목차
The Automation in Chemicals Petrochemicals Market is expected to witness significant growth as the market is estimated to grow at a CAGRs from the year 2023 till the year 2032.
Is Your Chemical Warehouse Ready for the Future?
As stringent in the areas of safety, accuracy, and efficiency, chemical warehousing speaks of unique challenges. These challenges include hazardous material management and compliance with stringent regulations.
What if these problems had automation and innovative solutions as the answer? In this blog, discover these major areas of challenge in chemical warehousing and automation as an industry game-changing solution.
Key Challenges in Chemicals & Petrochemicals Warehousing
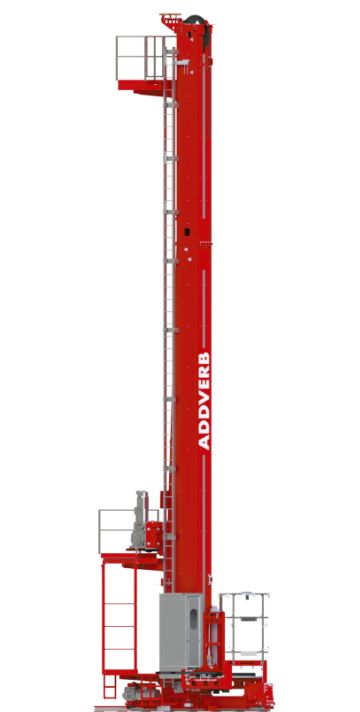
Handling Hazardous Materials and Safety Protocols
An effective safety measure needs to be adapted for handling possible hazardous chemicals is through containment ventilation and emergency response plans.
Complicated Intralogistics and Stacking Rules
Chemical warehousing products require sophisticated storage systems and effective intralogistics management due to their unique safety regulations and storage conditions. Improved automation and advanced tracking systems would support this, enabling secure storage operations.
Inability to Handle a Large Number of Products
The inability of skilled personnel to handle dissimilar and complicated chemical warehousing SKUs leads to inefficiency that can generate a safety hazard. Expertise is essential for efficient handling and compliance.
Compliance with Regulatory and Safety Standards
It is, in fact, the storage house that will comply with the very strict regulations at the local and international levels that will govern the handling, labelling, and storage of chemicals. Non-compliance would carry fines and legal harassment, besides many other effects like a tarnished reputation.
Common Warehouse Requirements for Chemicals & Petrochemicals
Storage Systems Security
Fireproof shelving and separated areas ensure safe, compliant storage of hazardous chemicals, preventing leakage and cross-contamination.
Accurate Material Movement Solutions
Automated systems and specialised equipment that handle import-export chemicals in an accurate way are required. This reduces both the risk and human error of handling these chemicals.
Sophisticated Software for Monitoring Stock Inventory and Regulation Maintenance
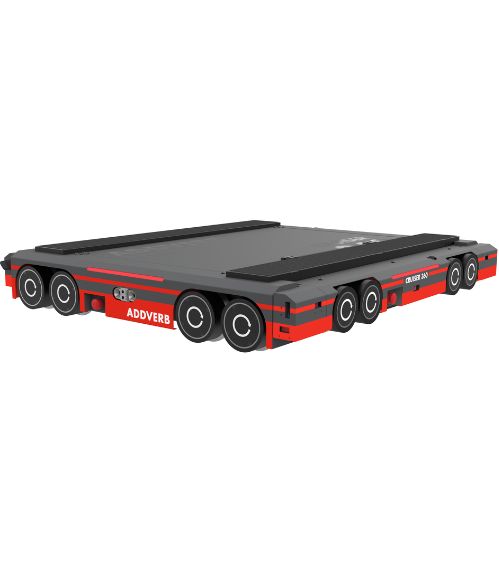
WMS and ERP software help in inventory-taking, regulating, and optimizing warehouse processes as they help in real time for safety and efficiency.
In 2024, the size of the global ERP software market was projected to be worth USD 64.83 billion and poised to witness a compound annual growth rate (CAGR) of 11.7% from 2025 to 2030.
Optimizing Chemical Warehousing with Automation Solutions
Advanced ASRS Solutions for Efficient Chemical Storage and Retrieval
ASRS designs tailored high-density storage and retrieval systems for chemical warehousing. The multi-pro-shuttle system greatly boosts throughput by automating the storage and retrieval of items.
