Índice
Se prevé que el mercado mundial de la automatización de la asistencia sanitaria alcance los 42.590 millones de USD en 2024; seguirá creciendo hasta alcanzar los 46.850 millones de USD en 2025 y se situará en torno a los 110.470 millones de USD en 2034, con una CAGR de crecimiento específica del 6,2% de 2024 a 2034.
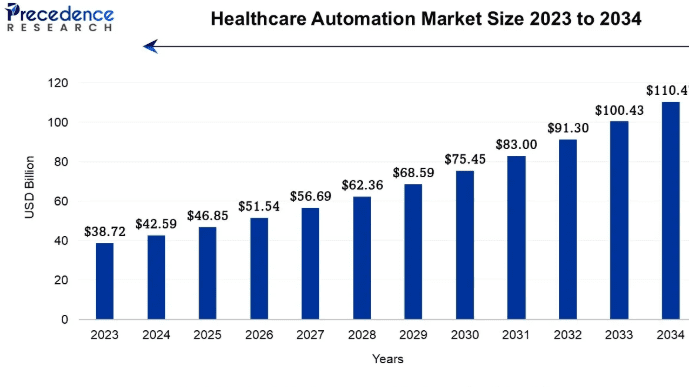
Tecnologías como los sistemas automatizados de almacenamiento y recuperación, los clasificadores robotizados y los robots móviles autónomos son motores de la transformación de las operaciones de almacenamiento y cadena de suministro que está surgiendo ante la creciente demanda de eficiencia y precisión en el almacenamiento farmacéutico.
En este blog, desentrañaremos cómo estas innovaciones están ayudando a los responsables de los almacenes sanitarios y farmacéuticos a aumentar la eficiencia, reducir los errores y satisfacer la creciente demanda.
Principales retos del almacenamiento sanitario y farmacéutico
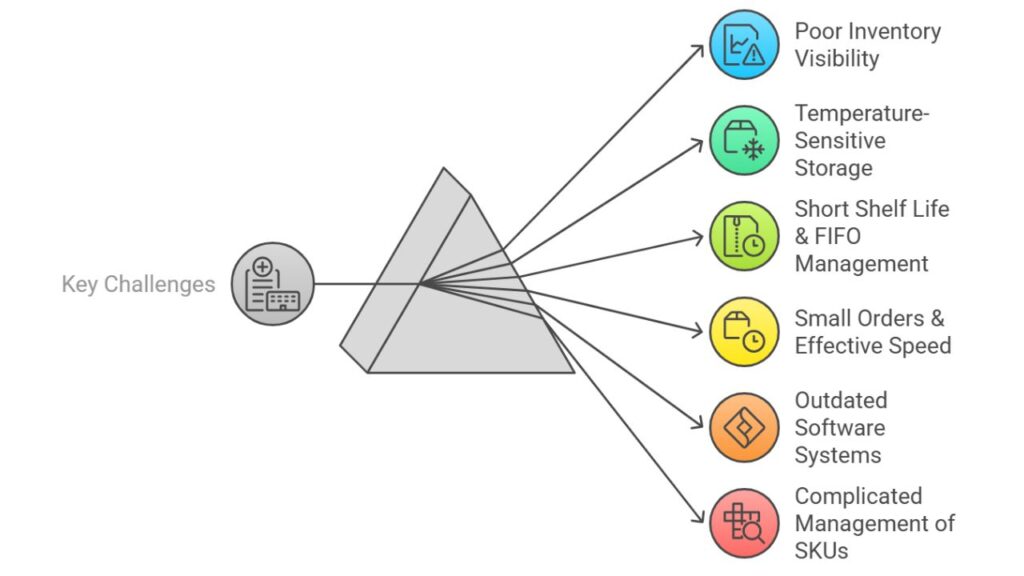
Escasa visibilidad del inventario: Es el resultado de un seguimiento inadecuado de las existencias en los almacenes farmacéuticos, lo que posteriormente da lugar a roturas de stock o exceso de existencias que, en última instancia, provocan retrasos y pérdidas durante las operaciones de procesamiento.
