Table of Contents
We often get asked: how much will a warehouse management system cost?
Several factors play a pivotal role in determining warehouse management system cost. As there is a multitude of factors which are crucial for your warehouse operations inventory management, here we present a step-by-step guide to consider which features to consider while prioritising or choosing a Warehouse Management System software:
- Begin by assessing your business requirements and the key functionalities necessary for smooth operations. These functionalities encompass order management, inventory monitoring, and pick-and-pack capabilities.
- Next, pinpoint areas within your warehouse operations that could benefit from enhancements, like optimising manual procedures or minimising inventory discrepancies.
- By leveraging advanced functionalities, you can enhance efficiency in truck routing or managing kitting and packaging for prospective customers.
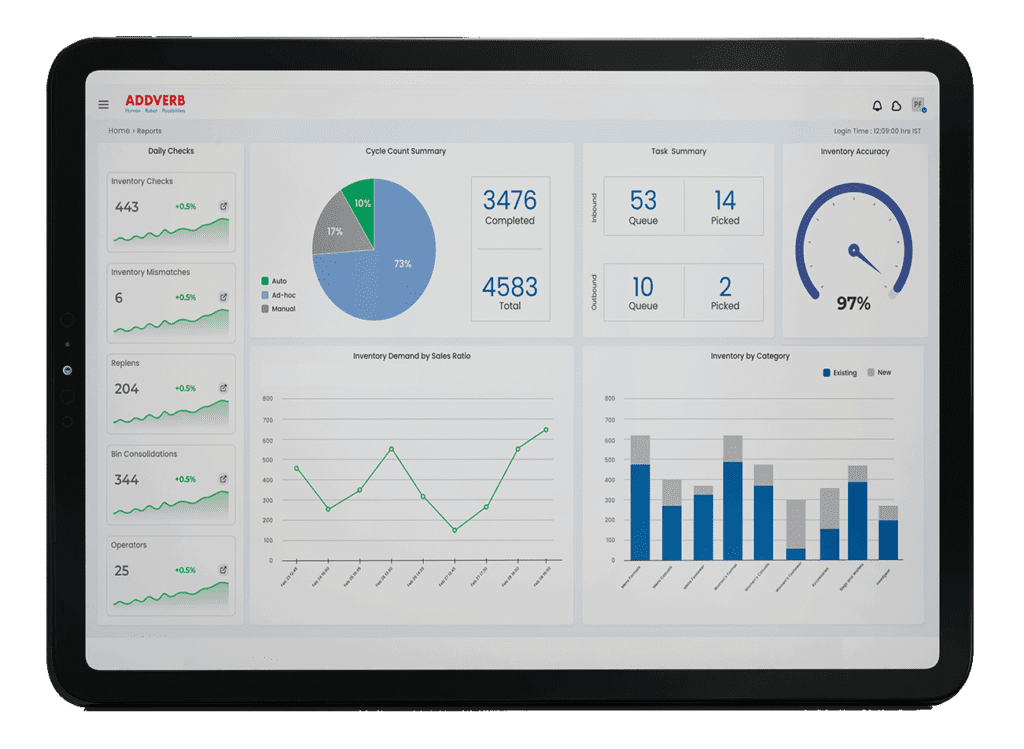
What Factors Influence the Cost of a Warehouse Management System?
In India, Warehouse Management System (WMS) prices depend on the size of the warehouse, complexity of warehouse operations, and required features. Usually, pricing for a basic WMS solution that is suitable for small to mid-sized warehouses is affordable.
While larger systems which have more advanced capabilities and integrate with other enterprise systems tend to be higher priced. Installing, customising, training, and ongoing support can all affect overall costs based on the requirements, configuration, and scale of the solution.
1. System Features and Functionalities
It is pivotal to be aware of installation and customization pricing models when budgeting for your warehouse management system.
Installation costs
- On-premise solutions: These are the costs involved in hardware, software, physical licences, and physical equipment. Software packages that heavily rely upon perpetual licences have higher upfront costs due to purchasing them upright for business needs. Running a database, implementing configuration, and integration may incur additional fees.
- Cloud-based solutions: These costs are required on-site with subscription pricing models. On-premise, permanent licence. WMS packages typically have a separate annual maintenance expense as part of your contract. This includes updates, upgrades, security fixes, and technical support for your program.
