Índice
La asignación de ubicaciones en el almacén organiza estratégicamente los productos dentro de un almacén para promover la utilización del espacio, el cumplimiento de los pedidos y la eficiencia operativa. Examinando cuidadosamente la colocación de los productos, los jefes de almacén pueden reducir sustancialmente los tiempos de preparación de pedidos, reducir las distancias recorridas por los trabajadores y optimizar los procedimientos generales del almacén. Conozcámoslo en detalle a través de sus enfoques, consideraciones críticas, beneficios, mejores prácticas, retos y la importancia de utilizar el slotting para mejorar la eficiencia operativa.
La asignación de ubicaciones en el almacén consiste en asignar lugares de almacenamiento a los productos dentro de un almacén. Su objetivo es mantener los artículos de uso más frecuente en lugares de fácil acceso, mientras que los artículos de uso menos frecuente se guardan en zonas que requieren una recuperación menos frecuente. El objetivo es mejorar el proceso de picking, reducir el tiempo de desplazamiento de los trabajadores y, en última instancia, aumentar la eficiencia del almacén. Incluye el examen de los datos de los productos, el historial de compras y las tendencias de ventas para decidir dónde debe guardarse cada artículo. Los almacenes pueden utilizar esta estrategia basada en datos para reducir los costes de mano de obra, aumentar la productividad y minimizar los errores.
¿Qué es la macro y microranura?
El ranurado de almacenes puede dividirse en dos tipos: Macro-Slotting y Micro-Slotting.
La macrodistribución implica tomar decisiones de alto nivel sobre la disposición general del almacén. Se trata de establecer las ubicaciones óptimas para las distintas categorías de productos, teniendo en cuenta aspectos como las dimensiones de los productos, la demanda y las necesidades de almacenamiento. El objetivo principal de la macroperfilación es optimizar el flujo global de mercancías dentro del almacén, garantizando que los productos se guardan de la forma más eficaz y lógica posible.
Por su parte, la micro-slotting se ocupa del posicionamiento de las SKU individuales dentro de sus respectivas categorías de productos. Tiene en cuenta parámetros específicos como la popularidad del producto, la frecuencia de los pedidos y las dimensiones del artículo. Al disponer deliberadamente los productos de alta demanda en lugares de fácil acceso, la microperforación pretende maximizar la eficacia de los procesos de preparación de pedidos. El micro-slotting reduce el tiempo y el esfuerzo necesarios para que los trabajadores recojan los artículos optimizando la disposición de los productos individuales, lo que se traduce en un cumplimiento más rápido de los pedidos y una mayor eficiencia operativa.
Ventajas de una asignación eficaz de las franjas horarias de los almacenes
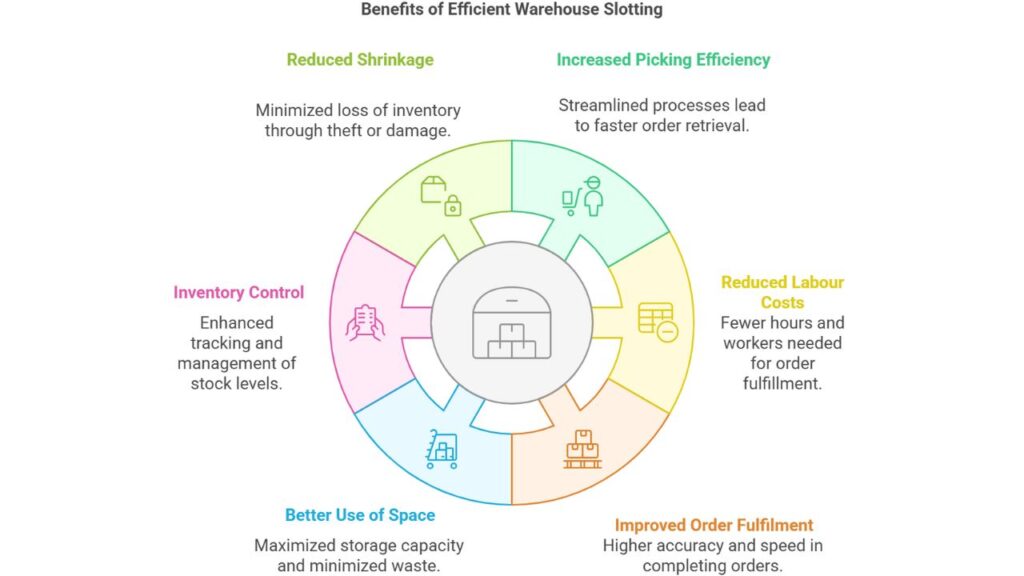
La aplicación de un plan eficaz de optimización de las franjas horarias del almacén puede aportar diversas ventajas:
Mayor eficacia de picking
Al colocar los artículos de alta demanda en lugares de fácil acceso, los empleados pueden completar los pedidos más rápidamente y con menos errores.
