Inhaltsübersicht
Bei der Lagerverwaltung geht es, wie bei jeder anderen Führungsposition auch, darum, die wichtigsten KPIs zu ermitteln, die sich auf die Unternehmensleistung auswirken. Außerdem geht es um die Bereitstellung der Instrumente und Ressourcen, die zur Erfüllung dieser KPIs erforderlich sind.
Wenn es sich um ein bereits bestehendes Lager handelt, ist der verfügbare Platz das Hauptkriterium für die Wahl zwischen dichten Regalsystemen und herkömmlichen Regalsystemen. Wenn es jedoch um die Verwaltung von Lagern im Allgemeinen geht, hängt diese Wahl von zwei Faktoren ab, nämlich von Bestandseigenschaften wie Haltbarkeit und Anzahl der Artikel und von betrieblichen Zielen wie schnelle Lieferung, niedrige Kosten usw. Bevor wir fortfahren, wollen wir zunächst beschreiben, wie herkömmliche und dichte Regalsysteme definiert sind:
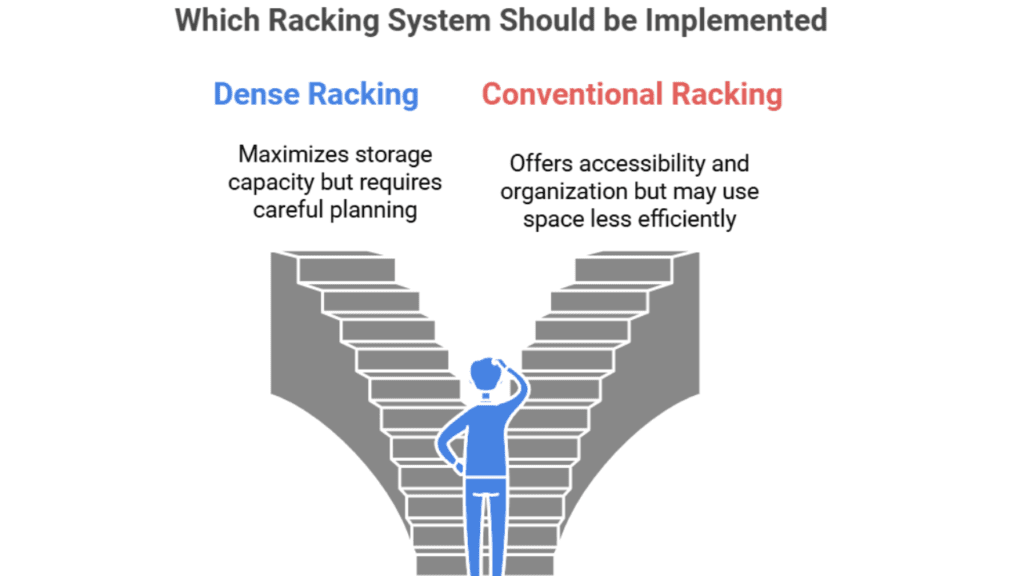
Was sind konventionelle Regale?
Selektive Palettenregale oder konventionelle Regale sind die am häufigsten verwendeten Lagerungssysteme. Es ermöglicht den direkten Zugriff auf alle Paletten und kann in Lagern mit vielen SKUs (Stock Keeping Units) eingesetzt werden.
Vorteile der konventionellen Regale
Zugänglichkeit: Es bietet jeder Palette einen direkten Zugang, wodurch es sich sehr gut für eine hohe SKU-Sorte eignet.
Vielseitigkeit: Fast jede Produktart.
Niedrige Anfangskosten: Sie sind einfacher und billiger zu installieren und zu warten.
Nachteile der konventionellen Regale
Geringe Lagerdichte: Es wird mehr Bodenfläche zwischen den Regalen benötigt, da zwischen den Regalen Gänge vorhanden sind.
Raumausnutzung: Der vertikale und horizontale Raum kann nicht nachhaltig maximiert werden.
Was ist ein dichtes Regalsystem?
Dichte Regalsysteme, wie Drive-in, Drive-through, Push-back oder Palettenfluss, zielen darauf ab, die Lagerdichte zu maximieren. Sie sparen Platz im Gang und nutzen sowohl den vertikalen als auch den horizontalen Raum besser aus.
Vorteile von dichten Regalen
Hohe Lagerdichte: Ein perfekter Ort, um Produkte desselben Typs in großer Zahl zu lagern.
Platzersparnis: Es reduziert den Platzbedarf für die Lagerung, wodurch Boden und vertikaler Raum frei werden.
Anpassbarer Fluss: Ein Inventarsystem kann so aufgebaut werden, dass es FIFO (First in, first out) oder LIFO (last in, first out) unterstützt.
Nachteile von dichten Regalen
Selektiver Zugriff: Bestimmte Paletten können schwieriger abzurufen sein.
Komplexität: Sie erfordert geschultes Personal und spezielle Handhabungsgeräte.
