Table of Contents
The trend of automation in industrial production has led to massive use of autonomous robots. In classical approaches, safety in robotic warehouses is usually guaranteed by isolating robots from humans. Collaborative robots, i.e., humans and robots working together, are expected to increase both productivity and performance.
As technology advances, so does our ability to revolutionise traditional practices. One such innovation that is rapidly transforming the industry is automated warehouses. These cutting-edge facilities are powered by state-of-the-art automation systems designed to improve efficiency and productivity. However, as with any revolutionary change, safety concerns arise. At Addverb, we understand the paramount importance of ensuring safety in robotic warehouse environments for both humans and machines in these high-tech robotic warehouses.
Ensuring Safety in Robotic Warehouses
We understand the importance of identifying potential risks and taking proactive measures to mitigate them. Our practices for conducting thorough risk assessments are designed to identify hazards, evaluate their severity, and implement effective control measures.
Risk Assessment Process
The first step in our risk assessment process involves identifying potential risks that could pose a threat to the safety in robotic warehouse and our employees. This includes assessing all aspects of the warehouse environment, such as layout, equipment, materials handling processes, and employee tasks.
We also consider both internal and external factors that could impact safety with automated warehouse robots. By thoroughly examining every aspect of our warehouse operations, we can ensure that no potential risks go unnoticed.
Once potential risks have been identified, we assess their severity based on several factors including likelihood of occurrence and consequences. We use a systematic approach to rank each risk level using a scale from low to high. This allows us to prioritise which risks need immediate attention and which ones can be addressed at a later stage.
After identifying potential risks and evaluating their severity levels, our team develops comprehensive strategies to address each risk effectively.
In-depth training for Employees
Our advanced technology and state-of-the-art warehouse solutions require a skilled workforce that is well-equipped to handle the complex automation solutions.
To begin with, all our employees undergo rigorous training sessions before they are assigned any responsibilities in the warehouse. This includes both theoretical as well as practical knowledge about the functioning of our robotic warehouses and systems. Our trainers have years of experience working with these cutting-edge technologies and are able to effectively impart their expertise to our employees.
The training program is designed to cover various aspects such as understanding the basics of robotics, learning how to operate different types of machines and equipment, handling emergency situations, and ensuring proper maintenance procedures. We also provide specialised training for specific roles such as operators, technicians, and managers so that they can perform their tasks efficiently while maintaining warehouse safety.
Installation of Safety Barriers
Safety barriers play a crucial role in preventing accidents and injuries in robotic warehouses. They act as physical barriers between humans and robots, creating a safe working environment where both can operate without risk of harm. Addverb recognises the importance of these barriers and has implemented various measures to ensure their effectiveness.
To begin with, Addverb conducts thorough risk assessments before setting up any new warehouse or implementing new mobile robotic systems. This involves analysing potential hazards that could arise from working with robots, such as collisions or entanglement, and identifying areas where safety barriers are required. These risk assessments not only help identify potential risks but also aid in determining the most suitable type of barrier for each specific area to ensure safety in robotic warehouses.
Regular Inspection and Maintenance
Addverb follows a strict protocol for regular inspection and maintenance to ensure the smooth functioning of their robotic warehouses
Conducting Daily Inspections
The first step in ensuring safety in robotic warehouses is conducting daily inspections. Addverb’s team of trained technicians conducts thorough inspections of all robots, machines, and equipment before starting operations each day. This includes checking for any damaged or malfunctioning parts, loose connections, or potential hazards that could pose a risk in safety in robotic warehouse.
Scheduled Maintenance
In addition to daily inspections, scheduled maintenance is also an essential practice followed by Addverb. The company has a well-defined schedule for routine maintenance tasks such as lubrication, cleaning, and calibration of robots and other equipment. This helps to identify any issues early on and prevent them from developing into more significant problems that could compromise safety in robotic warehouse.
Training Programs
Along with regular inspections and maintenance tasks done by trained technicians, Addverb also conducts training programs for warehouse staff on basic troubleshooting techniques for minor issues that may arise during operations. This empowers employees with the necessary knowledge to handle minor repairs or report any potential hazards.
Safety Sensors and Emergency Stop Buttons
Maximising robotic operation safety requires the installation of advanced safety sensors. These sensors come in various forms, including proximity sensors, vision systems, and laser scanners. They provide real-time data on human presence, objects, or potential hazards near robots.
When a human is in the robot’s way, the sensors immediately communicate with the robot’s control system, triggering safety measures such as reducing speed, pausing movements, or stopping the robot to prevent accidents.
To ensure worker safety in robotic warehouse and swift response during emergencies in warehouses, the installation of easily accessible emergency stop buttons is crucial. These buttons, also known as kill buttons, provide a reliable way to quickly halt robot operations in critical situations, preventing accidents and damage.
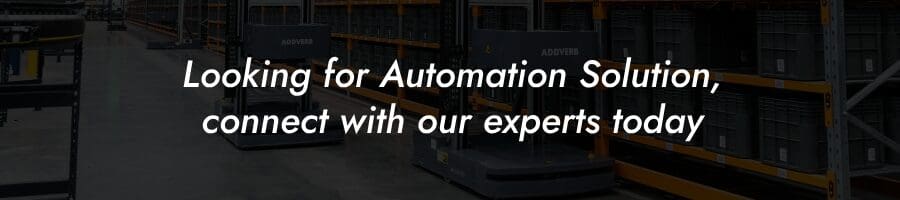
FAQ
How are risks mitigated in robotic warehouses?
Through comprehensive risk assessments and control measures.
How are employees trained for safety?
Employees receive training on robotic systems, safety protocols, and emergency procedures.
What safety features protect workers?
Safety barriers, sensors, and emergency stop buttons are installed.
How is maintenance managed for safety?
Regular inspections and maintenance are conducted to ensure safe operations.
What do safety sensors do?
They detect humans or obstacles, slowing or stopping operations if necessary.