Reducción de los costes laborales
La asignación óptima de franjas horarias reduce el tiempo de desplazamiento de los trabajadores, lo que se traduce en menores costes laborales y mayor producción.
Mejora de la tramitación de pedidos
Los métodos de picking más rápidos y precisos aumentan el índice de cumplimiento de los pedidos y la satisfacción de los clientes.
Mejor aprovechamiento del espacio
La distribución eficiente del almacén permite un uso más eficaz del espacio, eliminando la demanda de instalaciones de almacenamiento adicionales.
Control de inventario
Una distribución bien organizada permite una mejor gestión del inventario y reduce la probabilidad de que se agoten las existencias.
Reducción de la contracción y los daños
Un ranurado adecuado puede ayudar a reducir los daños y las pérdidas de producto causados por el maltrato.
¿Por qué son necesarias las franjas horarias?
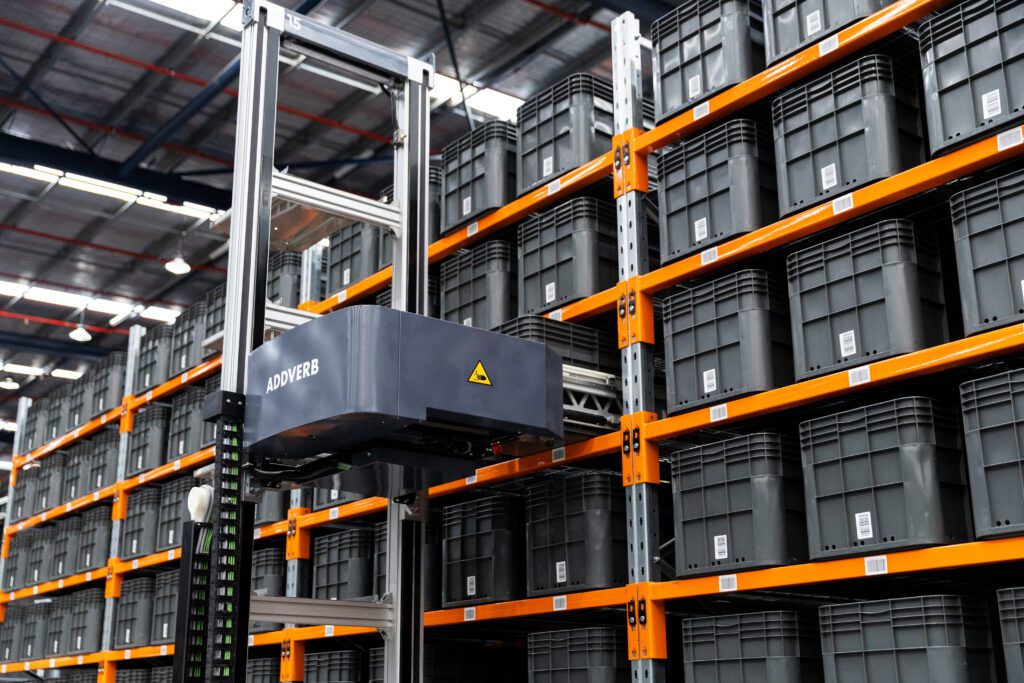
Poner en práctica la asignación de huecos en el almacén es esencial por varias razones:
Ahorro de tiempo
La eficacia en la colocación de los artículos tiene la importante ventaja de ahorrar mucho tiempo. Cuando los artículos se organizan y almacenan adecuadamente, pueden descubrirse rápidamente, lo que evita que los trabajadores tengan que realizar búsquedas que llevan mucho tiempo. Como resultado, la tramitación de pedidos se agiliza y simplifica, lo que aumenta la eficacia general. Se pueden procesar más pedidos en el mismo tiempo con tiempos de procesamiento más cortos, lo que aumenta el rendimiento y la productividad.
