Inhoudsopgave
Ongeveer 25% van de magazijnen in de hele wereld heeft in 2024 een vorm van automatisering ingevoerd. Slechts 10% maakt echter gebruik van geavanceerde operationele automatisering.
Lees de blog om een aantal belangrijke uitdagingen in halfgeleider warehousing te ontrafelen en hoe Addverb's revolutionaire technologieën helpen om deze op de meest effectieve en efficiënte manier te transformeren.
Belangrijkste uitdagingen bij het opslaan van halfgeleiders
Onnauwkeurig voorraadoverzicht: Dergelijke slechte tracking in real-time en kan leiden tot discrepanties in voorraden en per-order fulfilment fouten.
Temperatuurgevoelige opslag: Halfgeleiders zijn gevoelig voor beschadiging en hebben een delicate temperatuur nodig.
Korte houdbaarheid van producten & FIFO-beheer: Beheer van houdbaarheidsdatums en FIFO, de First In - First Out, van voorraadveroudering.
Kleine orders & snelle levering: Een zeer hoge vraag naar tijdige, kleine zendingen is niet efficiënt voor het magazijn.
Traditionele softwaresystemen: Conventionele systemen beperken real-time tracking en optimalisatie van de werking.
Gecompliceerd SKU-beheer: Vereist goede tracering en organisatie omdat het beheren van productvariatie ingewikkeld is.
Gevaarlijke veiligheidsomstandigheden & strikte protocollen: Het veilige gebruik van delicate onderdelen moet nauwgezet voldoen aan zeer strenge normen binnen de industrie.
Belangrijkste vereisten voor opslag van halfgeleiders
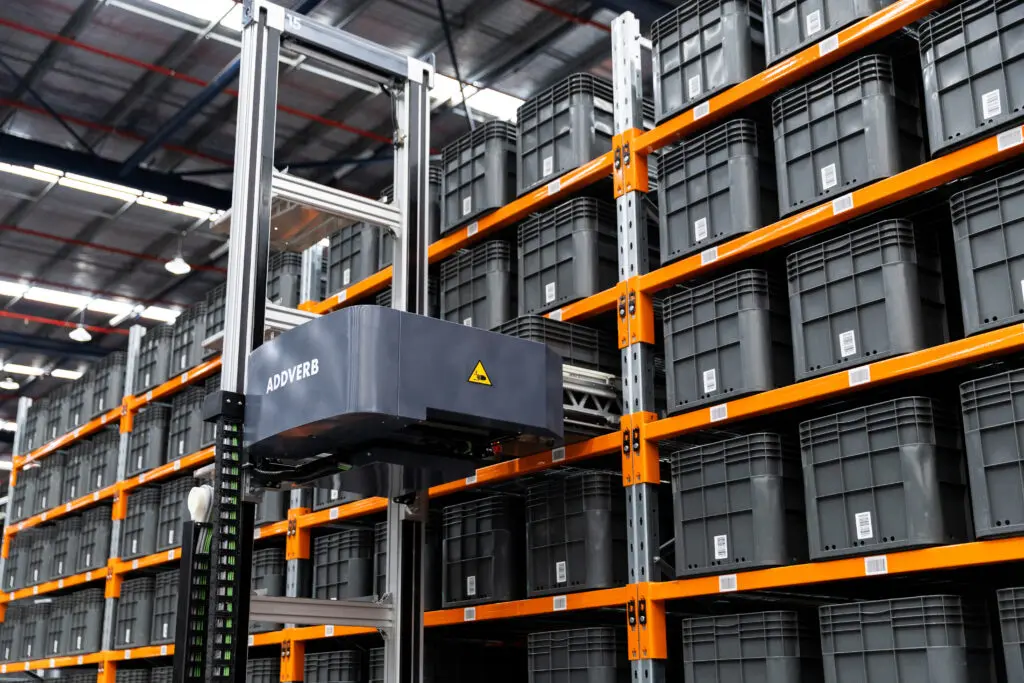
Opslag voor milieugevoelige materialen: Vocht, statische elektriciteit of schokken kunnen halfgeleidermaterialen beschadigen; daarom zijn er vaak specifieke rekken, bakken, opslagapparaten, planken, enz. nodig om schade te voorkomen.
