Table of Contents
With e-commerce exploding and customer expectations reaching new heights, the pressure to deliver faster, cheaper, and more accurately is relentless. But here’s the catch, while demand keeps rising, space is shrinking, and labour is getting costlier. That’s not just a challenge; it’s a call for transformation.
Warehouses today aren’t just storage spaces, they’re the beating heart of a lightning-fast supply chain. Intelligent ASRS systems are changing the game, helping warehouses shift from reactive firefighting to proactive precision. From optimising vertical space to reducing human errors and improving inventory accuracy, ASRS systems isn’t just automation, it’s a strategic upgrade for the modern warehouse.
Automated Storage and Retrieval System
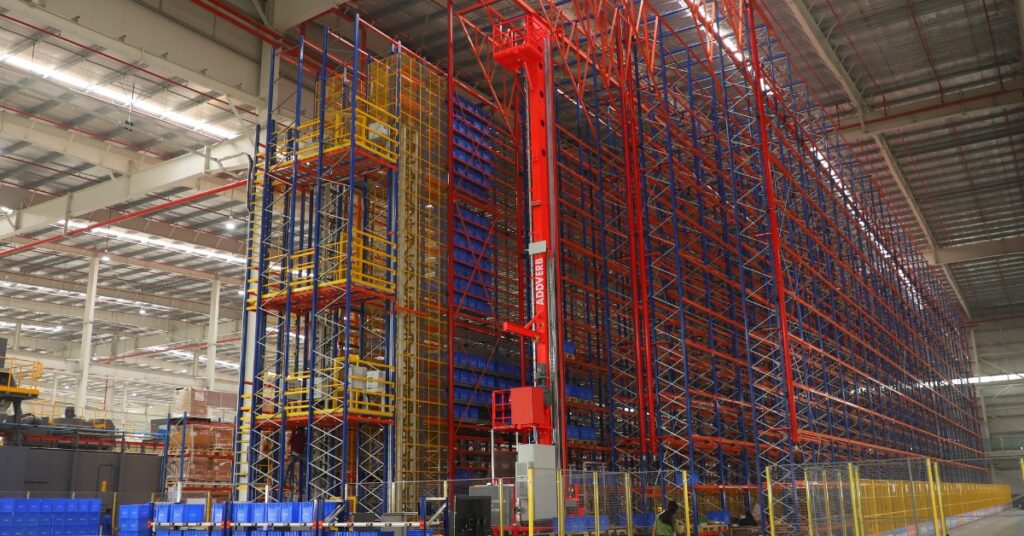
ASRS systems serves as an efficient, high-density solution for fast and accurate storage and retrieval, eliminating the need for additional personnel. This real-time inventory management system integrates cranes, shuttles, and lifts working in conjunction with Warehouse Management Systems (WMS) and Warehouse Execution Systems (WES). Modern warehouses require more than just automated labour replacements, redesign efforts must focus on improving operational speed and efficiency while incorporating intelligent systems.
Making Better Use of Space
Traditional warehouses often underutilize vertical space, leading to limited storage capacity and increased real estate expenses. Automated Storage and Retrieval Systems (ASRS) address this issue through tall, space-efficient designs that maximize ceiling height and minimize the need for wide aisles. By doing so, ASRS can reclaim up to 85% of floor space, making warehouse layouts significantly more efficient and cost-effective.
Improving Accuracy
Manual picking errors come can double the costs, they impact customer satisfaction and drain operational budgets. By integrating software within ASRS operations, warehouses can achieve significant gains in order accuracy while substantially reducing the financial burden of fulfilment errors.
Getting Real-Time Inventory Visibility
Manual inventory management can cause issues like overstocking and shortages. ASRS systems provides real-time stock monitoring that helps companies make better choices for restocking and estimating demand and improving warehouse layout efficiency.
Reducing Operating Costs
Labour shortages together with increased wages put strain on operational budgets. The resulting reduction labour expenses after implementing an ASRS system and optimized space results in long-term cost savings.
Speeding Up Fulfilment
Modern commercial operations depend on the exchange of speed as their primary form of asset. ASRS streamlines both picking operations and storage execution thus it decreases order delivery time without compromising quality performance.