Ahorro de costes
La optimización de las franjas horarias reduce significativamente los costes y ahorra mucho tiempo. Como los empleados pueden dedicar más tiempo a tareas productivas que a desplazarse al almacén, los costes laborales se reducen como consecuencia de la disminución del tiempo de desplazamiento de los trabajadores. Además, al aprovechar al máximo su capacidad de almacenamiento actual, las empresas pueden evitar tener que realizar inversiones adicionales en instalaciones de almacenamiento. Esta estrategia económica aumenta el rendimiento final del almacén y genera un ahorro financiero considerable.
Satisfacción del cliente
La satisfacción del cliente es un factor crucial que mejora positivamente con un slotting eficaz. Con una ejecución de pedidos más rápida y precisa, las empresas pueden cumplir sistemáticamente los plazos de entrega y minimizar las dificultades de los pedidos. En consecuencia, los clientes viven experiencias maravillosas, lo que aumenta su satisfacción y fidelidad. Los clientes satisfechos con sus compras son más propensos a realizar más compras y a recomendar la marca a otras personas, lo que beneficia la posición de la empresa en el mercado y su reputación.
Ventaja competitiva
Un almacén bien surtido también proporciona a una empresa una clara ventaja competitiva. Las empresas pueden desmarcarse de la competencia en un sector tan competitivo ofreciendo un procesamiento de pedidos rápido y fiable. Un servicio de atención al cliente eficaz y una entrega fiable atraen a los clientes, lo que aumenta el atractivo y el atractivo de la empresa para otros nuevos. Esta ventaja competitiva puede traducirse en un aumento de la cuota de mercado, un mayor crecimiento de la clientela y, en última instancia, mayores beneficios.
¿Cómo se realizan las ranuras en un almacén?
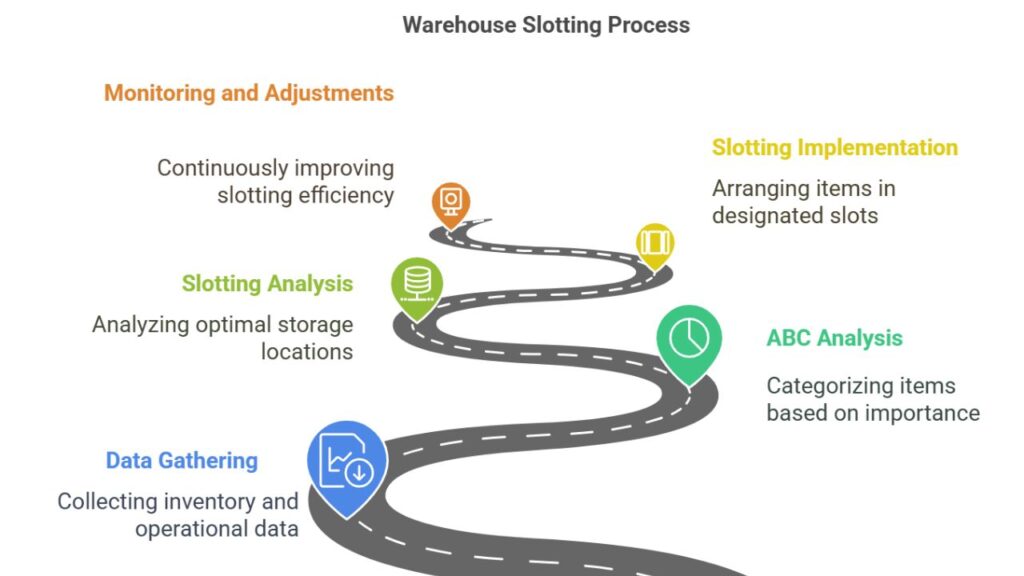
La optimización de la asignación de huecos en los almacenes es una estrategia metódica y basada en datos para mejorar la colocación de los productos, lo que se traduce en una mayor eficacia operativa. El procedimiento de asignación de ubicaciones suele incluir los siguientes pasos:
Recopilación de datos
El primer paso consiste en recopilar datos útiles sobre los productos del almacén. Esto incluye características del producto como el tamaño, el peso y las dimensiones, así como el historial de pedidos, los patrones de demanda y cualquier otra información que pueda influir en el almacenamiento y la selección de artículos. Para tomar decisiones bien fundadas en materia de asignación de huecos es necesario disponer de datos precisos y actualizados.
Análisis ABC
