Inhaltsübersicht
With warehouse automated picking system accounting for up to 55% of total operating costs, selecting the right automated picking solutions is crucial for boosting efficiency, accuracy, and scalability in your operations.
Selecting the appropriate automated warehouse picking system can be helpful to achieve greater efficiency, accuracy and scale in your operations.
With the options of ASRS, AMRs, and pick-to-light, we need to ensure that the automated picking solution aligns with the size of your warehouse, order volume, or type of inventory. This blog will help you identify the best solutions, along with future growth.
Evolution of Automated Warehouse Picking System
The tale of automated warehouse picking system is a compelling story of development from completely human labor to the advanced robotic technologies of today. Prior to automation, warehouses relied on low tech, with all workers needing to memorize the locations of every product and walk for the product to pick it—an ordeal of fatigue, errors, and inefficient speed.
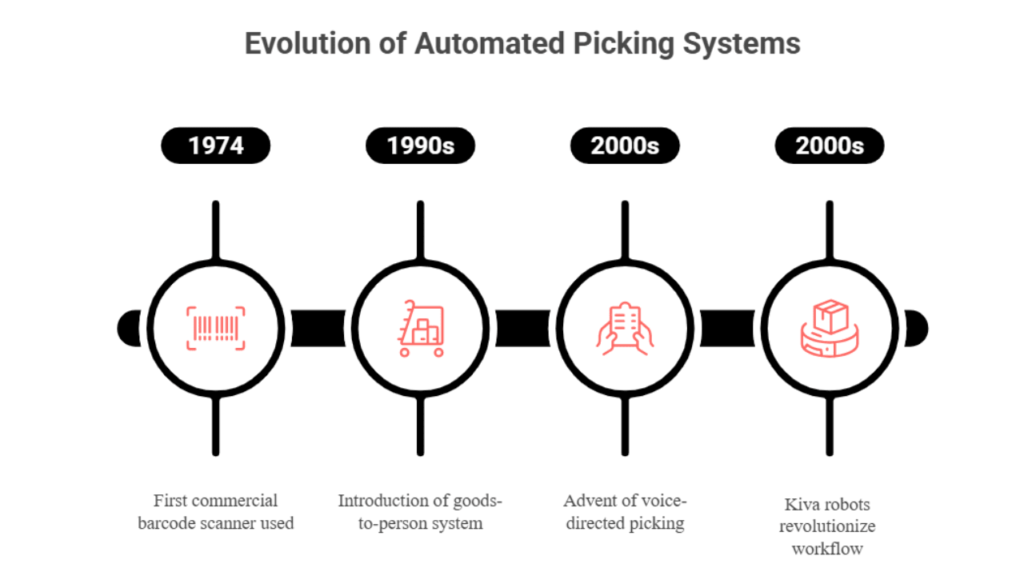
- This changed in 1974 when the first commercial barcode scanner was used at a supermarket in Ohio to scan a pack of Wrigley’s Juicy Fruit gum (the first scanned item).
- Fully automated picking did not occur until the 1990s when the first goods-to-person system was introduced.
- Change kicked into speedy gear in the 2000s with the advent of voice-directed picking, and then Kiva introduced their mobile robots that year (later purchased by Amazon) that revolutionized design and workflow by bringing the items to the worker rather than having the worker walk to the items.
- There are also automated picking management systems built on AI, computer vision, and robotics to provide flexibility to pick/identify/grasp/sort essentially any product while allowing pick errors to be reduced to nearly 99% of what manual pickers experience, all while processing order at shipment speeds and order that are not humanly possible to achieve.
Transforming Warehouse Efficiency with Advanced Automated Warehouse Picking System
In the logistical landscape of today, automated warehouse picking has emerged as an avenue to increased speed, accuracy, and space utilisation.