Er moet worden voorzien in extra beveiligingen, zoals beperkte toegang tot de faciliteiten en monitoringsystemen, om diefstal of ongeoorloofde handelingen te voorkomen.
Nauwkeurige verwerking en verplaatsing van materialen. Geautomatiseerde systemen voor het verwerken van materialen, zoals transportbanden, robotarmen en pick-and-place-technologieën, zorgen voor verdere perfectionering van de totale controle voor nauwkeurige en effectieve verplaatsing van artikelen in het magazijn, waarbij, voor zulke delicate materialen, geen beschadigende bewegingen op snelheid zullen plaatsvinden.
Oplossingen voor temperatuurregeling: De gevoelige materialen vereisen automatisering voor optimale prestaties en houdbaarheid omdat ze geen vochtige omstandigheden kunnen verdragen. Verschillende technologieën omvatten magazijnbeheersystemen in combinatie met mobiele robots, die het proces waarschijnlijk zullen verbeteren door effectieve opslag en picking.
Inventaris volgen en beheren in real-time: Real-time voorraadtracering in de halfgeleidermagazijnindustrie is de belangrijkste ondersteunende ruggengraat van goed presterende magazijnen.
Een WMS met barcode/RFID, een geavanceerd magazijnbeheersysteem, zorgt er inderdaad voor dat materialen en eindproducten voortdurend worden getraceerd.
Dit leidt dus tot geoptimaliseerde voorraadniveaus, huurverlagingen door stockouts of te grote voorraden en bestellingen die op tijd en foutloos worden uitgevoerd.
Waarom is automatisering van opslag van halfgeleiders nodig?
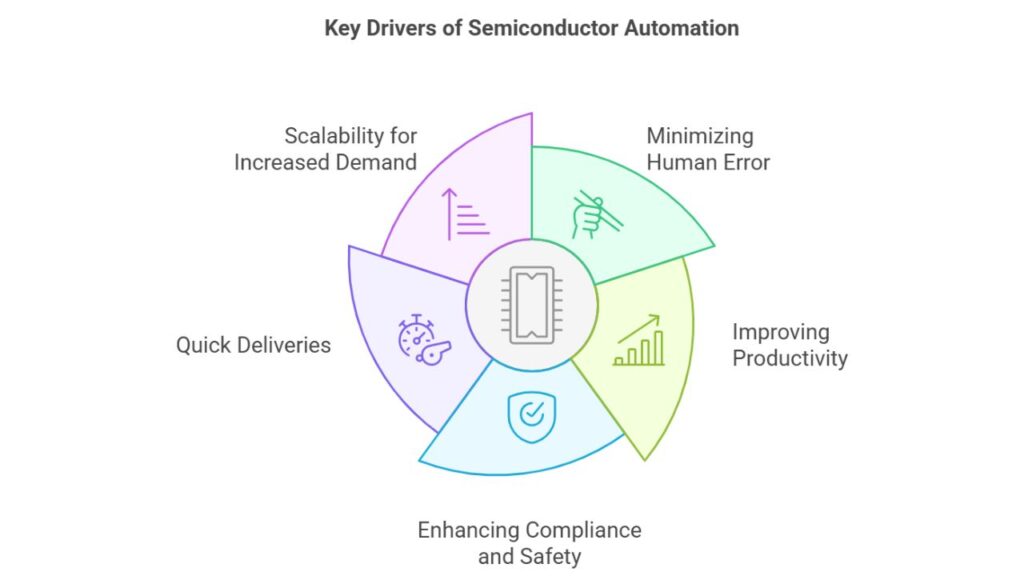
Minimaliseren van menselijke fouten: Automatisering helpt de handmatige activiteiten van een werknemer te verminderen, wat op zijn beurt menselijke fouten vermindert bij het bijhouden van voorraden en het uitvoeren van orders en ook bij de behandeling van gevoelige componenten om een grotere nauwkeurigheid te garanderen.