Tras recopilar los datos, el siguiente paso es realizar un análisis ABC. En él se clasifican los productos en función de su importancia y demanda. Normalmente, la clasificación se hace en tres categorías: A, B y C. La categoría A contiene productos de alta demanda y alto valor; la categoría B contiene artículos de demanda moderada; y la categoría C contiene cosas de baja demanda y bajo valor. Este análisis ayuda a priorizar la ubicación de los artículos en función de su importancia en las operaciones de almacén.
Aplicación de las franjas horarias
Una vez determinadas las configuraciones ideales de las ranuras, las alteraciones propuestas deben aplicarse en el almacén. Los artículos de alta rotación descubiertos tras la investigación se colocan en zonas de fácil acceso y frecuentadas. Se modifica la distribución del almacén para adaptarla a la nueva técnica de asignación de ubicaciones, garantizando que los productos estén correctamente colocados para su recogida y almacenamiento.
Control y ajustes
El procedimiento de asignación de franjas horarias no finaliza una vez asignadas las franjas. El rendimiento de la estrategia de asignación de franjas horarias debe supervisarse continuamente. Los responsables del almacén realizan un seguimiento de los tiempos de preparación de pedidos, los índices de cumplimiento de pedidos y otros parámetros relevantes para evaluar el éxito de los nuevos acuerdos de asignación de franjas horarias. Si los patrones de demanda u otros factores cambian, la estrategia de asignación de huecos se ajusta en consecuencia. Esta estrategia adaptativa garantiza que el almacén esté siempre optimizado para un funcionamiento eficiente.
Consideraciones relativas a las ranuras de los almacenes
Al adoptar un software/solución eficaz de asignación de huecos en el almacén, hay que tener en cuenta varios factores principales:
- Velocidad del producto: Investigue los datos históricos para identificar objetos de alta velocidad que deban colocarse en regiones de mucho tráfico.
- Almacenamiento: Tenga en cuenta las propiedades físicas de los productos a la hora de decidir las estrategias y ubicaciones de almacenamiento permitidas.
- Perfil del pedido: Comprenda los distintos tipos de pedidos que se suelen procesar (por ejemplo, pedidos individuales frente a pedidos masivos) y ajuste la estrategia de asignación de franjas horarias en consecuencia.
- Demanda estacional: Tenga en cuenta las variaciones estacionales de la demanda y ajuste en consecuencia sus estrategias de asignación de franjas horarias.
- Metodología de selección: Elija el método de picking óptimo (como picking por zonas o picking por lotes) y construya las franjas horarias en consecuencia.