Almacenamiento sensible a la temperatura: Mantener la temperatura adecuada es crucial para garantizar la seguridad y la conformidad de los productos. Los sistemas monitorizados ofrecen garantías de integridad y evitan pérdidas costosas y derrochadoras.
Vida útil corta y gestión FIFO: Utilizar eficientemente el FIFO es primordial para evitar que salgan al mercado productos viejos, garantizando la seguridad y la reducción de residuos.
Pedidos pequeños y rapidez efectiva: la demanda de pedidos pequeños y urgentes desarrolla sistemas muy ágiles para responder con precisión y rapidez a la demanda de los clientes.
Sistemas informáticos obsoletos: Los sistemas tradicionales se concentran en la automatización y el seguimiento en tiempo real, por lo que reducen la eficiencia. Las soluciones modernas mejoran las operaciones y el cumplimiento, con lo que aumentan la productividad y la eficiencia.
Gestión complicada de SKU: Una tarea muy sofisticada es la gestión de varias SKU. Los procesos ineficaces de racionalización y previsión reducen la precisión y aumentan los cuellos de botella.
Clasificación rápida: Es necesario integrar sistemas de clasificación eficientes para clasificar y dirigir los productos de forma rápida y precisa, mejorando la velocidad de las operaciones y reduciendo los errores humanos.
Demanda creciente: El aumento de la demanda de productos sanitarios y farmacéuticos obliga a los almacenes a funcionar con mayor eficacia y a la vez satisfacer con prontitud las necesidades de sus clientes.
Deben centrarse en mejorar la eficiencia, minimizar los gastos y garantizar la entrega segura de los productos más cruciales.
Requisitos comunes de los almacenes sanitarios
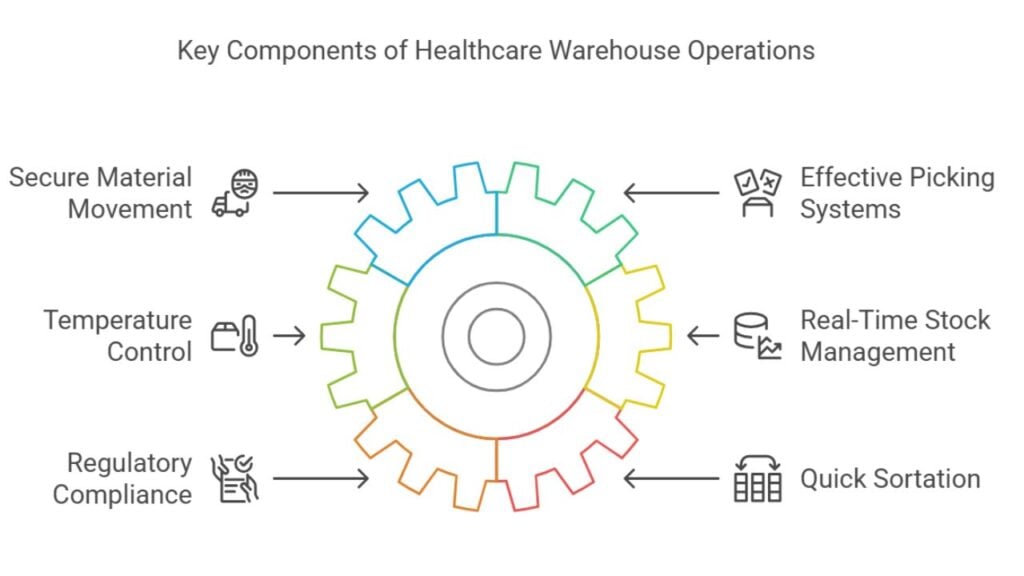
Movimiento de material en un entorno seguro: Un entorno seguro en el que se trasladen todos los materiales es un requisito esencial para evitar cualquier tipo de daño, contaminación o robo. Esto garantizará el movimiento fluido de los productos sanitarios tanto dentro del almacén como hacia sus lugares de venta.