Höhere Investitionen: Geringere Dichte im Vergleich zu herkömmlichen Regalen.
Hauptunterschiede zwischen dichten Regalen und konventionellen Regalen
Merkmal | Dichtes Regal | Konventionelle Regale |
Speicherkapazität | Lager mit hoher Dichte für Schüttgut. | Geringere Dichte, besser geeignet für Vielfalt. |
Erreichbarkeit | Begrenzter Zugang zu bestimmten Paletten. | Direkter Zugang zu jeder Palette. |
Inventarfluss | Großvolumige, schnell umschlagende Bestände. | Hohe Selektivität, geeignet für kleine Stückzahlen oder unterschiedliche Artikel. |
Raumausnutzung | Maximiert den vertikalen und horizontalen Raum. | Benötigt aufgrund der Gänge mehr Bodenfläche. |
Kosten | Höhere Anfangsinvestitionen. | Geringere Anfangskosten. |
Beliebte Schüttgut-Lagerregalsysteme
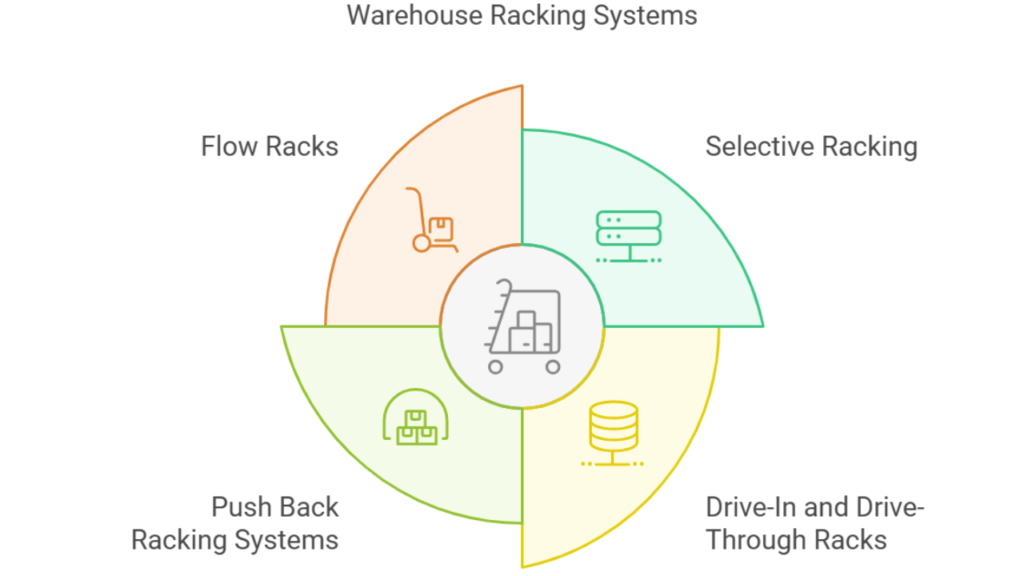
Selektive Regale
Selektivregale sind das am häufigsten verwendete Palettensystem, das den Zugriff von einem Gang aus ermöglicht. Sie eignen sich ideal für Schmalgangregale, Standardsysteme und Tiefgangsysteme. Selektivregale erfordern spezielle Schmalgangstapler und bieten Platz für eine einzige Palette in der Tiefe. Dieses System hat die geringste Lagerkapazität von Paletten und auch die niedrigsten Kosten pro Palette; es ist jedoch nicht skalierbar und wird teuer, wenn die Anzahl der Palettenplätze 3000 übersteigt. Bei einer größeren Anzahl von Palettenplätzen und Produktlinien bietet das dichte Regalsystem jedoch eine größere Kostenoptimierung und reduziert die Lagerkosten um 20-50%.
Nach Ansicht der grand view research führte das Segment der selektiven Paletten den Markt mit dem größten Umsatzanteil von 45,0% im Jahr 2024 an.
Drive-In- und Drive-Through-Regale
Einfahrregale werden für eine hohe Lagerdichte verwendet und haben einen Eingang und einen Ausgang. Diese Regale eignen sich gut für die LIFO-Lagerung. Durchfahrregale, die an beiden Enden Zugang haben, sind besser für FIFO-Prozesse geeignet. Beide Systeme erfordern Gabelstapler, um in das Regal zu gelangen. Sie stellen jedoch ein Sicherheitsrisiko für die Staplerfahrer dar und eignen sich nicht für kleine Chargen oder eine große Produktvielfalt.
Push Back Racking Systeme
Push-back-Regalsysteme sind für die Lagerung von Schüttgut konzipiert, in der Regel für 2-5 Paletten. Wenn eine Palette beladen wird, schiebt sie die nächste Palette zurück. Das System arbeitet auf LIFO-Basis und verfügt über geneigte Schienen und Schiebewagen. Im Gegensatz zu Drive-in-Systemen müssen bei diesem System keine Gabelstapler in die Gassen fahren, was die Sicherheit des Bedieners erhöht. Allerdings hat das System eine begrenzte Reichweite mit maximal 4-5 Zugangswegen.
