Inhaltsübersicht
Der Markt für fahrerlose Transportsysteme (FTS) zieht die Lagerhaltung an, da er bis 2028 auf 3,3 Milliarden Dollar anwachsen wird, indem er die Arbeitskosten senkt, den Durchsatz erhöht und die Sicherheit erhöht, da weniger manuelle Materialhandhabung erforderlich ist.
MärkteundMärkte
Was ist der Haupteinsatzbereich von FTS?
Die fortschrittlichsten Arten von fahrerlosen Transportsystemen werden als Sortierroboter oder Palettenroboter eingesetzt. Diese Roboter identifizieren, klassifizieren und trennen Artikel durch den Einsatz von Sensoren, Computer Vision und künstlicher Intelligenz in einer Weise, die den Betrieb effizient maximiert.
Ausgestattet mit Algorithmen des maschinellen Lernens verbessern diese Roboter ihre Sortiergenauigkeit schrittweise, da die Daten im Laufe der Zeit ausgewertet und die entsprechenden Prozesse mit der Zeit verfeinert werden.
Sie maximieren die Ressourcennutzung und leisten einen positiven Beitrag zur Nachhaltigkeit, indem sie eine höhere Recyclingrate und geringere Betriebskosten gewährleisten.
Wussten Sie das?
Dem McKinsey-Bericht zufolge sind 82 % der Bodenbewegung und des Materialtransports, 80 % der Warenannahme und -lagerung, 77 % des Materialtransports und der Gabelstapler und 75 % der Sortierung automatisiert.
Flexibler Sortierroboter
ZippyDer flexible Sortierroboter von Addverbrevolutioniert als hochwertiges fahrerloses Transportsystem (FTS) die Sortiervorgänge in Lager und Logistik. Er kann eine maximale Nutzlast von 40 kg handhaben und ermöglicht eine ultraschnelle Sortierung auf SKU-Ebene mit einer beeindruckenden Rate von bis zu 30.000 Sortierungen pro Stunde.
Dieses fahrerlose Fahrzeug nutzt intelligente Sensoren und KI-Algorithmen, um auf vordefinierten Pfaden zu navigieren und bestimmte Aufgaben ohne menschliche Hilfe auszuführen. Seine fortschrittlichen Fähigkeiten ermöglichen eine nahtlose Integration in bestehende Arbeitsabläufe und steigern die betriebliche Effizienz erheblich.
Zippy ist Teil einer vielfältigen Familie von Sortierrobotern, die verschiedene Traglasten (6, 10, 25 und 40 kg) und Konfigurationen (Schlepper, X) umfasst, die jeweils für unterschiedliche Sortier- und Materialhandhabungsanforderungen konzipiert sind.
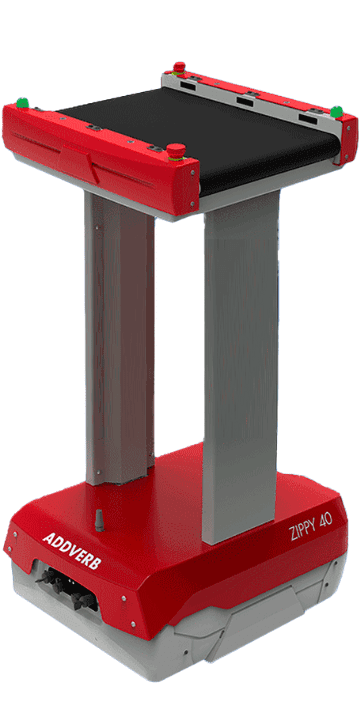
Lesen Sie mehr: 5 Gründe für die Wahl von Robotern für die Materialbewegung und -sortierung
Feststehender Roboter-Sorter
Dabei handelt es sich um ein Hochgeschwindigkeits-Sortiersystem, das unter der Bezeichnung SortIE bekannt ist und höchste Genauigkeit bei der Sortierung der einzelnen Pakete zu ihren Bestimmungsorten im Gleis auf verschiedenen Ebenen bietet.