Sistemas de picking eficaces: Un sistema de picking altamente eficaz es fundamental para agilizar el cumplimiento de los pedidos, reducir los errores de picking y facilitar la automatización o el escaneado de códigos de barras para garantizar que se eligen con rapidez y precisión los productos sanitarios adecuados para su entrega.
Soluciones de temperatura controlada: El control de la temperatura es imprescindible para la mayoría de los productos farmacéuticos. Es necesario garantizar que los almacenes ofrezcan soluciones especializadas de almacenamiento y vehículos para realizar su trabajo y mantener los límites de temperatura prescritos para los artículos sensibles, garantizando al mismo tiempo su seguridad y eficacia.
Gestión de las existencias en tiempo real: se trata de un requisito esencial para la organización con el fin de planificar la no disponibilidad de existencias o el exceso de existencias en los almacenes, de modo que los recursos estén disponibles para completar los pedidos en cualquier momento utilizando las cantidades correctas.
Cumplimiento de las normas reglamentarias: Los almacenes sanitarios y farmacéuticos deben cumplir estrictas normas reglamentarias como GDP y GMP que garantizan la seguridad, calidad y trazabilidad de los productos. El cumplimiento de la legislación es un aspecto importante, pero también lo es la seguridad de los pacientes.
Solución de clasificación rápida: Los sistemas de clasificación de alto rendimiento son necesarios en los almacenes más populares para agrupar rápidamente los productos y enviarlos a su destino final. Acelera las operaciones, minimiza los errores y garantiza la expedición puntual de los productos, lo que contribuye a una cadena de suministro más eficaz.
Todas estas condiciones juntas forman la espina dorsal de una operación eficiente de almacenamiento sanitario y farmacéutico que mantiene las cosas dentro del ámbito de la seguridad, dentro del plazo y con precisión en la entrega de productos.
¿Por qué es necesaria la automatización del almacenamiento farmacéutico?
Minimización de los errores humanos y mejora de la precisión: La automatización minimiza los errores manuales y, por tanto, permite una perfecta ejecución de los pedidos y ahorra errores relacionados con las operaciones de almacenamiento de productos sanitarios y farmacéuticos.
Aumento de la eficacia y la rapidez operativas: Los sistemas automatizados agilizan el proceso de preparación de pedidos, embalaje y envío para que la entrega sea más rápida en el tiempo.
Garantizar el cumplimiento de la normativa y la seguridad: La automatización hace que la normativa se mantenga intacta gracias a la coherencia de los procesos y la documentación, lo que garantiza la calidad del producto y la seguridad para los pacientes.
Mejores rotaciones de inventario y gestión FIFO: Los sistemas de inventario automatizados realizan un seguimiento de las existencias en tiempo real para optimizar la rotación, así como la gestión FIFO (primero en entrar, primero en salir), reduciendo los residuos y los productos caducados.
Reducción de los costes laborales y de la dependencia de la mano de obra: La automatización de actividades repetitivas disminuye la mano de obra en los almacenes, lo que se traduce en un descenso de los costes operativos y de la dependencia de la mano de obra.
Mayor eficiencia de almacenamiento: La automatización facilita una mejor utilización del espacio y maneja bien las condiciones de almacenamiento del producto para una mejor gestión del almacenamiento y menos residuos.
Soluciones innovadoras para el almacenamiento sanitario
Sistemas de almacenamiento y recuperación automatizados (ASRS)
ASRS desarrolla y diseña sistemas de almacenamiento y recuperación de alta densidad altamente personalizados y eficaces para almacenes farmacéuticos.
El sistema de lanzaderas multi-pro aumenta significativamente el rendimiento al liberar las lanzaderas infantiles para su almacenamiento automatizado.
El transbordador de palés Cruiser 360 ofrece un control del espacio de almacenamiento o recuperación completamente activo y eficiente desde el punto de vista operativo con Wi-Fi y una batería de larga duración.