Customized costs
Higher costs are incurred due to the tailored functionalities required for the business.
- Training expenses: Training the staff can add to the extra cost to keep them updated; depending on your vendor, they may have a training center for your team to visit, send experts to your location to train teams on your specific equipment, or provide self-study information such as webinars and system documentation. Self-study features are now more than just bare-bones assistance; some providers may generate particular documentation and training content depending on your business, equipment, and operations.
2. Size and Complexity of the Warehouse
When considering the factors influencing the cost of a warehouse management system, these factors come into play:
- Small warehouses typically demand simpler WMS solutions with limited functionality. Fewer users, simpler inventory management requirements, and less extensive hardware requirements reduce costs.
- More giant warehouses require more sophisticated WMS solutions with additional functionality to manage massive inventory quantities, many locations, and complex workflows. This dramatically raises expenses due to more complicated software and hardware infrastructure requirements.
- The complexity of the operations: Warehouses with single-location storage and packing processes use standard WMS with minimal customization. On the other hand, warehouses with significant operations, including multi-location management, supply chain integration, and advanced order processing, require a higher WMS package with scalable solutions.
3. How Much Data to Be Used
The quantity of data handled by the WMS substantially impacts expenses. Extensive datasets necessitate more resilient storage options and enhanced processing capabilities, resulting in elevated costs.
- Data Analysis: Including advanced data analysis functionalities, which extract valuable information from extensive datasets, leads to increased expenses due to sophisticated software requirements and potentially higher subscription fees.
4. Integration of other WMS Features
Integrating the WMS with other enterprise systems like CRM, ERP, and SCM can increase costs due to the seamless features included in the package model. Additional features include automated picking, real-time inventory tracking, and barcode scanning upgrades when SaaS models are being upgraded.
When opting for on-premise solutions, upgrades may be necessary for the database servers, networking hardware, and PCs used for your WMS. When investing in a new warehouse management system, anticipate increased equipment demands.
5. Improving Infrastructure
Upgrading storage solutions, such as incorporating vertical storage and improving warehouse layouts, allows the WMS to manage space more effectively and improve inventory accessibility.
Improved data storage and processing capacities ensure that the WMS can efficiently manage large amounts of data while providing critical insights for strategic decision-making. Companies can optimise their WMS capabilities by improving infrastructure, increasing operational efficiency, adaptability, and response to market requirements.
Cost savings of implementing a Warehouse Management System (WMS)
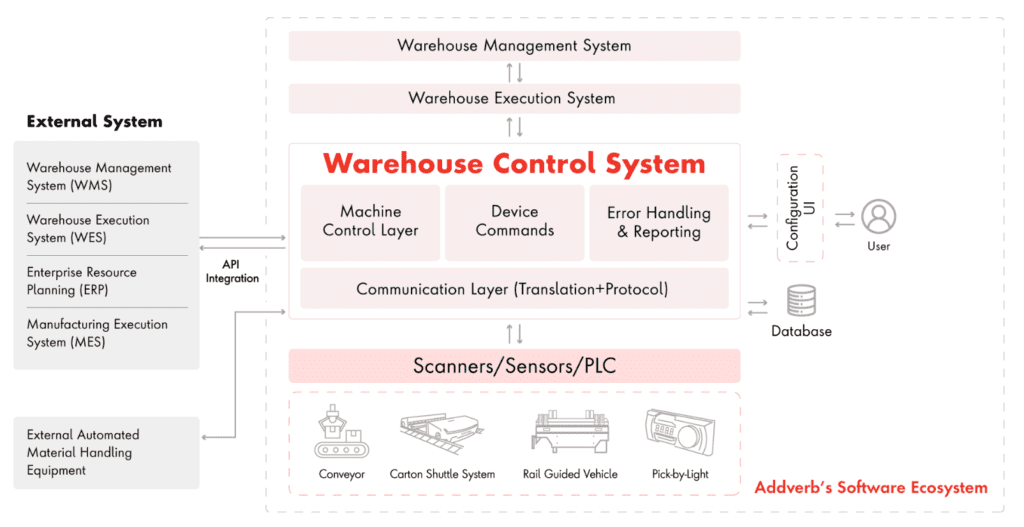
Investing in a warehouse management system can lead to substantial cost savings, improved operational efficiency, and more considerable scalability than relying on manual systems, which cause human errors or other drawbacks of improper inventory records.