Für große Unternehmen, die mit einer großen Menge an Waren handeln, ist SortIE ideal, um die Effizienz der Sortier- und Rückwärtslogistik sowie der Einlagerungsvorgänge zu steigern.
Das Ergebnis ist eine Senkung der Arbeitskosten, eine höhere Genauigkeit und eine Optimierung des Platzbedarfs.
Dieses fahrerlose Transportsystem ist für Unternehmen geeignet, die eine gute Sortierung, Organisation und Verwaltung von Schüttgut benötigen. Seine Anwendungen umfassen:
- Sortierung: Sie rationalisiert die Organisation und den Weg der Produkte, um den Arbeitsablauf zu verbessern und Fehler zu minimieren.
- Rückführungslogistik: Sie verbessert die Rücksendung und Sortierung von Produkten und gewährleistet eine effiziente Bearbeitung von Rücksendungen bei gleichzeitiger Eliminierung aller Kosten.
- Einlagern: Die Lagerung wird rationalisiert, da die Artikel an den richtigen Ort gebracht werden, ohne viel Platz zu verschwenden, wodurch der Bestand kontrolliert wird.
Die wichtigsten Vorteile von fahrerlosen Transportsystemen
Hochgeschwindigkeits-Sortierung
Leistungsmetriken: ZippyDie Fähigkeit des Systems, 30.000 Sortierungen pro Stunde durchzuführen, symbolisiert seine höchste Effizienz. Es bedeutet nur, dass eine genaue Sortierung auf SKU-Ebene minimale Abweichungen und somit eine bessere Bestandsverwaltung und mehr Kundenzufriedenheit gewährleistet.
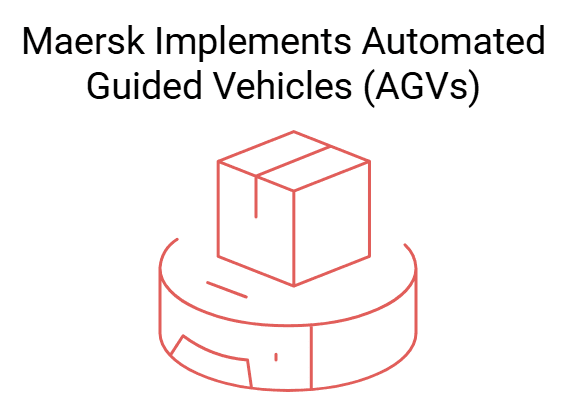
Steigerung der Lagereffizienz
- Verringerung der menschlichen Arbeitskraft: Durch den Wegfall sich wiederholender Sortierarbeiten Zippy reduziert das fahrerlose Transportsystem den Einsatz menschlicher Arbeitskraft und die Mitarbeiter werden für andere strategische Tätigkeiten eingesetzt.
- Schnelligkeit bei der Auftragsabwicklung: Die Hochgeschwindigkeitssortieranlagen von Zippy verbessern die Effizienz des Auftragsabwicklungszyklus und damit die rechtzeitige Lieferung.
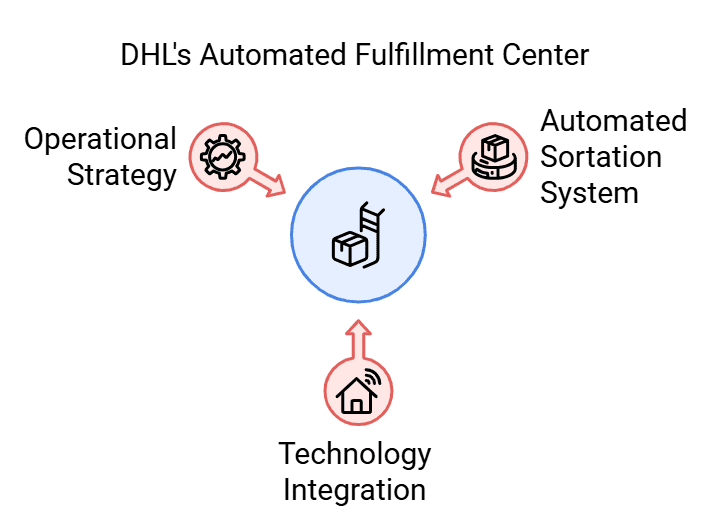
Rationalisierte umgekehrte Logistik
- Rückwärtslogistik: Zippy rationalisierte die Rückwärtslogistik und sortierte und leitete die Rückwärtsprodukte für weitere Prozesse weiter.