El crane Skyron ofrece seguimiento de inventario en tiempo real y también permite cargas de hasta 1.500 kg.
Las aplicaciones sanitarias mejoradas están implantando diversas soluciones en las áreas de almacenamiento, recuperación ygestión de inventarios.
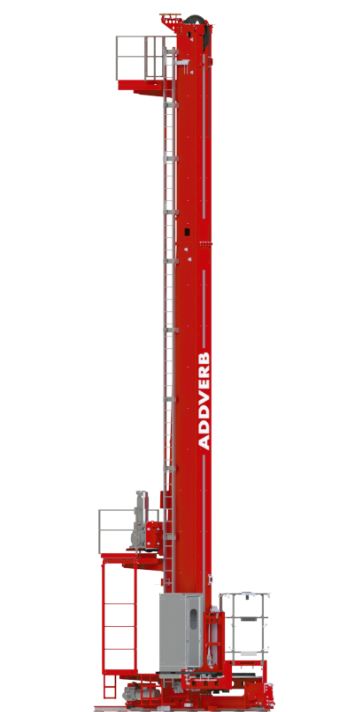
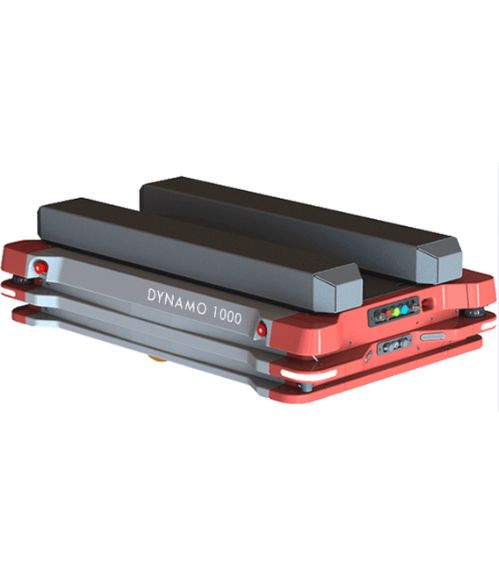
Robots móviles para el movimiento de materiales.
Dynamo, un robot móvil autónomo (AMR), realiza el transporte de materiales con gran rapidez y eficacia, al tiempo que reduce la exposición a daños o contaminación de objetos sensibles en almacenes farmacéuticos.
Gracias a su robusto chasis y a sus fiables sensores LiDAR, es más compacta para el movimiento seguro y fluido de materiales pesados y peligrosos.
Utiliza la IA y los algoritmos más avanzados para optimizar los pedidos reduciendo significativamente la intervención humana que suele afectar a la fiabilidad operativa.
Vehículos guiados por raíles y cintas transportadoras para intralogística
Nuestros sistemas de vehículos guiados por raíles (RGV) Travect y transportadores- agilizan el movimiento de materiales en un almacén sanitario.
Travect permite el transporte rápido y preciso de palés a velocidades de hasta 3 m/s con una capacidad de carga útil de 1500 kg, minimizando la manipulación manual y la contaminación.
Combinado con nuestros transportadores de primera clase, optimiza la eficacia y la seguridad en todos los procesos, desde la preparación de pedidos hasta el movimiento y la clasificación de materiales en el entorno de los almacenes farmacéuticos.
Clasificación
Zippy y SortIE son robots clasificadores para almacenes sanitarios y farmacéuticos que aportan automatización y facilitan el cumplimiento de los pedidos gracias a su velocidad, precisión y flexibilidad.
Zippy clasifica las SKU a un ritmo significativamente más rápido, junto con un sensor de detección de obstáculos integrado, que permite establecer la clasificación de los artículos para varios destinos. Por tanto, su diseño se adapta específicamente a entornos dinámicos.
SortIE es un clasificador vertical modular que ordena rápidamente los paquetes en un sistema de "puesta en pared" mediante control de movimiento y un mecanismo de transmisión por correa.