Each of the solutions in our offering is specifically designed to enhance and improve efficiency with automated warehouse picking. Here are a few ways in which we do this:
ASRS (Automated Storage and Retrieval System)
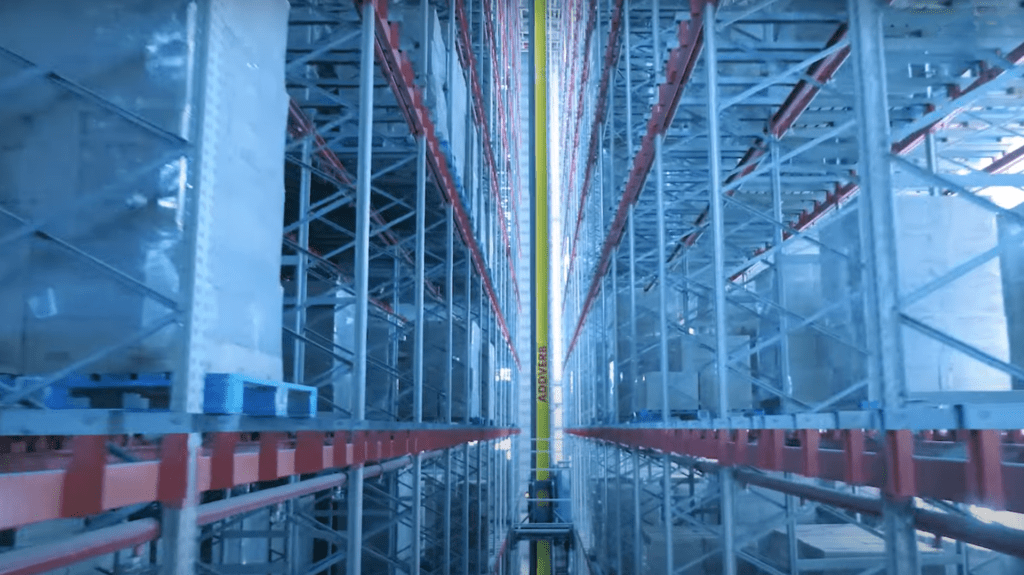
An ASRS is focused on the storage and retrieval of items. The first part of the retrieval process is for the system to retrieve the needed item from storage and then transfer it to a designated picking area.
Retrieval is defined as the system finding and bringing the item out of storage. The second step is the actual picking or automation taking place for order fulfillment or processing.
The foundation for automated warehouse picking, ASRS provides accurate inventory movement, drastically minimizing manual errors and allowing for high-speed, high-density storage. ASRS is the solution for large-order volume fulfilment centres.
HOCA (High-Speed Order Consolidation Automation)
Powered by Corzie
Addverb’s HOCA, powered by Corzie, is an advanced Horizontal Carousel System designed to streamline the storage and picking of small and medium-sized items. Its 180° shelf rotation delivers products directly to operators, ensuring faster and more accurate picking.
With a scalable design and flexible workstations, Corzie adapts to various industries, optimizing space utilization and enhancing operational efficiency. It’s the perfect solution for businesses aiming to improve throughput and accuracy in their warehouse operations.
Cruiser 360 (4-Way Pallet Shuttle)
When it comes to pallet-level automated warehousing technology, the Cruiser 360 stands out as a game-changer. Designed with a 4-way travelling shuttle, it seamlessly moves pallets across racked structures, offering unparalleled flexibility for modern warehouses.
Powered by smart battery technology and Wi-Fi-controlled operations, the Cruiser 360 ensures that pallet reorganization is not only fast and efficient but also exceptionally safe. With this innovative solution, warehouse operators can streamline their processes and stay ahead in today’s fast-paced logistics landscape.