The Cruiser 360 pallet shuttle, on the other hand, stores pallets in a safe, dense way that lets inventory be tracked in real time over Wi-Fi.
The Skyron stacker crane is generally capable of handling loads of up to 1500 kg without compromising proper utilisation of storage space AND continuous monitoring of inventory levels.
Such solutions would make a difference in space optimization, safety, and inventory management in a chemical warehousing.
Enhancing Material Movement with Autonomous Mobile Robots
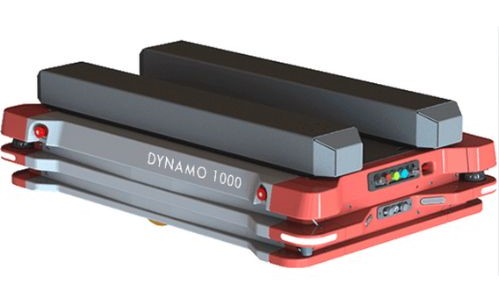
Dynamo is the most versatile autonomous mobile robot (AMR) tailored for optimizing chemical warehousing material movement.
The strong chassis of Dynamo, reliable LiDAR sensors, and compact design allow Dynamo to traverse through very complex warehouse environments deftly while transporting chemicals of a hazardous nature.
Advanced algorithms and artificial intelligence have been fitted into the Dynamo, which can completely automate the movement of chemicals such that human error is reduced and improves order fulfilment speed while always maintaining safety standards for the critical materials to be transported in time.
Enhancing software efficiency in chemical warehousing with Optimus
Optimise WMS by Addverb is an excellent solution specifically engineered to facilitate the entire warehousing operations for chemicals. It makes movement within the internal warehouse happen seamlessly, where hazardous chemicals would be entering or exiting the warehouse and optimally utilised with all resources and material flow.
In a nutshell it helps in real-time inventory monitoring, enhances accurate visibility into stock levels and would help in avoiding stock outs or overstocks.
Why Chemicals & Petrochemicals Automation is Required?
Safety Compliance Improvements: With its monitoring-in-real-time capability, this feature could also help in ensuring that the monitoring systems are within regulatory limits over a particular time span as well as allowing for a quick response during emergencies.
Minimising Human Error while Maximising Operational Efficiency and Enhancing Process Safety: This would limit the effects of human error regarding chemicals and allow proper storing and retrieving. Conducting processes with speed and safety will ensure productivity, reduce downtime, and ultimately increase overall operational efficiency.
Enhanced Traceability and Inventory Control: Real-time levels and movements of inventories actually help automate inventories more accurately. Better traceability, fewer stock-outs, less regulatory compliance imposed, and better handling of hazardous materials are some advantages of extensive automation.
Case Study: Wooster Brush Company
Situation: Wooster Brush Company – a firm with a manual paper selection process that was faced with inefficiencies, with operations, devolved into fulfillment errors and unsafe work practices.
Aim: WBC aimed at optimizing material flow while streamlining order fulfillment, throughput enhancement, and improved safety and accuracy in their warehouses.
Action: With Addverb, WBC developed their present solution with 13 Autonomous Mobile Robots used for picking and palletizing activities together with automated pallet de-stacking and stacking, all coordinated by Addverb’s Fleet Management System.
Result: The solution increased productivity while decreasing manual labor since it minimized safety risks and improved order accuracy, providing greater efficiency and customer satisfaction.
최종 생각
The challenges of chemical warehousing, namely safety and compliance, efficiency, and inventory management, require automation.
Using autonomous robots and cutting-edge smart software, Addverb has pioneered advanced solutions for streamlining operations, using material handling methods that reduce human error.
Visit Addverb for more information on bringing cutting-edge technology to your warehouse and making that warehouse more productive but also safer and more efficient in the future.
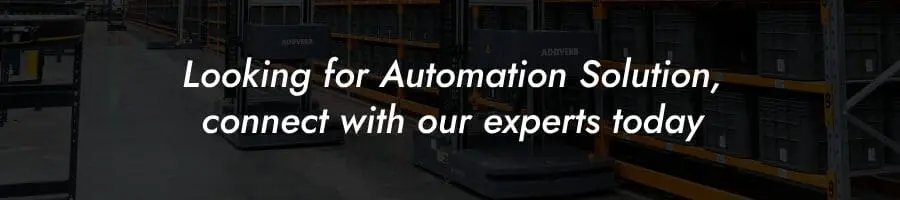