- Cumplimiento de la legislación: Asegúrese de que los artículos peligrosos o frágiles se almacenan de forma segura y de conformidad con la legislación vigente.
- Desplazamientos de los trabajadores: Tenga en cuenta la estructura y las operaciones generales del almacén a la hora de optimizar los desplazamientos de los trabajadores.
Superar los retos de la asignación de ubicaciones en los almacenes
La asignación de huecos en los almacenes se enfrenta a varios problemas que deben resolverse para que las operaciones funcionen bien.
- Uno de los retos más comunes es la falta de datos. El acceso a datos correctos y actualizados es fundamental para una asignación eficaz de las franjas horarias, pero no siempre se dispone de ellos fácilmente, lo que puede dificultar la toma de decisiones.
- Otra cuestión es diversidad de productos en cuanto a forma y tamaño. Gestionar distintos tipos de productos puede dificultar la asignación de espacios, ya que cada artículo puede requerir soluciones de almacenamiento únicas.
- Luego viene la demanda dinámica. Las fluctuaciones de la demanda de productos pueden dificultar la elaboración de una estrategia coherente de asignación de huecos, ya que puede ser necesario modificar periódicamente la prioridad de almacenamiento de los artículos.
- Una dificultad clave es también la escasez de recursos. El espacio y los recursos limitados de los almacenes pueden dificultar la adopción de prácticas ideales de asignación de huecos, lo que obliga a desarrollar soluciones imaginativas para maximizar la productividad dentro de los límites.
Conclusión
La asignación de huecos en los almacenes es un componente vital para mejorar la eficiencia operativa de la cadena de suministro. Los almacenes pueden minimizar los costes de mano de obra, mejorar los índices de cumplimiento de pedidos y maximizar la utilización del espacio mediante la colocación estratégica de productos basada en datos. El uso de software para la asignación de huecos y el análisis periódico de los datos garantizan que las decisiones de asignación de huecos se adapten a las tendencias cambiantes de la demanda.
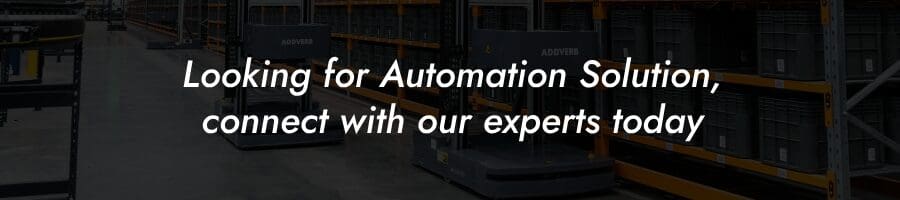
PREGUNTAS FRECUENTES
¿Qué es el slotting en un almacén?
La técnica de disponer las mercancías en zonas estratégicas para aumentar la eficacia de la preparación de pedidos y ahorrar costes operativos se conoce como slotting en almacén.
¿De qué manera aumenta la productividad la asignación de franjas horarias?
La asignación de franjas horarias acelera el cumplimiento de los pedidos organizando los productos en función de la frecuencia de la demanda, lo que reduce los errores de manipulación y el tiempo de desplazamiento.
¿Qué elementos influyen en la mejor asignación de ranuras?
El peso del producto, su tamaño, la frecuencia de picking y el tipo de almacenamiento son algunas de las variables. Para un acceso más rápido, los productos de mayor demanda se colocan más cerca de las zonas de picking.
¿Es posible automatizar la asignación de huecos?
De hecho, la asignación de huecos puede ajustarse automáticamente mediante robots y sistemas de gestión de almacenes (SGA) en respuesta a los niveles de inventario y la demanda actuales.
¿Qué ventajas ofrece el slotting eficiente?
Aumenta la eficiencia general del almacén, reduce los gastos de mano de obra, mejora la gestión del inventario y aumenta la productividad.