Multi-Pro (Mother Child Shuttle)
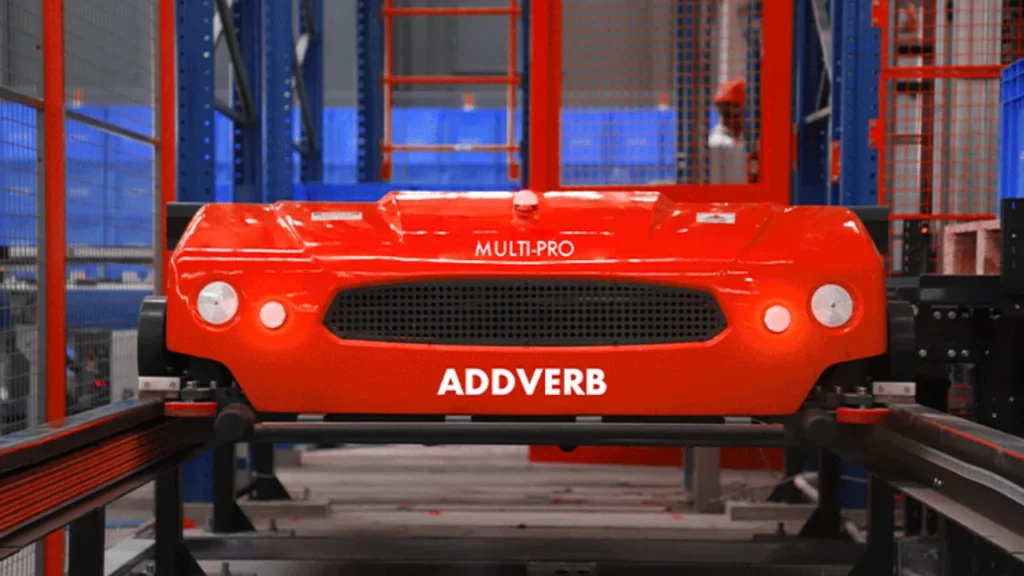
Built for vertical scalability, Multi-Pro enables automated warehouse order picking in multiple tiers, allowing access and order picking to happen simultaneously while optimizing density within a warehouse.
Quadron (Carton Shuttle)
Designed to be most effective for automated warehouse order picking of small items, Quadron has the speed and accuracy to handle cartons and totes of any size in a warehouse while decreasing total picking time. Quadron can be integrated with Goods-to-Person (GTP) systems, which have the potential to decrease walking time and increase order accuracy.
Medius (Multi Level Shuttle)
Medius introduces intelligent automation to multi-level carton shuttle systems, redefining efficiency in warehouse operations. Designed for industries such as pharma, cosmetics, and electronics, Medius excels at low-volume automated picking, offering precision and reliability.
Equipped with AI-powered vision systems, Medius ensures high levels of accuracy and efficiency in handling cartons across multiple levels. This advanced technology is tailored to meet the unique demands of industries that require both speed and precision, making it a critical solution for modern warehousing.
Person-to-Goods: Empowering Automated Warehouse Picking System with Precision
Addverb’s Person-to-Goods solutions are targeted to improve operator productivity, reduce errors, and increase speed via technology-guided picking.
Pick by Voice for Enhanced Automated Warehouse Picking System
Zesty, a pick by voice solution from Addverb reimagines the approach to automated warehouse picking by providing verbal instructions to guide the operator.
The operator wears a light-weight headset and orders are delivered in real-time with commands that engage the operator and allow them to remain hands-free, instead of relying on a printed list or a printed screen with a list.
- Enhances picking accuracy through clear, step-by-step directions.
- Perfect for fast-paced environments and rapid SKU changes.
- Improves productivity by allowing workers to remain focused and mobile.
Pick to light – A Blend of Speed and Simplicity with Rapido
Rapido, a Pick-to-Light solution, from Addverb reimagines automated warehouse picking by leveraging visual light signals to bring clarity to an operator’s picking motion.
The light will illuminate the location and quantity of an item to be picked, allowing for unparalleled speed and near-zero error.
- Achieves a throughput of 500 order lines/hour
- Perfect for batch, wave, and multi-order picking
- Faster training times and increased operator confidence
Light-directed automated warehouse picking, like Rapido, brings an unmatched level of accuracy required in e-commerce, pharma and fast moving consumer goods (FMCG).