Verbetering van de productiviteit: Geautomatiseerde systemen maken veel snellere werkprocessen mogelijk voor picken, verpakken en sorteren, waardoor de tijd die nodig is om materiaal te verplaatsen wordt geminimaliseerd en de workflow soepeler verloopt, terwijl er minder gangen hoeven te worden uitgebreid.
Naleving en veiligheid verbeteren: De juiste materiaalverwerking en temperatuurregeling voorkomen menselijke fouten die veiligheidsrisico's met zich meebrengen, en volledige veiligheidsvoorschriften en regelgevende mandaten krijgen een boost door automatisering.
Snelle leveringen: Geautomatiseerde systemen voeren orders sneller en efficiënter uit, omdat orders minder tijd vergen en de leveringssnelheid verbetert, terwijl aan de vraag wordt voldaan door de verwachtingen van de klant ten aanzien van snelheid en doorlooptijd.
Schaalbaarheid voor toenemende vraag: Dankzij automatisering kunnen magazijnen hun activiteiten eenvoudig opschalen om tegemoet te komen aan de stijgende ordervolumes zonder dat de behoefte aan arbeidskrachten in dezelfde mate toeneemt, wat schaalbaarheid en kosteneffectieve flexibiliteit oplevert ten tijde van pieken in de vraag.
Innovatieve oplossingen voor opslag van halfgeleiders bij Addverb
Geautomatiseerde opslag- en zoeksystemen (ASRS)
Ze spelen een belangrijke rol bij het verbeteren van de opslagdichtheid, de ophaalsnelheid en de efficiëntie van de hele operatie. Elk van deze systemen is dan nodig in een prestatiegerichte automatiseringsoplossing voor magazijnen van halfgeleiders:
- Multi-Pro: Optimale bufferopslag en dichte opslag voor snel terugvinden in productie- en verzendzones.
- Quadron: Een veelzijdig shuttlesysteem voor geautomatiseerde opslag van kleine componenten, zoals IC's, voor een hoge verwerkingscapaciteit en ruimtebesparing.
- Cruiser 360: Pallet-shuttle systeem voor massamateriaal, dat maximale verticale ruimte bereikt met veilige bediening en effectieve opslag van zware ladingen.
- Skyron: crane, een zeer nauwkeurige handlingoplossing voor zware pallets. In combinatie met een hoge real-time inventarisatiecapaciteit is het ook een zeer flexibel geautomatiseerd lastverwerkingssysteem.
- Medius: Een shuttlesysteem met meerdere niveaus, ontworpen voor het snel en compact opbergen en terugvinden van kleine voorwerpen, dat verticale ruimte inneemt voor maximaal 7 opslagniveaus.
Mobiele robots (AMR's)
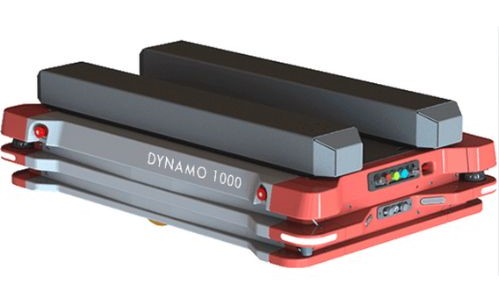
De mobiele robot Dynamo verbetert de automatisering van de opslag van halfgeleiders door de zeer breekbare onderdelen te vervoeren via een volledig autonoom transportsysteem. Deze machines zijn uitgerust met LiDAR voor veilige navigatie door magazijnen, waarbij gebruik wordt gemaakt van AI-algoritmen om het handwerk te verbeteren zodat menselijke fouten worden voorkomen.
Door hun kleine formaat kunnen de machines krappe ruimtes bereiken met hun handelingen, wat de optimale magazijnindeling aanvult.
AMR's automatiseren het transport van gevoelige materialen en beloven een nauwkeurige verwerking met een minimale kans op besmetting, naast het verbeteren van de efficiëntie in het hele ecosysteem van de productie en opslag van halfgeleiders.