Durchlaufregale
Durchlaufregale, auch als Schwerkraftregale bekannt, werden für die Lagerung von Produkten mit hoher Dichte verwendet, oft bis zu 20 oder mehr Paletten tief. Die Produkte werden am oberen Ende eingelagert und am unteren Ende nach einem FIFO-System entnommen. Diese Regale arbeiten mit Schwerkraftrollen und benötigen keinen Strom. Sie sind jedoch teurer als herkömmliche Regalsysteme und haben eine schlechte Zugänglichkeit zu allen Paletten.
Die Wahl des richtigen Systems für Ihre Bedürfnisse
Für große Mengen von Artikeln mit geringer Stückzahl, wie FMCG oder Kühllager, können Sie dichte Regale verwenden. Wenn Sie einen vielfältigen Bestand mit häufigem Artikelumschlag verwalten, sollten Sie sich für konventionelle Regale entscheiden. Dichte Regalsysteme können den verbleibenden Platz optimal ausnutzen, da sie weniger Gänge benötigen. Herkömmliche Regale eignen sich hervorragend für den schnellen und häufigen Zugriff. Dichte Regale sind die optimale Wahl für die effiziente Lagerung von Schüttgut.
Merkmale des Lagerbestands: Verwenden Sie dichte Regale für Betriebe mit hohem Volumen und geringer Stückzahl wie FMCG oder Kühllager. Entscheiden Sie sich für konventionelle Regale, wenn Sie ein vielfältiges Inventar mit häufigem SKU-Umschlag verwalten.
Platz im Lager: Wenn der Platz begrenzt ist, können dichte Regalsysteme die verfügbaren Flächen optimieren, da weniger Gänge benötigt werden.
Betriebliche Prioritäten: Herkömmliche Regale sind ideal für schnellen und häufigen Zugriff. Dichte Regale sind die bessere Wahl für eine effiziente Schüttgutlagerung.
Budgetüberlegungen: Berücksichtigen Sie den langfristigen ROI. Dichte Regale haben höhere Anschaffungskosten, bieten aber eine größere Raumdichte, senken die Betriebskosten und verzögern die Notwendigkeit einer Lagererweiterung.
Schlussfolgerung
Sowohl dichte Regale als auch konventionelle Regale haben ihre eigenen Stärken und Grenzen. Die Wahl hängt von Ihren betrieblichen Prioritäten, den Bestandseigenschaften und der Platzverfügbarkeit ab. Wenn Sie diese Systeme und ihre Anwendungen verstehen, können Sie eine fundierte Entscheidung treffen, um die Lagereffizienz und Gesamtleistung Ihres Lagers zu verbessern.
Wenn Sie bereit sind, Ihre Lagerhaltung zu transformieren, entdecken Sie die fortschrittlichen Lösungen von Addverb und maximieren Sie Ihr betriebliches Potenzial!
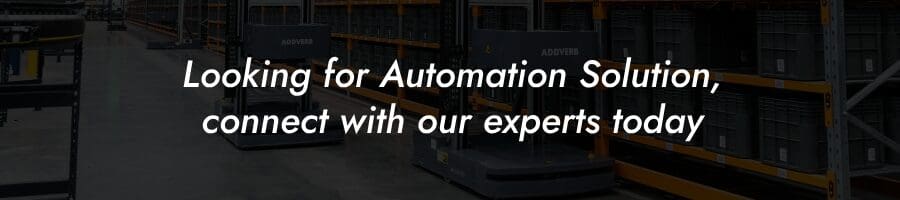
FAQ
Was ist ein dichtes Regalsystem?
Dichte Regalsysteme, wie Paletten-Shuttles oder Einfahrregale, maximieren die Raumnutzung, indem sie eine hochdichte Lagerung mit minimalen Gängen ermöglichen.
Was ist ein konventionelles Regal?
Bei konventionellen Regalsystemen, wie z. B. selektiven oder doppelttiefen Regalen, stehen Zugänglichkeit und Flexibilität anstelle von Dichte im Vordergrund, wobei jeder Reihe ein Gang zugeordnet ist.
Was eignet sich besser für eine hohe SKU-Vielfalt?
Herkömmliche Regale eignen sich besser für eine hohe SKU-Vielfalt, da sie einen einfachen Zugriff auf einzelne Paletten ermöglichen.
Welches Regalsystem ist für die Kühllagerung besser geeignet?
Dichte Regale sind aufgrund ihrer kompakten Bauweise ideal für die Kühllagerung, da sie den Kühlraum minimieren und die Energiekosten senken.
Wie wirken sich dichte Regalsysteme auf den Materialtransport aus?
Für einen effizienten Betrieb sind oft spezielle Geräte wie Palettenwagen oder Gabelstapler erforderlich.
Sind dichte Regalsysteme kosteneffizient?
Ja, sie optimieren die Lagerkapazität und senken langfristig die Lagerkosten pro Palette.