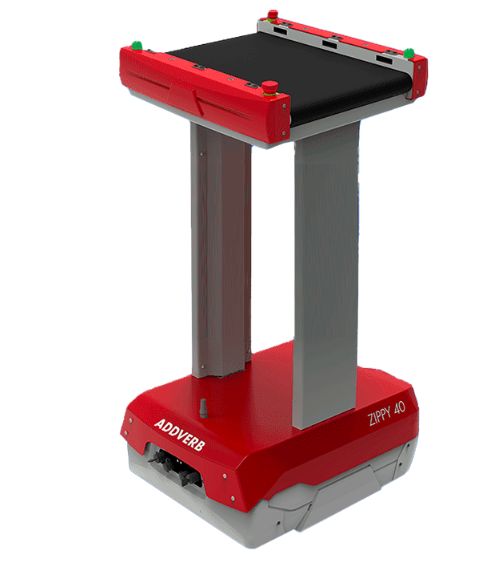
Estudio de caso: Sistema de almacenamiento multiprofundo Par Pharma
Situación: Par Pharma se enfrentaba a los retos de establecer plataformas de almacenamiento muy limitadas; adoptar el picking manual; lagunas en la escasez de mano de obra; y una trazabilidad deficiente para sus productos, lo que reducía el apetito por los niveles deseados de eficiencia-almacenamiento-densidad-visibilidad.
Acción: Añadiendo un sistema de almacenamiento en profundidad múltiple, configurando la manipulación automatizada de materiales mediante la combinación de la carretilla elevadora, las cintas transportadoras y las lanzaderas Cruiser con unidades ASRSCrane , Addverb controló la integración del software Mobinity WCS para obtener datos y control en tiempo real.
Resultado: El sistema logró el seguimiento del 100% de los productos y la optimización del almacenamiento de 4050 posiciones multiprofundas, mejorando la velocidad, la precisión y la eficacia operativa.
Conclusión
¿Está listo para optimizar los procesos de su almacén sanitario o farmacéutico? ¿A qué está esperando? Póngase en contacto con Addverb ahora mismo para saber cómo nuestra automatización de vanguardia puede innovar los procesos de almacenamiento, maximización de la eficiencia y seguimiento del inventario en tiempo real en su almacén.
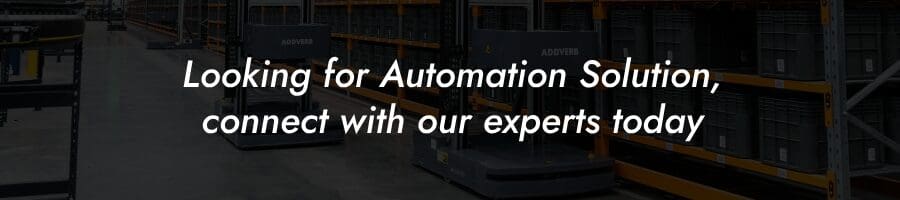
PREGUNTAS FRECUENTES
¿Cuáles son los principales retos del almacenamiento farmacéutico?
Mantener el control de la temperatura, la precisión del inventario, la manipulación de productos de vida útil corta y la gestión de diversas referencias.
¿Cómo mejora la automatización la gestión del inventario?
Ofrece seguimiento en tiempo real, control preciso de las existencias y cumplimiento eficaz de los pedidos.
¿Qué papel desempeñan los ASRS en los almacenes farmacéuticos?
Los ASRS optimizan el almacenamiento y la recuperación, mejorando la utilización del espacio y el acceso a los productos.
¿Cómo ayuda la automatización al almacenamiento sensible a la temperatura en los almacenes farmacéuticos?
Garantiza la supervisión y el control continuos de las condiciones de almacenamiento para mantener la integridad del producto.
¿Qué ventajas aporta la automatización a la gestión de las SKU?
Agiliza el almacenamiento y la recuperación, reduciendo los errores y mejorando la precisión de los pedidos.