Picken van persoon tot persoon
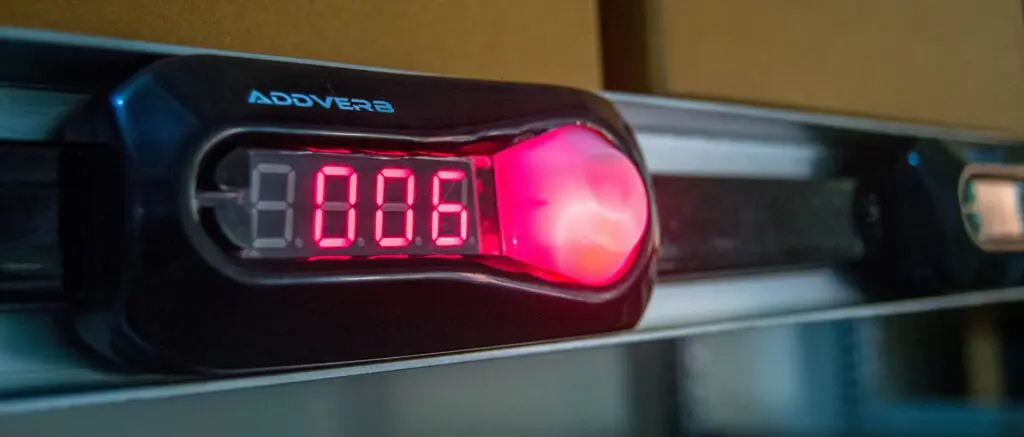
De samenwerking tussen Rapido en Zesty zou een zeer effectief en nauwkeurig proces van orderverwerking mogelijk maken in magazijnen en productieomgevingen voor halfgeleiders.
De Pick-to-Light-oplossing van Rapidostelt operators in staat om snel en nauwkeurig producten en lijnen te identificeren met behulp van verlichte indicatoren.
Dergelijk snel en foutloos orderverzamelen is echt belangrijk in de snel bewegende omgeving van halfgeleiderfabricage en -verzending, waar het bij gevoelige materialen en componenten aankomt op nauwkeurigheid.
Aan de andere kant elimineert Zesty de noodzaak voor papier of RF-apparaten door operators te laten werken met spraakopdrachten voor de Pick-by-Voice technologie.
Simpel gezegd, met behulp van de nieuwste ontwikkelingen op het gebied van spraakherkenning, horen machinisten real-time, handsfree instructies, waardoor ze zich zonder afleiding kunnen concentreren op de uit te voeren taak.
Laatste gedachten
Automated Storage and Retrieval Systems (ASRS), Automated Mobile Robots (AMRs), and smart picking technologies like Rapido and Zesty have made this possible. This means that semiconductor warehousing doesn’t have to worry about speed, accuracy, or efficiency when working with sensitive materials.
Bij Addverb blinken we uit in onze expertise, zodat semiconductor warehousing bedrijven deze perfecte en geavanceerde automatiseringssystemen kunnen implementeren om hun activiteiten een hoge kwaliteit te geven en te voldoen aan de eisen die klanten stellen.
Bezoek Addverb vandaag nog en ontdek hoe onze futuristische technologieën uw magazijnprocessen transformeren en ze naar de toekomst van de halfgeleiderlogistiek leiden.
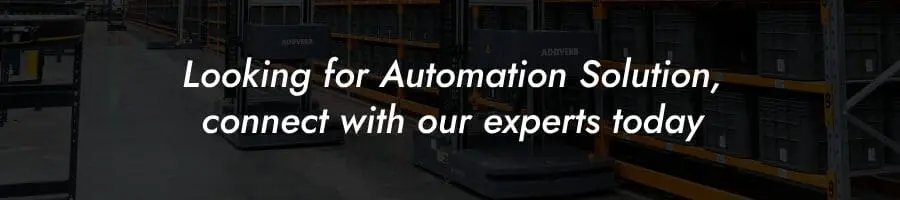