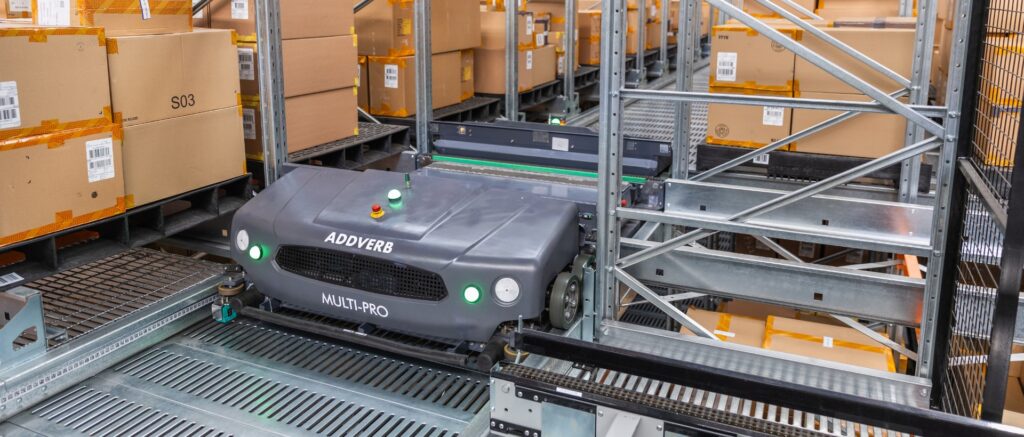
Handling Returns
More and more order returns can create business chaos. ASRS systems maintain efficient reverse logistics operations by keeping track of returned goods then storing and reprocessing them for further use.
PepsiCo – Automated Mixed Case Palletizing
PepsiCo planned to establish its 4th production plant in India, which would be its largest and fully automated captive warehouse. They wanted to shift from manual to automated processes to address their storage and throughput requirements. Addverb came up with a unique mixed-case palletizing solution that helped them make the most of their limited space.
Future
Businesses require new techniques because consumer expectations continue to change and supply chains become progressively complex. ASRS systems offers businesses future operational protection by unifying agile handling with precise management and extended capabilities within a single unified platform.
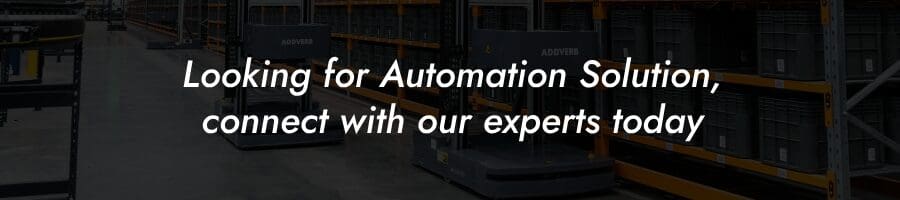
FAQ
What are the benefits of using an AS/RS?
- Increased efficiency: Faster retrieval and storage of items.
- Space optimization: Better use of vertical space.
- Labor reduction: Decreases the need for manual labor.
- Accuracy: Reduces human error in inventory management.
- Safety: Enhances workplace safety by minimizing manual handling.
How does an AS/RS work?
An AS/RS uses a combination of automated machinery and software. The system’s software manages inventory data and directs the automated machinery to store or retrieve items based on this information.
What industries benefit most from Automated Storage and Retrieval Systems?
- Manufacturing: For efficient parts storage and retrieval.
- Retail: For managing inventory in distribution centers.
- Pharmaceuticals: For precise storage and retrieval of medical supplies.
- Food and Beverage: For handling temperature-sensitive goods.
- E-commerce: For fast order fulfillment.
Can an AS/RS be customized?
Yes, AS/RS solutions can be tailored to meet specific business needs, including custom configurations for storage density, load handling, and integration with other automation systems.
Addverb, one of the leading robotics and automation companies for maintaining efficiency, reliability, and accuracy in your supply chain, offers the power-packed range of AS/RS that provides the efficiency and speed required for the supply chain management environment of today. Our solutions include a carton shuttle for streamlining order picking, a mother-child shuttle for multi-deep pallet storage requirements and a pallet shuttle that increases storage density multifold. Addverb’s ASRS system can be tailored to fit your specific load profile and weight, building capacity and operating surroundings. All solutions feature premium-quality drives for smooth, fast, and reliable performance.