- Effizienz bei Kosteneinsparungen und Kundenzufriedenheit: Diese Automatisierung wirkt sich auf die Kosteneinsparungen aus, da sie die Betriebskosten senkt und gleichzeitig den Rückgabeprozess beschleunigt, was zu einem besseren Kundenerlebnis führt.
Insgesamt wirkt sich eine solche Automatisierung auf die Effizienz des gesamten Betriebs aus. Die große Zeitersparnis bei der Verarbeitung führt zu einem wesentlich höheren Durchsatz des Lagers und damit zu einer höheren Effizienz des gesamten Betriebs.
Nachteile von fahrerlosen Transportsystemen
Enger Spielraum bei der Navigierbarkeit
Die meisten fahrerlosen Transportsysteme arbeiten auf festen Routen, die keinerlei Flexibilität zulassen, vor allem nicht in Umgebungen, die sich schnell verändern. Ändert sich beispielsweise die Struktur des Lagers oder gibt es ungeplante Hindernisse auf dem vorgesehenen Weg des FTS, können die FTS Schwierigkeiten haben, umgehend eine alternative und effektive Route zu finden.
Infolgedessen kann es zu Verzögerungen bei der Bereitstellung von Diensten und zu Geschäftsunterbrechungen kommen. Solche Einschränkungen könnten sich als Hindernis erweisen, insbesondere in Umgebungen, in denen Schnelligkeit und Schnelligkeit gefragt sind.
Hohe Kosten
Für fahrerlose Transportsysteme sind erhebliche finanzielle Mittel erforderlich, um die Technologie zu erwerben und die erforderlichen Strukturen zu schaffen. Dies bedeutet den Kauf der physischen FTS, die Installation der Navigationssysteme und die Umstrukturierung der Räumlichkeiten, in denen sie eingesetzt werden sollen.
Für mehrere Unternehmen können solch hohe Anlaufkosten sie davon abhalten, in den Markt einzutreten, und dies gilt insbesondere für kleine Unternehmen, die nicht über die nötigen Mittel verfügen.
Herausforderungen bei der Wartung und Ausfallzeiten
Obwohl fahrerlose Transportsysteme in der Regel wie vorgesehen zuverlässig arbeiten, sind sie dennoch nicht wartungsfrei, wenn ihr Betrieb aufrechterhalten werden soll. Diese können zu Störungen im Betrieb führen, die wegen der Beeinträchtigung der Produktivität nicht erwünscht sind.
Da viele dieser Reparaturen und Wartungsarbeiten mit fortschrittlicher Technologie verbunden sind, könnte außerdem ein Bedarf an spezialisierten Arbeitskräften entstehen, was zusätzliche Kosten für die Verwaltung verursacht.
Wie kann Addverb helfen?
Wenn es um fahrerlose Transportsysteme geht, gehen wir bei Addverb über das Standardangebot hinaus und bieten maßgeschneiderte Lösungen mit fortschrittlichen Navigationssystemen.
Unsere fahrerlosen Transportsysteme arbeiten harmonisch mit anderen Robotersystemen, einschließlich Cobots, zusammen und sorgen so für einen reibungslosen Arbeitsablauf.
Es gibt auch die Option Robot as a Service (RaaS), mit der Unternehmen von hochentwickelten Robotersystemen profitieren können, ohne gleich erhebliche Investitionen tätigen zu müssen.