- Lower Labour Costs: By automating warehouse processes, less manual labour is required, which saves money on wages and lowers the risk of human error.
- Enhanced Productivity: Real-time inventory tracking and streamlined procedures increase efficiency and decrease the time and resources required to oversee warehouse operations.
- Lower Inventory Holding Costs: Overstock and stockouts are minimised through improved inventory management, which maximises storage capacity and lowers holding expenses.
- Increased Accuracy: Order accuracy is increased by automated processes, which lowers the costs related to returns, reshipments, and unhappy consumers.
Discover more insightful content on our blog! |
Keep Costs Low with Addverb’s Warehouse Management System
We tailor pricing based on each client’s unique needs and operational complexity. Addverb’s Optimus is a highly customizable WMS that utilizes advanced techniques to boost warehouse operational efficiency.
Optimus guarantees smooth operations and increased productivity by optimising resource allocation and material movements. It efficiently manages inbound and outbound logistics, facilitating a seamless flow of goods within the warehouse.
With its robust inventory control features, Optimus offers precise and up-to-date visibility into stock levels, reducing instances of stockouts and overstocks.
The system effectively handles resources and distributes workloads to enhance productivity. Additionally, Optimus is crafted for easy reconfiguration to cater to specific site needs, ensuring flexibility and scalability.
Conclusion
We hope the above-listed pointers gave you valuable insights into the cost of a warehouse management system. To maximise warehouse management, head to Addverb Technologies, a software application that optimises warehouse operations, including inventory and labour management.
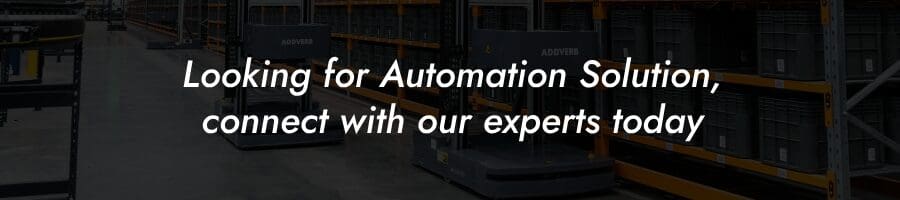
How much does it cost to automate a warehouse?
The cost of warehouse automation is dependent upon your particular situation. The critical factors will be facility size, complexity of operations, levels of automation desired and the existing infrastructure.
Implementation costs will depend on whether partial or full automation is to be achieved. The variety of equipment-from simple conveyor systems to advanced robotic solutions AI-surely affects the capital investment needs. For a proper budgeting assessment, it’s always best to consult with automation specialists for an exact and tailored assessment.
What is a Warehouse Management System (WMS)?
A Warehouse Management System (WMS) is a software solution designed to manage and optimize warehouse operations, including inventory management, order picking, shipping, and receiving.
What factors influence the cost of a WMS?
The cost of a WMS is influenced by several factors, including the size and complexity of your warehouse operations, the number of users, the type of WMS (cloud-based vs. on-premise), the level of customization and integration required, additional features and modules, and support and maintenance services.
How can I determine the ROI of a WMS?
To calculate the ROI of a WMS, consider factors like increased efficiency and productivity, reduced labor costs, improved inventory accuracy, enhanced customer satisfaction, and cost savings from reduced errors and returns.
Can I get a free trial or demo of a WMS?
Many WMS providers offer free trials or demos, allowing you to test the system’s features and determine if it meets your needs before making a financial commitment.
How do I choose the right WMS for my business?
When choosing a WMS, consider the specific needs and scale of your warehouse operations, the system’s scalability, integration capabilities with existing systems, user-friendliness, and the vendor’s reputation and customer support.
Founded in 2016, Addverb offers complete robotics solutions for warehouse and industrial automation, with a strong global presence through its subsidiaries worldwide. The company provides a range of in-house automation products, including Autonomous Mobile Robots, ASRS, and sorting technologies. It serves over 350+ clients, including well-known companies such as Coca-Cola, Amazon, and DHL.