Revolutionizing Warehouse Operations with ASRS and BRISK GTP Technology
In today’s fast moving logistics and warehousing market, speed, accuracy, and efficiency are paramount. That’s where Automated Storage and Retrieval Systems (ASRS) married with BRISK—Addverb’s intelligent Goods-to-Person (GTP) picking station come into play. The integration of ASRS and BRISK not only revolutionizes storage, retrieval, and picking, but also elevates traditional warehousing methods into flexible, high-performance routines.
Key Takeaways: Automated Storage and Retrieval (ASRS):
- Automates the storage and retrieval of material.
- Provides retrieval of an item from storage before delivery to a GTP pick station.
- Maximizes space utilization, speeds order processing, and eliminates manual handling.
BRISK – Advanced GTP Picking Station:
- Developed around Natural User Interface (NUI) to reduce operator fatigue and time required to learn.
- Includes a 6400-lumen projector that projects pick instructions directly onto the workstation – there are no extra screens.
- Supports gesture-based control and real-time scanning with a Ring Barcode Scanner.
- Auto-calibrating with precision markers for fast set up and minimal disruption.
- Works equally well in the dark or well-lit spaces due to adaptable light features.
- Easily scalable or flexible across all industries, be it e-commerce, retail, pharma, 3PL, automotive, manufacturing and more.
Working in conjunction with ASRS, BRISK is changing the way we think about efficiency in the warehouse, increasing picking speed and accuracy, and providing a smarter, ergonomically friendly user experience.
How to Choose the Right Automated Warehouse Picking System?
- Order Volume & Throughput Requirements: If your warehouse fills high order volumes at a high rate each day, you might consider very fast “automated” warehouse picking systems like autonomous shuttles or mobile picking routes. These will allow you to pick quickly and accurately while reaching downtime.
- Type of Inventory: The characteristics of your inventory will be a factor in your decision, too. For smaller SKU’s, or stock-in-store items that are frequently picked and shipped, a light-directed or carton shuttling systems will work the best.If you are also handling large bulky items, or pallets in your operations, pallet shuttles or self-operating fork trucks may be better suited within an automated warehouse picking system.
- Space Utilisation: If you do not have a lot of physical space to work with, vertical solutions like multi-level carton shuttles or vertical autonomous storage and retrieval systems can allow you to optimize your storage footprint. Overall, an automated warehouse picking system should complement your storage, providing you with the capabilities to store more in less space.
- Integration with WMS/ERP: In virtually situations you’ll want a system that can create a data flow with your WMS/ERP. Real-time data flow where seamless operation can be achieved through an automated warehouse picking system will enhance the accuracy of your system.
- Scalability & Flexibility: Modular designs or Robots-as-a-Service (RaaS) solutions enable businesses to scale automation as they grow. Flexible systems adapt to changes in order patterns and inventory profiles, ensuring warehouses remain efficient and responsive to evolving demands.
Partner with Addverb for the Right Automated Warehouse Picking Systems
Selecting the best-automated warehouse picking system is not solely about automation; it’s all about creating a smarter, more responsive, future-ready warehouse operation.
At Addverb, we approach warehouse automation with a focus on state-of-the-art robotics, intelligent software, and industry know-how to offer you complete warehouse automation solutions, tailored to your needs.
Contact our team today to discuss which automated warehouse picking system will be best fit for your operation!
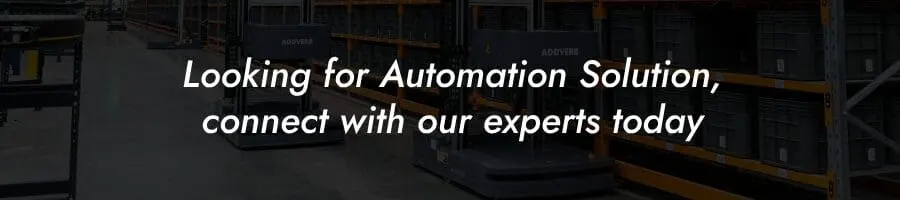