order-to-delivery times and enhancing customer satisfaction.
The local warehouse optimization decisions included implementing
- 3 Crane ASRS with 5,700 pallet positions – supporting 15-21 days of inventory, and 60 picks/hour.
- Multi-Level Shuttle System with 23,040 tote positions and 100 buffer positions – managed six days of inventory.
- 4 Goods-to-Person (GTP) stations, handling 15 order totes at once.
The global warehouse optimization that brought it all together:
- An integrated conveyor system connecting the ‘local’ systems.
- Warehouse Execution System (WES) to optimize storage and synchronize the operations.
The result? 66% increase in daily order lines, from 6,000 to 10,000
Improved dispatch accuracy, reducing truck turnaround times, and boosting productivity.
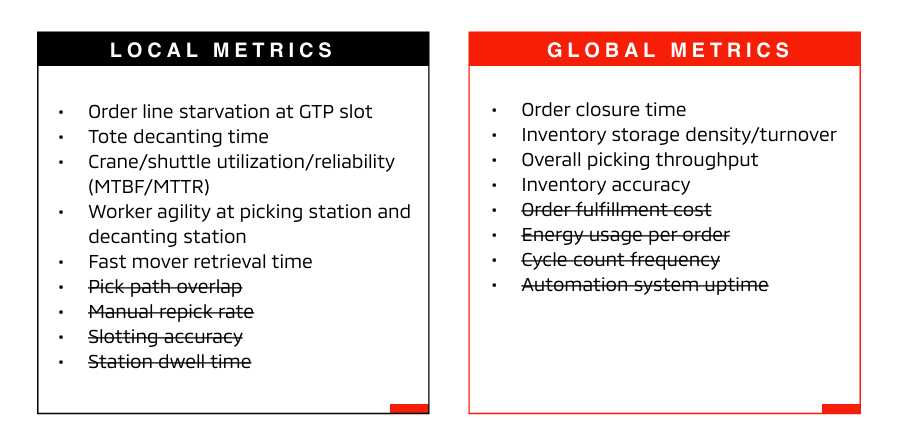
Conclusion
Think bigger than just a pick path.
Local warehouse optimization is important. But only when seen through a global lens can it truly drive warehouse excellence.
Modern warehousing isn’t just about moving faster – it’s about moving smarter, in sync, and at scale. High time warehouse leaders stop thinking in silos and start thinking in systems.
The takeaway? Your next big warehouse win might not be in the pick path, it could be in seeing how every pick fits into the big picture.
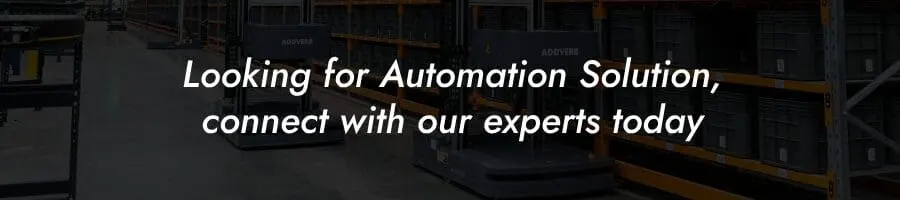