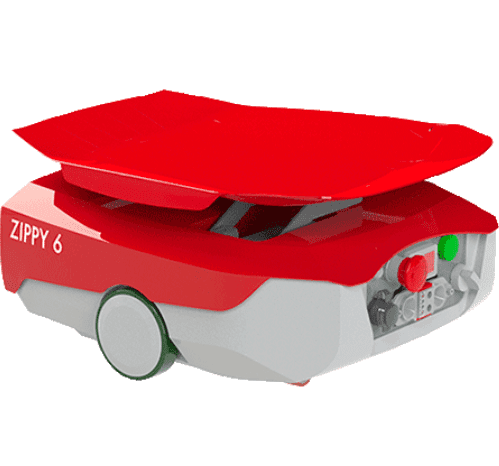
Ein solches Modell wird erfolgreich von Unternehmen wie Mondial Relay eingesetzt, um eine Skalierung des Geschäftsbetriebs zu ermöglichen und gleichzeitig ein geringes Kostenrisiko einzugehen.
Mit uns kann Ihr Unternehmen das Leistungsniveau erreichen, das auf dem heutigen Markt erforderlich ist.
Abschließende Überlegungen
Beim Einsatz von fahrerlosen Transportsystemen sind Herausforderungen wie begrenzte Anpassungsfähigkeit, hohe Anfangsinvestitionen oder Wartungsarbeiten zu erwarten.
Aber die bemerkenswerte Veränderung, die sie in der betrieblichen Effizienz bewirken, ist einfach unbezahlbar. Diese hochentwickelten Lösungen verbessern die Prozesse, minimieren Fehler und erhöhen die Effizienz der Arbeitsabläufe erheblich, weshalb sie für moderne Lager unerlässlich sind.
Bei Addverb nehmen wir jedes dieser Probleme als Herausforderung an und sorgen dafür, dass die Einführung und der Betrieb von fahrerlosen Transportsystemen für Sie einfach wird. Ihr Unternehmen profitiert von unseren maßgeschneiderten Lösungen, die sich an Ihren Bedürfnissen orientieren, von unserem starken Support nach dem Kauf und von modernster Technologie.
Wenn Sie mit Addverb zusammenarbeiten, brauchen Sie sich keine Sorgen zu machen, dass die Automatisierung zu Ineffizienzen oder unnötigen Ausgaben führt - Sie haben die Möglichkeit, alle Vorteile zu nutzen, die ein rationalisierter Prozess mit sich bringt.
Sind Sie bereit, Ihre Logistikprozesse auf die nächste Stufe zu heben? Kontaktieren Sie uns noch heute und entdecken Sie, wie wir Sie bei der Umgestaltung Ihrer Arbeitsabläufe unterstützen können!
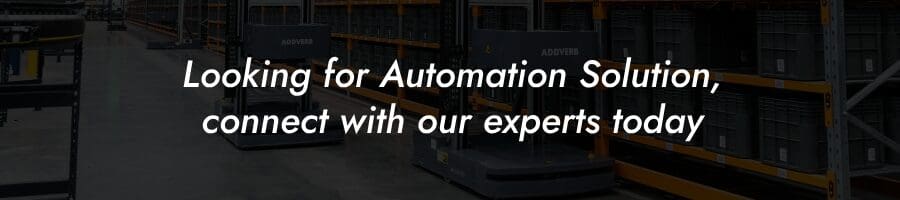
FAQ
Was sind Automated Guided Vehicles (AGVs)?
AGVs sind fahrerlose Fahrzeuge, die mit Hilfe von Navigationssystemen Materialien innerhalb einer Anlage effizient und sicher transportieren.
Was sind die Hauptvorteile von AGVs?
AGVs bieten erhöhte Produktivität, reduzierte Arbeitskosten, verbesserte Genauigkeit und erhöhte Sicherheit am Arbeitsplatz.
Welche Herausforderungen sind mit dem Einsatz von AGVs verbunden?
AGVs können hohe Anfangskosten haben, sind in dynamischen Umgebungen nur begrenzt flexibel und erfordern erhebliche Anpassungen der Infrastruktur für die Implementierung.